Panasonic Showcased the New AC Servo Motor and Other Smart Factory Solutions at the 17th China International Industry Fair
Serves as a show window for the world, and a platform for economic exchange and for promoting collaboration.
SHANGHAI--The 17th China International Industry Fair was organized at the National Exhibition and Convention Center (Shanghai) from November 3 (Tuesday) to 7 (Saturday), 2015. Panasonic showcased new industry products and solution including the newly developed AC servo motor, "MINAS A6 series," and laser welding robot system, "LAPRISS."
[Flash Video] #CIIF 2015 Panasonic Smart Factory Solutions Lead the Evolution of the Manufacturing Industry
https://www.youtube.com/watch?v=1rvR4zsxpFo
This tradeshow, first organized in 1999, has evolved over the past 16 years to become more specialized, more market-oriented, and global. It is also certified by UFI (Union of International Fairs), the Global Association of the Exhibition Industry, and it has come to be known as the most influential exhibition for the industrial system industry in China. Moreover, it also serves as a show window for the world, and a platform for economic exchange and for promoting collaboration.
As Panasonic shifts its axis to B2B, it has become especially active in the Chinese market. And at this exhibition, Panasonic focused its efforts to augment understanding for and recognition of both products and brand, "Smart Factory Solutions," including industry robots, automation technologies for production lines, PLC, and sensors.
The newly developed AC servo motor of the "MINAS A6 series" stays abreast with the reduction in size and weight of manufacturing equipment and also meets the demand for higher precision control and performance. Its excellent performance and resolution, low vibration, and its compact and robust body drew a crowd at the exhibition. Panasonic also introduced other new products such as the programmable controller FP-XH, inverter MK300, CMOS type micro laser distance sensor HG-C series. It also showcased solutions such as the laser welding robot system, "LAPRISS," and the intelligent arc welding robot system, "Active TAWERS" demonstrating its ability to make a comprehensive proposal from "Smart Factory Solutions" to "FA Solutions."
At the press conference, Hidetoshi Osawa, Managing Executive Officer of Panasonic Corporation and Regional Head for China and Northeast Asia emphasized how the growth of the B2B business holds the key to achieving the 10 trillion yen sales target by 2018, Panasonic's 100th anniversary. He also explained how Panasonic aims to introduce more rapidly, innovations in factory automation for the manufacturing industry, and continue to provide new products and solutions that meet clients' needs.
Furthermore, Hiroyuki Aota, Executive Officer of Panasonic Corporation and Vice President of Automotive and Industrial Systems Company voiced Panasonic's confidence in China's Smart Factory Solution market. "The Smart Factory Solutions we are proposing have the largest market share in China, and our sales in 2015 amounted to 45% of all global sales. Through our factory automation solutions, we will continue to help address many issues our clients face and contribute to the manufacturing industry in China."
Automotive and industrial systems form an integral part of Panasonic's B2B business. Panasonic will accelerate initiatives for the B2B business by continuing to develop technologies and propose solutions in these fields that the market desires and thereby support China's ever-developing manufacturing industry.
Featured Product
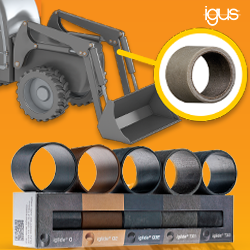
igus® - Free heavy-duty plastic bearings sample box
The iglide® heavy-duty sample box provides a selection of five unique iglide bearings, each suitable for use in heavy-duty equipment due to their self-lubricating, dirt-resistant properties. Each bearing material boasts unique benefits and is best suited for different application conditions, though each can withstand surface pressures of at least 11,603 psi at 68°F.