Velodyne 3D LiDAR Sensors Sweep Top Five Spots in China's Intelligent Vehicle Future Challenge
Inspired by DARPA Grand Challenge, 7th Annual IFVC is ‘Velodyne Country, With Its LiDAR Sensors Guiding 17 of 20 Entries; Full Product Line Represented
Morgan Hill, CA November 30, 2015 -- Coming tantalizingly close to a clean sweep, Velodyne LiDAR sensors were literally everywhere during the Intelligent Vehicle Future Challenge (IVFC) Nov. 16 in Chinas Changshu city - an event showcasing autonomous vehicles in action. Fully 17 of 20 competitors relied on real time multi-channel 3D LiDAR sensors from industry leader Velodyne - and the top five finishers all used Velodynes groundbreaking HDL-64.
Inspired by the DARPA Challenge, the IVFC is now in its seventh year, combining a conference dedicated to self-driving vehicles and a competition along a varied 13-kilometer course. The IVFC, underwritten by the National Natural Science Foundation of China, aims to advance perceptions of the natural environment and decision-making for unmanned vehicle platforms. Wei Weng, Velodyne Director of Asia Sales, addressed that theme in his presentation to the future roboticists in attendance.
Among the field of 20 teams, drawn from universities and research entities with some corporate sponsorship, the Military Transportation University contingent again took first place. Hailing from Tianjin, China, the MTU team won for the second consecutive year using Velodynes HDL-64 as its core sensing technology. Although the HDL-64 sensor was the winning technology, Velodyne is working to provide similar functionality in a form factor and at a price suited to the automotive industry. The company is scheduled to deliver the new sensor to automotive OEMs in the first quarter of 2016.
Changshu city, Jiangsu Province, is home to an economic development zone created specifically to promote the automotive industry. The IVFC course included urban, off-road and highway settings, with teams offered the option of skipping the off-road setting. Vehicles were judged on "4S" -- safety, speed, "smartness" and smoothness. The 2015 contest added a new challenge: passing other vehicles, mirroring interest in automated driving lane change features beginning to take hold in the automotive industry.
"For off-road settings, Velodyne LiDAR was the critical sensing technology to simultaneously localize, map and plan a path through the unstructured environment," Weng said. "This grueling challenge put each LiDAR sensor in our product line -- the 16-channel VLP-16 LiDAR Puck and the 32-channel HDL-32E, as well as the HDL-64 - through a series of rigorous real-world tests. Were delighted that the HDL-64 was able to assist the top five finishers in such a substantial way, and that Velodyne was able to contribute to the education and outcomes of a dozen other teams."
About Velodyne LiDAR
Founded in 1983 and based in Californias Silicon Valley, Velodyne Acoustics, Inc. is a diversified technology company known worldwide for its high-performance audio equipment and real-time LiDAR sensors. The companys LiDAR division evolved after founder/inventor David Hall competed in the 2004-05 DARPA Grand Challenge using stereovision technology. Based on his experience during this challenge, Hall recognized the limitations of stereovision and developed the HDL-64 high-resolution LiDAR sensor. Velodyne subsequently released its compact, lightweight HDL 32E sensor, available for many applications including UAVs, and the new VLP-16 LiDAR Puck, a 16-channel real-time LiDAR sensor that is both substantially smaller and dramatically less expensive than previous generation sensors. Market research firm Frost & Sullivan has honored the company and the VLP-16 with its 2015 North American Automotive ADAS (Advanced Driver Assistance System) Sensors Product Leadership Award. Since 2007, Velodynes LiDAR division has emerged as the leading developer, manufacturer and supplier of real-time LiDAR sensor technology used in a variety of commercial applications including autonomous vehicles, vehicle safety systems, 3D mobile mapping, 3D aerial mapping and security. For more information, visit http://www.velodynelidar.com.
Featured Product
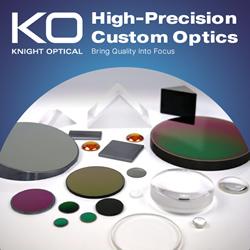