Realtime Robotics Partners with Siemens to Accelerate the Integration of Industrial Robotic Workcells
Realtime Robotics partners with Siemens to accelerate the integration of industrial robotic workcells. Realtime's technology is being seamlessly integrated into Tecnomatix® Process Simulate, simplifying robot programming and workcell coordination by automating motion programming. Manufacturers and integrators can now easily program, simulate, and validate automation, significantly simplifying the digital commissioning process.
Realtime Robotics, the leader in autonomous motion planning for industrial robots, today announced a strategic partnership with Siemens Digital Industries Software division. Realtime's technology is being seamlessly integrated into Tecnomatix® Process Simulate, simplifying robot programming and workcell coordination by automating motion programming. Manufacturers and integrators can now easily program, simulate, and validate automation, significantly simplifying the digital commissioning process.
Currently, multi-robot workcells take prohibitive amounts of calendar and scarce engineering time in the simulation phase before going to production. Once deployed, they are inflexible, requiring significant re-programming for every modification. This has made multi-robot workcells cost-prohibitive for all but the most stable high-volume manufacturing.
Siemens' industry leading Tecnomatix® Process Simulate, coupled with the Realtime Controller and RapidPlan software, significantly simplifies the programming of automated robotic processes, reducing the time to deploy and adapt to changes, both during simulation and on the shop floor. The integrated technology eliminates the need to enter teach-points and to create and manage interference zones.
Joint customer proof of concepts show programming cycle time reductions of over 70 percent, enabling quicker, more robust deployments.
Quotes and Commentary
"We are excited to announce our collaboration with Siemens. Our combined solution provides manufacturers with the flexibility and efficiency they have been clamoring for to expand the deployment of industrial automation. Together we will accelerate the pace of automation."
— Peter Howard, CEO, Realtime Robotics
"Our partnership with Realtime Robotics reflects a paradigm shift in the way robotic applications are programmed and deployed. Together we have created a unique value proposition that will open up a world of possibilities for robotic automation."
— Zvi Feuer, Senior Vice President MFE, Siemens Digital Industries Software
About Realtime Robotics
Realtime Robotics has developed a specialized processor to generate safe motion plans in milliseconds for industrial robots and autonomous vehicles. Its solution enables robots to function together in unstructured and collaborative workspaces, as well as react to dynamic obstructions the instant changes are perceived. Its solutions expand the potential of automation. Learn more about Realtime Robotics here and connect on Twitter and LinkedIn.
Featured Product
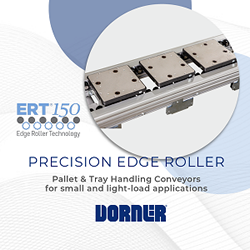