Kinema Systems Announces World's First Self-Training Robot Picking Solution
Kinema Systems is proud to announce its first product - Kinema Pick - the worlds first self-training, self-calibrating software solution for robotic depalletizing.
MENLO PARK, Calif.--(BUSINESS WIRE)--Kinema Systems is proud to announce its first product - Kinema Pick - the worlds first self-training, self-calibrating software solution for robotic depalletizing. Kinema Pick enables fully automated depalletization of multi-SKU, single-SKU and random pallets of boxes. Kinema Pick is self-training - it requires no manual training for the type of boxes to be picked or the workcell that the robot is operating in. Kinema Pick can be easily configured using a browser-based GUI. Kinema Pick is the first in a series of solutions from Kinema Systems for the "holy grail" of industrial robotics - random picking. Kinema Pick addresses a critical need in the e-commerce, logistics and distribution industry for robotic picking solutions capable of dealing with unstructured random pallets of boxes.
About Kinema Systems
Kinema Systems is a robotics startup in the Silicon Valley building advanced robotic manipulation applications. Kinemas founders are veterans of Willow Garage and SRI who created some of the most popular open-source software for robotics including MoveIt!, ROS-Control and Rviz, now used by hundreds of companies, researchers and universities around the world on robots ranging from industrial automation systems to humanoids. Kinemas team includes perception experts who have built scalable, real-time solutions to large-scale object recognition and tracking problems and automation experts skilled in architecting and deploying large-scale systems. Kinemas long-term vision is to build easy to use software solutions for advanced robotic manipulation applications in industry and beyond.
Featured Product
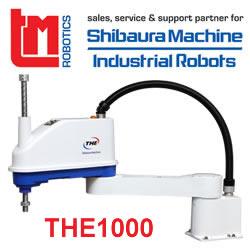