hIOTron Presents a guide on five ways to improve manufacturing process with real-time monitoring
The reason smart manufacturing is being described as the next industrial revolution is that it arises in the wake of technological developments such as increased connectivity and remarkable access to and contextualization of data.
The reason smart manufacturing is being described as the next industrial revolution is that it arises in the wake of technological developments such as increased connectivity and remarkable access to and contextualization of data.
IIoT allows steaming data across various machines in the factory as well as facilities. This provides whole visibility across several operational processes, offering information about the failure of parts, etc. Manufacturers are capable to analyze data trends and recognize inefficiencies in processes, a drop in production or inefficient utilization of materials.
Real-time data allows manufacturers to run simulations to recognize the most effective manufacturing methods. With a concentration on the shop floor, real-time monitoring is proving to be an important aspect.
The fastest-growing manufacturers depend on real-time monitoring to search for new insights into how they can enhance and boost shop floor productivity and stand out in delivering customer requirements at the same time.
The quality management system is the technology being embraced by many manufacturers this year. The real-time analysis gives the data streams these QMS require to give new insights into minimizing the cost of poor quality, increasing yield rates and achieving higher performance.
Real-time monitoring tackle the tool issues and machine level minimizes hard fault errors, including tool breakage, tool presence and workpiece presence. In addition to that, it helps manufacturers to resolve soft faults attributable to machinery acceleration, temperature variation, vibration and force.
Real-time monitoring helps in analyzing energy consumption and finding waste in any production process and hence is important for achieving sustainability goals across all production centers.
Real-time monitoring allows the end-to-end visibility across production centers that is enabling medical device manufacturers to excel. The more complex the production process, the more reliance is on real-time data to minimize the incidence of production downtime because of equipment failures.
Links
To know update 5 Ways to Enhance Manufacturing process with Real-Time Monitoring , please visit us at: https://www.hiotron.com/real-time-monitoring-enhance-manufacturing/
About hIoTron
hIOTron provides a practical study for various IoT cloud platforms. Hiotron had deployed over 21000 IoT Devices. hIoTron's IoT Platform helps businesses to connect and manage data securely.
hIOTron offers an industrial solution over such a platforms with Internet of things Training Course which you can easily come up with a new ideas and techniques. Those training will be building up with the help of various techniques.
Featured Product
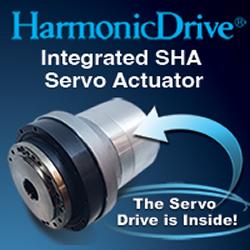
Harmonic Drive - Coming Soon! Integrated Actuators with EtherCAT®!
The IDT Series is a family of compact actuators with an integrated servo drive with
CANopen® and, coming soon, EtherCAT® . With high torque, exceptional
accuracy and repeatability, these actuators eliminate the need for an external drive and
greatly simplify cabling.