Supply Chain Issues Create Opportunities for U.S. Encoder Manufacturer
Within every challenge is opportunity.
Carlsbad, CA - Extensive slowdowns all along the supply chain are keeping electronics manufacturers from buying the components they need, when they need them, suggesting broader problems across the economy. However, for SMAC, a little encoder manufacturing group in Derry, New Hampshire, the crisis has led to record sales numbers in 2021.
"No one else on the planet can create prototypes as quickly as we can," claimed one SMAC Application Engineer. This statement may be difficult to verify, but certainly only a very select few can deliver price competitive encoder prototypes to U.S.-based companies as quickly as SMAC can.
SMAC setup their own Encoder manufacturing group SMAC-EMC, to design, build and test their own line of optical encoders. Their engineering and manufacturing staff have over 25 years' experience designing and building optical encoders at SMAC and at other major optical encoder companies. This staff has designed large volume, optical encoder products for Markem, Brooks Automation, Varian Corp, HP, Universal Instruments, Delphi and other manufacturers from coast to coast.
Because SMAC developed and designed their own reflective and diffractive optical encoder in-house, it has given them the knowledge and understanding of all the attributes that go into choosing superior encoder optical components for their designs.
Featured Product
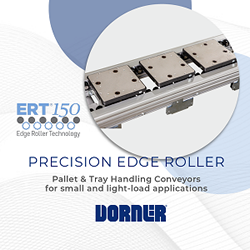
The ERT150 - Dorner's Next Evolution of Edge Roller Technology Conveyors
The next evolution in Dorner's Edge Roller Technology conveyor platform, the ERT®150, is ideal for small and light-load assembly automation, as well as medical and medical-device assembly application. The ERT platform is the only pallet conveyor of its kind available with an ISO Standard Class 4 rating for cleanroom applications. Earning the ISO Standard 14644-1 Class 4 rating means Dorner's ERT150 will conform and not contribute to the contamination of cleanrooms to those standards. As implied by its name, the ERT150 (Edge Roller Technology) uses rollers to move pallets through the conveyor smoothly with no friction (a byproduct often seen in belt-driven platforms). The conveyor's open design eliminates concerns of small parts or screws dropping into rollers and causing conveyor damage or jamming. The ERT150 is suited to operate in cleanroom environments requiring a pallet handling conveyor. It is capable of zoning for no or low-back pressure accumulation and is ideal for automation assembly applications within industries including medical devices, electronics, consumer goods among others.