Microscan Hosts 3-Day Advanced Machine Vision Training Course
Microscan hosts a three-day training course June 7-9 in Nashua, NH, using advanced machine vision tools with hands-on exercises using Microscans advanced Visionscape® Machine Vision Software platform.
Microscan, a global technology leader in barcode, machine vision, verification, and lighting solutions, announces a three-day training course on advanced machine vision tools taught with hands-on exercises using Microscans advanced Visionscape® Machine Vision Software platform. The course will be held in Microscans Northeast Technology Center in Nashua, NH, U.S.A., June 7-9, 2016 at 8:30 AM to 4:30 PM daily. Attendance is free and online registration is available for all users; recommended for those with intermediate to advanced experience in machine vision or programming.
Part of Microscans Certified Training program, this three-day machine vision training course offers an in-depth study of Microscans complete vision tool library available in its advanced Visionscape® Machine Vision Software. Training will provide an overview of common machine vision applications with hands-on exercises to familiarize attendees with setting up inspection tools and programming jobs to solve a range of tasks from basic barcode reading and text recognition to complex measurements, defect detection, and guidance. Microscan machine vision technology experts will be available to offer one-on-one guidance on attendees specific applications and attendees are invited to bring their parts or barcodes to the event to discuss with the Microscan team.
To register for this training course or request additional training, visit http://www.microscan.com/training.aspx.
About Microscan
Microscan is a global technology leader in precision data acquisition and control solutions serving a wide range of automation and OEM applications. Founded in 1982, Microscan has a strong history of innovation that includes the invention of the first laser diode barcode scanner and the Data Matrix symbology. Today, Microscan remains a technology leader in automatic identification and machine vision with extensive solutions for ID tracking, traceability, and inspection, ranging from basic barcode reading to complex machine vision inspection, identification, and measurement.
As an ISO 9001:2008-certified company recognized for quality leadership in the U.S., Microscan is known and trusted by customers worldwide as a provider of quality, high-precision products. Microscan is a subsidiary of Spectris plc, a leading supplier of productivity-enhancing instrumentation and controls.
Featured Product
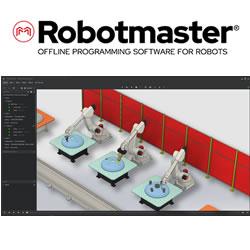