The FAULHABER Series 3274 BP4 Brushless DC Motor from MICROMO
A Flyweight with Heavyweight Performance
In the fight for high performance with minimum weight, FAULHABERs 3274 BP4 is the new champion in the ring. The brushless DC servo motor, measuring 32 mm in diameter and 74 mm in length, has massive continuous torque of 165 mNm. Surprisingly, it weighs in at just under 320 g, which is half the weight of conventional motors with comparable power.
The four‐pole brushless DC servo motor is ideal for applications in which high power and dynamic start/stop operation with the lowest possible total weight is an important factor. Perfect application fits include humanoid robots, electric grippers used in process automation and high‐performance traction drives used in inspection robotics.
The 3274 BP4 is overload‐resistant and operates without wear‐prone mechanical commutation. As a result, its operational lifetime is many times longer than that of a conventional DC micro motor. The slope of the motor characteristic curve is just 3 rpm/mNm, with a stall torque of 2.7 Nm. The 3274 BP4 can reliably deliver what the application demands even under the harshest ambient conditions, such as at low temperatures or high mechanical loads (e.g. in aerospace applications). This is made possible by a robust stainless steel housing and the omission of adhesives, which are otherwise usually used for assembly.
One standout feature of this motor series is the high flexibility in its design. The FAULHABER series 3274 BP4 is equipped as standard with digital hall sensors. High‐resolution optical and magnetic encoders can be attached with ease to the rear multifunction flange. As an option, the motor is also available with analog (linear) hall sensors that can replace an encoder in many applications. Finally, a large selection of optimal performance precision gearheads rounds off the complete drive system.
Contact the MICROMO Team today and learn more.
Featured Product
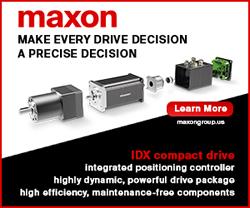
The maxon IDX Compact Drive with Integrated Positioning Controller
The compact brushless EC-i motor combined with an EPOS4 positioning controller delivers a highly dynamic, powerful drive package with field-oriented control (FOC), high efficiency, and maintenance-free components in a high-quality industrial housing. The maxon IDX drives are suitable for use across the entire speed range (from standstill to maximum speed) and have an extremely high overload capability. Together with a positioning controller, the integrated sensor (single turn) enables absolute positioning.