MHS joins Robotic Industries Association to promote growth, adoption of advanced technologies
MHS, a single-source provider of material handling automation and software solutions, announces its membership in the Robotic Industries Association (RIA), the only trade group in North America organized specifically to serve the robotics industry.
(Mt. Washington, Ky.) Oct. 5, 2020 — MHS (www.mhsglobal.com), a single-source provider of material handling automation and software solutions, announces its membership in the Robotic Industries Association (RIA), the only trade group in North America organized specifically to serve the robotics industry. MHS will support RIA's efforts to advance industrial robotics through promotional and educational opportunities, integration and safety standards and more.
"We look forward to continuing our involvement with such a respected, trusted organization, whose mission aligns with our efforts to solve customer challenges with robotics and flexible automation," says Dean Terrell, Senior Vice President, MHS. "Our relationship will mutually serve both parties in speeding up time to market for all new robotics products while ensuring safe operation and a common knowledge center for industry standards, best practices, and robotics training for personnel."
MHS helped host the 2019 Autonomous Mobile Robot Conference, co-sponsored by the RIA and Association for Advancing Automation (A3), capping off the event with a tour of the company's 260,000-square-foot research and development facility and live demonstrations of automation technology for a range of logistics processes. MHS has also contributed to RIA's effort to define safety standards specifically for autonomous mobile robots (AMRs), which have previously operated under standards for automated guided vehicles established in the 1990s.
MHS offers both AMR and robotic work cell solutions to deliver value-added automation for supply chain customers. Earlier this year, the company significantly expanded its portfolio of AMR capabilities, providing access to a full lineup of transportation systems, including modifications for target applications like detachable carts, robotic arms, forklifts and conveyor supplements. Some examples of MHS robotic work cells include palletizing, each picking for order fulfillment and an innovative robotic singulation solution to precisely pick and place individual items to feed downstream automated systems.
About MHS
MHS Global is a full-service provider of innovative material handling systems that solve the challenges of distribution and fulfillment operations. We take a comprehensive, customer-centric approach that includes custom engineering, design, manufacturing and turnkey integration services. Our quality solutions leverage a broad range of controls and automated equipment, including but not limited to sorters, conveyors, extendable loading and unloading systems. We provide complete, responsive support to maintain systems for peak performance, with predictive analytics and local technicians to maximize long-term value and return on investment.
MHS has a global installed base of over $5 billion for small to large distribution and fulfillment projects in a variety of industries, including e-commerce, parcel, third party logistics and outside integrators.
# # #
Media contact:
Dan Gauss, Koroberi
336.409.5391
dan@koroberi.com
Company contact:
Lauren Pedley, MHS
502.645.6199
Lauren.Pedley@mhsglobal.com
Featured Product
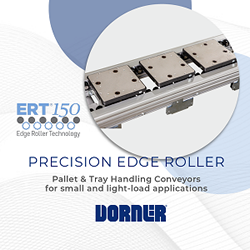