Zimmer Group - Webinar -EPISODE 7 - New 5000 "AL" SERIES GRIPPERS
This is an invitation to attend our upcoming webinar. In this installment of our periodic webinar series, we would like to introduce exciting additions to our industry leading 5000 series grippers.
This is an invitation to attend our upcoming webinar. In this installment of our periodic webinar series, we would like to introduce exciting additions to our industry leading 5000 series grippers. We are rolling out versions with aluminum linear guides to complement the flagship steel guided models.
This expansion of our 2 and 3-jaw gripper lines offer considerable savings in the premium gripper market segment.
The 5000 series grippers were designed to be a truly universal gripper series and have 2-jaw , 3-jaw , angular , pneumatic, electric and IO-Link options.
Whether you are an end-user, distributor, integrator or machine builder, we feel that you can take some useful knowledge away from this 40 minute session and learn why we think this gripper series simplifies your gripper choice by offering more features including, higher forces, higher moments, and longer fingers than the benchmark, 30 million cycles maintenance-free and a fully sealed design.
AGENDA FOR EPISODE 7
Hosted by Costas, he will cover the following:
- Unique design features of the new "AL" aluminum 5000 series gripper
- Comparison of the "AL" models to current gripper offerings
- The simple part numbering of the grippers
- An overview of the flagship 5000 series
- A quick preview of the upcoming Assembly Show in Rosemont, Illinois
Featured Product
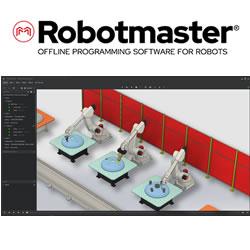
Robotmaster® 2024
Program multi-robot cells and automatically solve robotic errors with ease. Hypertherm Associates announces a new version to its robotic programming software. Robotmaster 2024 addresses key market trends including the support for programming multiple robots in a single work cell and the demand for automatic trajectory optimization and robotic error correction.