Soft Robotics Expands mGrip™ Modular Gripping System with New Features
IP69K Rating Provides Safe Handling of Proteins and Dairy Products
Soft Robotics Inc. announced today the expansion of the mGrip Modular Gripping System with new capabilities and an IP69K rating to enable safe food handling of proteins and dairy products. These new features put more capabilities into the hands of machine builders to design flexible end of arm tools that can withstand high-pressure washdown environments.
Launched in 2019, the mGrip system is a suite of configurable gripper and controller products that make reliable, high-speed picking of traditionally hard to grasp items possible. Today, with hundreds of systems in production globally, mGrip is addressing some of the hardest picking challenges for Fortune 100 companies in the food processing and consumer packaged goods industries.
Adoption of robotic automation in the protein and dairy industries has lagged behind other food segments due to the inherent variability and stringent hygienic requirements which often require food contact surfaces to be cleaned-in-place with high pressure solutions. "The needs of protein and dairy customers are unique and their automation options have been limited as a result," says Austin Harvey, Director of Product Management at Soft Robotics. "We've seen a lot of demand from the protein and dairy industries throughout the pandemic and we're excited to bring a new level of versatile and cleanable grasping solutions to our customers to help grow their businesses."
The expansion of the mGrip product line delivers four new capabilities designed to give machine builders more versatility when designing systems:
Deploy in washdown environments - All food grade mGrip grippers maintain IP69K compliance allowing for high-pressure washdown to further prevent food-born illnesses from stopping production.
Build custom tools - The newly released mGrip adapters and accessory interface give integrators greater flexibility, allowing them to rapidly prototype and build custom, production-grade tooling by combining Soft Robotics patented technology with other technologies such as part presence sensors or suction cups.
Pick smaller products - New, compact finger modules enable tighter grip spacing (down to 20mm) to improve picking performance for smaller items. These smaller, lighter finger modules result in lower mass tools which leave more robot payload for product handling, permit faster rates, and cause less system wear over time.
Pick flat products - Designed specifically for picking meat and poultry patties, the new angle-tipped fingers safely lift and grasp thin products from flat surfaces without damage.
"Simple, Clean, Reliable. These 3 words best describe why Soft Robotics tools have been the choice for us on a number of direct food handling projects," says Daniel Woodbridge, Mechanical Design Engineer at JMP Solutions. "With one of their IP69k grippers we are able to easily, and reliably, handle products of varying shapes and sizes while vastly reducing the number of parts and surfaces that would be required by a traditional mechanical gripper design. From raw meat to fresh buns, these tools have proven themselves to be the answer on many food handling projects."
About Soft Robotics
Soft Robotics is an industry-leading and award-winning technology company that designs and builds automated picking solutions using proprietary soft robotic grippers, 3D machine perception, and SoftAI™ artificial intelligence. The company's transformational robotic automation solutions enable machine builders to solve the hardest piece picking problems in growing automation industries like food processing, consumer goods production, and logistics. Learn more at www.softroboticsinc.com.
Soft Robotics is backed by leading venture capital firms and strategic investors that include Calibrate Ventures, Hyperplane Venture Capital, Material Impact, Scale Venture Partners, FANUC, ABB Technology Ventures, Honeywell Ventures, Tekfen Ventures, and Yamaha Motor Co., Ltd.
Featured Product
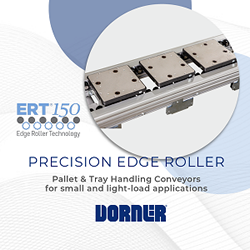
The ERT150 - Dorner's Next Evolution of Edge Roller Technology Conveyors
The next evolution in Dorner's Edge Roller Technology conveyor platform, the ERT®150, is ideal for small and light-load assembly automation, as well as medical and medical-device assembly application. The ERT platform is the only pallet conveyor of its kind available with an ISO Standard Class 4 rating for cleanroom applications. Earning the ISO Standard 14644-1 Class 4 rating means Dorner's ERT150 will conform and not contribute to the contamination of cleanrooms to those standards. As implied by its name, the ERT150 (Edge Roller Technology) uses rollers to move pallets through the conveyor smoothly with no friction (a byproduct often seen in belt-driven platforms). The conveyor's open design eliminates concerns of small parts or screws dropping into rollers and causing conveyor damage or jamming. The ERT150 is suited to operate in cleanroom environments requiring a pallet handling conveyor. It is capable of zoning for no or low-back pressure accumulation and is ideal for automation assembly applications within industries including medical devices, electronics, consumer goods among others.