Mission to Mars
Barrett and Draper Team To Harden the Ultraminiature Puck® Motor Controller for NASA JPL's Next-Generation Mars Rovers
Newton and Cambridge, MA, USA - A robot equipped for the rocky terrain of Mars isn't your average robot. It needs space-hardened electronics, the kind that can withstand the harsh conditions of rocketing into orbit, surviving the radiation-filled expanse from Earth to Mars, colliding with the Martian surface, and then operating continuously for months and years to explore the red planet. Such a robotic system needs to be rugged, lightweight, and miniaturized in ways that go beyond the capabilities of the best systems designed for Earth.
Barrett Technology has long understood the value of lightweight, miniaturized, powerful electronics for robotics. Inside every robot that Barrett produces is a patented power-electronics module called the Puck®. There is one Puck for each motor inside Barrett's WAM® arms and BarrettHands™, and these Puck-driven robots are in operation in 18 countries across six continents. The Puck reads motor position down to 0.09º and up to 14,000 RPM and then controls motor-winding currents with nanosecond timing to apply precise torque, position, speed, acceleration at each axis. Barrett's newest Puck application, BURT™, is an FDA-Registered, Class-II robotic medical device designed to accelerate neuromuscular recovery after a stroke.
Barrett first designed the Puck to improve the torque precision in motors that drive its gear-free™ robots. It turns out that the same technology that boosted performance also enables extraordinary miniaturization. The latest version, P3™, is the size and weight of a penny, nearly one-tenth the size of the smallest brushless-DC servomotor controller available, and it has extreme performance capabilities.
Barrett has just been selected for Phase-II under NASA's highly-competitive Small Business Innovation Research (SBIR) program, opening the door to begin space-hardening Barrett's Puck. The company had earlier executed a Phase-I SBIR contract to study the feasibility of using the Puck to support NASA JPL's Mars Rover missions, for both locomotion and manipulation.
Space-hardening power electronics, and especially the dynamic power electronics that drive motors, can be a challenge because they are the most vulnerable piece of electronics in any robotic system. Barrett turned to Draper because of Draper's experience with space systems dating from the first Apollo moon landing to more recent missions including the Space Shuttle, the International Space Station, DreamChaser and two satellite servicing programs: Restore-L and Robotic Servicing of Geosynchronous Satellites (RSGS).
Under the Phase-II contract, Barrett and Draper will subject the Puck to several types of radiation including gamma/X-rays for general circuit degradation and high-speed particles, like energized protons, for latch-up single-event failures in key components like the power MOSFETs. They also will test the performance of P3 under severe extremes of temperature and vibration and under vacuum and partial vacuum. The results will help optimize the design.
Draper's innovations in microelectronics, materials engineering and microfabrication have impacts across industries and technologies. In addressing the consumer technology market, Draper is helping semiconductor manufacturers overcome crosstalk and low signal integrity in their wirebond microelectronics packaging through an innovative technique that connects chips without substrates. In neurotechnology, Draper is developing a transistor-less neural stimulator, that, once implanted in the brain, has the potential to successfully treat a variety of neurological disorders, as well as mental health conditions. Draper facilities in Cambridge include a microfabrication center, microelectromechanical systems (MEMS) facility, polymer fabrication, precision machine shop and a Center for Additive Manufacturing.
About Barrett Technology
Barrett is a pioneer in high-performance robotic arms and hands, such as its WAM® arm
and BarrettHand™, for emerging applications requiring superior versatility. Barrett has pioneered advanced motor controls, for example its Puck, to enable the best force-controlled performance available. When combined with its gear-free™ transmissions, these systems are in a league of their own. Barrett's latest robot, named BURT™, is an FDA-Registered Class-II medical device that immerses the user in a rich haptic field and enables unencumbered zero-gravity reaching in all directions. A research edition of BURT is available for researchers in advanced robotics who need a haptic-development platform that enables large motions.
About Draper Laboratories
At Draper, we believe exciting things happen when new capabilities are imagined and created.
Whether formulating a concept and developing each component to achieve a field-ready prototype or combining existing technologies in new ways, Draper engineers apply multidisciplinary approaches that deliver new capabilities to customers. As a not-for-profit research and development company, Draper focuses on the design, development and deployment of advanced technological solutions for the world¹s most challenging and important problems. We provide engineering solutions directly to government, industry and academia; work on teams as prime contractor or subcontractor; and participate as a collaborator in consortia. We provide unbiased assessments of technology or systems designed or recommended by other organizations-custom designed, as well as commercial-off-the-shelf.
Featured Product
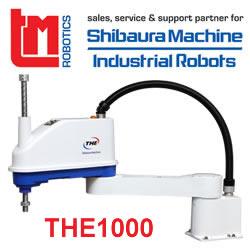