Festo Emphasizes Industry 4.0 and Smart Manufacturing at Manufacturing in America 2017
The revolutionary Siemens/Festo Multi-Carrier transport system that enables mass customization is on display within the Siemens pavilion.
HAUPPAUGE, NY, March 17, 2016 — Festo showcases the power of Industry 4.0 to improve flexibility and productivity while lowering costs at Manufacturing in America, March 22-23, in Detroit. At the event, Festo and Siemens will demonstrate the Multi-Carrier System, a mass customization transport solution. Festo will provide strategies for smart manufacturing during presentations on Wednesday and Thursday afternoon. The company features its innovative VTSA valve terminal at the Festo exhibit #212 - one product delivering a host of automation solutions.
The Multi-Carrier System enables the customization of batch sizes as small as one. By employing RFID technology and task-specific automation stations, products and product variations can be produced on a single manufacturing line quickly and efficiently. The Multi-Carrier System features zero changeover time and embodies Industry 4.0 manufacturing concepts of modularity, communications, and diagnostics. Each transport carrier - square pucks conveying products - moves freely and independently from all other carriers. Positioning accuracy for carriers is rated at 50 microns. The carriers in this product transport system move collision-free at constant velocity from station to station.
On Wednesday and Thursday at 1 p.m. in meeting rooms Nicolet B and Brule B, respectively, Nuzha Yakoob, Festo Corporations Senior Product Manager for Advanced Motion & Mechatronics, presents Paradigm Shift Towards Smart Manufacturing. She covers technologies that are available today to build smart production lines with the advantages of economies of scale and scope that embrace the concepts of Industry 4.0. To maximize the flow and re-use of data throughout the enterprise, smart manufacturing technologies are integrated at three levels — product, production line, and enterprise.
At Festo exhibit #212, company representatives will discuss productivity enhancement potential through efficiency, security, competency, and simplicity. Key attributes include:
• Proper sizing and selection of products
• Function integration, including safety - PROFIsafe - and IO-Link
• Design tools that simplify user experience, helping to bring products to market faster
• Support through custom solutions and industry specialists
Festo will have the VTSA valve manifold on display at exhibit #212. The VTSA is the most flexible pneumatic valve system on the market today with the ability to mix and match valves of different sizes. Flexibility enables automakers and Tier One suppliers to cut energy usage by selecting the most efficient compressed air flow rate without adding bulky and costly transition plates. The VTSA system offers more than 10 valve functions - the highest number on the market - in four different flow rates. This gives machine designers the utmost flexibility in creating pneumatic circuits. The modular system also enables simple modification and reconfiguration.
Festo is recognized as the most advanced electric and pneumatic motion actuation supplier, delivering unsurpassed product solutions, services, support, and quality. Festo fields two teams of automotive application specialists and supports all major control architectures.
For more information call 800-993-3786 and visit www.festo.com/us.
###
About Festo
Festo is a leading manufacturer of pneumatic and electromechanical systems, components, and controls for process and industrial automation. For more than 40 years, Festo Corporation has continuously elevated the state of manufacturing with innovations and optimized motion control solutions that deliver higher performing, more profitable automated manufacturing and processing equipment.
Connect with Festo: Facebook, LinkedIn, Twitter and YouTube
Featured Product
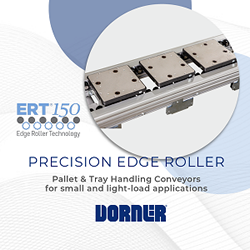