High precision is the key to the future of robotics
With the UK's first robotics week taking place in June 2016, Graham Mackrell, managing director of Harmonic Drive UK, looks at how high precision gears will be as vital for the advancement of the robotics sector.
Its no secret that the UK is lagging behind the rest of the world when it comes to both innovation and uptake of robotic technology. While large robots have been widely seen in industrial or manufacturing settings since the 1970s, the current trend in Asia and America for smaller, collaborative robots has barely made a dent in the British marketplace.
The global market for service and industrial robots is estimated to reach $59.5bn by 2020 and the UK has identified robotics as a technology thats key to its future growth. To this end, the government has launched several initiatives, such as the first annual robotics week in June 2016, launching special interest group RAS2020 to focus on improving the robotics and autonomous systems sector and investing £400m in driving robotics innovation.
Whether or not you believe that robots are coming to take your job or are just excited at the prospect of technological advancement, the age of the robot is upon us. The way we use robotic technology is going to change dramatically and this evolution is entirely dependent on high precision components.
Robots are now being designed with collaboration in mind, bringing them out of isolation and integrating them into the human workforce in a variety of settings, including both the production line and the operating theatre. This close proximity to and interaction with people is driving the need for increased accuracy in terms of functionality, when being used for intricate tasks such as surgery for example, as well as reliable reactions should an incident, such as a collision with a person, occur.
High precision gears in robot arms, such as those designed by Harmonic Drive, ensure reliability and safety. After all, it doesnt matter how reliable a robot's sensors are if the robot arm itself cannot stop before causing damage or doesnt respond as expected to commands. Strain wave gears like ours allow for highly accurate movements that can be repeated time and time again with perfect precision and zero backlash. This level of accuracy and repeatability affords peace of mind that collaborative robots can be relied upon to react to their surroundings and perform as required.
Essentially, high precision gears are the robotic equivalent of televisions transistors. However, unlike television, innovators in the robotics sector arent waiting around for their transistor - its already waiting for them. The key to growing the UKs innovation in robotics is high precision gears; inventors and original equipment manufacturers (OEMs) simply need to take advantage of it.
Featured Product
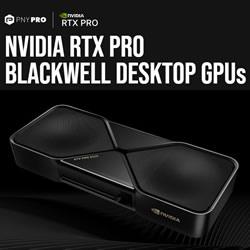