UltraFlex induction brazing copper tube to a rod within 40 seconds, at output power of 1600 F (871 °C)
In a recent test setup, UltraFlex Power Technologies demonstrated the speed and quality of induction brazing for manufacturing purposes.
In a recent test setup, UltraFlex Power Technologies demonstrated the speed and quality of induction brazing for manufacturing purposes.
The test setup had been requested by a potential customer - a leading manufacturer who needed to replace existing torch brazing methods to increase production volumes, consistency and repeatability. UltraFlex is a manufacturer of advanced digitally controlled induction heaters and frequently performs test applications for customers evaluating a switch to induction heating solutions.
The customer aimed at brazing 3000 pieces per month, with no rejects, which posed high requirements regarding the speed and quality of the brazing process. Considering the elements to be brazed - a 5/32" (3.96 mm) copper capillary type tube and a 9/16" (14.28 mm) electroplated rod - UltraFlex engineers considered UltraFlex induction heater from the UltraHeat SM series to be the perfect induction equipment for this case. UltraHeat SM is a compact 5kW induction heater which operates with either a water-cooled or air-cooled remote heat station. It can be very easily tuned to a wide range of loads and coils and its compact design can fit in any space.
The brazing process started by positioning the workpieces into a coil and clamping them together. Flux was applied at the brazing joint spot and brazing alloy was manually fed when the target brazing temperature of 1600 F (871 °C) had been reached.
At a power output of 4.5 kW, it took mere 40 seconds for the pre-programmed brazing to get completed. The evaluation of the brazing done proved the high-quality and reliability of the joints. The automation of the brazing process guaranteed that the customer would get consistent results if the brazing process would be implemented on the production line. Finally, thanks to this fast heating time, the target of 3000 brazed pieces per month could easily get reached.
This UltraFlex demonstration proved that by replacing torch brazing with induction brazing, all customer requirements for increased productivity and excellent quality could easily get met. In addition to being time-efficient, as well as cost-efficient, the induction brazing would be a completely safe process - both for the operator and for the environment, thanks to the lack of open flame, fumes and pollution.
Interested in finding out more?
Find out more at:
https://ultraflexpower.com/
Contact us at:
+1.631.467.6814
uptnews@ultraflexpower.com
About UltraFlex Power Technologies:
UltraFlex Power Technologies (ultraflexpower.com) offers the most advanced and innovative digitally controlled induction heating equipment in the industry. Its compact modular and flexible systems are suitable for a wide variety of induction heating, casting and melting applications.
Featured Product
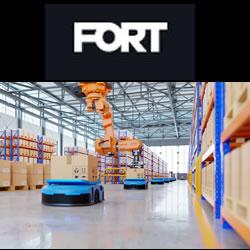
Fort Robotics - Avoid Costly Downtime with Safety & Security for Machines
Machine safety and security are two critical components of any industrial operation. Our latest video explores this question and provides insights into how security measures can enhance machine safety. Nivedita Ojha, VP of Product at FORT, breaks down the key considerations when it comes to securing your machines and keeping your workers safe, explaining why there is no safety without security.