Tennplasco Invests in Rethink Robotics' Sawyer Robot, Sees Return in Under Four Months
To combat growing labor shortages and deliver solutions for the automotive industry, manufacturer deploys smart, collaborative robot
BOSTON - August 22, 2017 - Tennplasco, a plastic injection molding company, solved its labor shortage and met its return on investment just three and a half months after deploying Rethink Robotics Sawyer at its Lafayette, Tenn. facility. With Sawyer, Tennplasco has increased its productivity and efficiency, giving the company a competitive advantage in the injection molding market.
"Like many other manufacturers out there, we have been really struggling to get workers in our factory, especially on the off shifts. The truth is, there are not a lot of people in our area looking for injection molding jobs, and if we dont have people showing up to work, we cant operate," said Danny Rose, General Manager at Tennplasco. "With Sawyer, we dont have to worry about whether the shift will be staffed, and we can stop wasting our time and effort on trying to recruit nonexistent labor."
Easy to deploy with minimal training necessary, Sawyer integrated seamlessly with Tennplasco employees and helped the team design a more efficient work cell. Tennplasco uses Sawyer to deliver solutions and supply key manufacturing components to support the demanding, global automotive industry. Sawyer is currently being used on the assembly line, helping to assemble and inspect automotive parts. Automotive component productions such as sensors, defrosters and electronics are ideally suited for collaborative robots, and Tennplasco is one of many leading manufacturers using Sawyer for these types of tasks.
"For small- to mid-size manufacturers, selling the CFO on the cost of deploying automation can be a challenge. Our team was willing to try it, and with Sawyer, we reached our ROI in just three and a half months," said Rose. "Our customers, especially those in the automotive industry, trust us to support their businesses and meet their changing needs, but to do this, we need both workers and the technology to be innovative and nimble - Sawyer has made that possible."
Founded in 1985 in Carthage, Tenn., Tennplasco, a division of Manar Inc., offers plastic injection and molding services and plastic product solutions. In the future, Tennplasco plans to deploy Sawyer on a variety of injection molding tasks on off shifts to further help solve the labor shortage they continuously face.
"Globally, manufacturers are facing labor shortages; in fact, Deloitte projects a shortage of two million factory employees by the year 2025," said Jim Lawton, chief product and marketing officer at Rethink Robotics. "Sawyer gives companies like Tennplasco the tools to stay innovative and competitive in a world where customers have changing needs, and manufacturers need to minimize uncertainty."
For more information, please visit www.rethinkrobotics.com.
About Rethink Robotics
Rethink Robotics is transforming the way manufacturing gets done, with smart, collaborative robots able to automate the 90 percent of tasks that until now, have been beyond the reach of traditional automation. Its Baxter® and Sawyer robots, powered by the Intera software platform, adapt to real-world variability, can change applications quickly and perform tasks like people do. The result: manufacturers of all shapes, sizes and industries get the fast-to-deploy, easy-to-use and versatile automation solution they need to increase flexibility, lower cost and accelerate innovation.
Based in Boston, the Rethink product suite is available in Asia, Europe and North America. The company is funded by Bezos Expeditions, CRV, Highland Capital Partners, Sigma Partners, DFJ, GE Ventures and Goldman Sachs. For more information about Rethink Robotics, please visit www.rethinkrobotics.com and follows us on Twitter @RethinkRobotics.
Featured Product
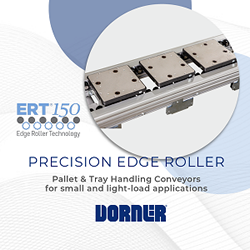
The ERT150 - Dorner's Next Evolution of Edge Roller Technology Conveyors
The next evolution in Dorner's Edge Roller Technology conveyor platform, the ERT®150, is ideal for small and light-load assembly automation, as well as medical and medical-device assembly application. The ERT platform is the only pallet conveyor of its kind available with an ISO Standard Class 4 rating for cleanroom applications. Earning the ISO Standard 14644-1 Class 4 rating means Dorner's ERT150 will conform and not contribute to the contamination of cleanrooms to those standards. As implied by its name, the ERT150 (Edge Roller Technology) uses rollers to move pallets through the conveyor smoothly with no friction (a byproduct often seen in belt-driven platforms). The conveyor's open design eliminates concerns of small parts or screws dropping into rollers and causing conveyor damage or jamming. The ERT150 is suited to operate in cleanroom environments requiring a pallet handling conveyor. It is capable of zoning for no or low-back pressure accumulation and is ideal for automation assembly applications within industries including medical devices, electronics, consumer goods among others.