HEIDENHAIN’s New “PressFit” Encoders for Small Motors
Designed to Support Automated Assembly
SCHAUMBURG, IL (April 2022) - With the introduction of the evolutionary PressFit rotary encoders from HEIDENHAIN, small-motor manufacturers finally have a better solution for incorporating automated mounting for feedback devices. This new ExI 11xx encoder series features a unique compact design that allows fast and simple mounting by press-fitting into a motor housing while still allowing surrounding space for cables and seals. HEIDENHAIN's PressFit encoders are made for integration into motors with a flange size as small as 40 mm x 40 mm or an axis height of only 20 mm!
Developed in collaboration with global motor manufacturers, HEIDENHAIN's new PressFit encoders include a "PressFit" flange that can be secured in a motor housing through a frictional connection, using a specially designed tolerance sleeve. This innovative system promises to support automation efforts by easing mounting requirements, leading to less mounting time being required.
HEIDENHAIN's new PressFit ExI 11xx encoders provide the following key technical benefits:
• Automatable mounting
• Faster installation
• Wide mounting tolerances
• Compact design
• EnDat 2.2 purely serial interface
• Functional Safety capability
About HEIDENHAIN
DR. JOHANNES HEIDENHAIN GmbH, headquartered in Traunreut, Germany, develops and supports motion control feedback solutions for the machine tool, semiconductor, electronics assembly and test, metrology, automation, medical, energy, biotechnology and other global markets. HEIDENHAIN employs approximately 6,000 people worldwide in its core business activities. The North American subsidiary is HEIDENHAIN CORPORATION, headquartered in Schaumburg, IL, and San Jose, CA, and has been serving the U.S. industry for over 50 years. Here nine company brands are represented. More information at: www.heidenhain.us/about-us
Featured Product
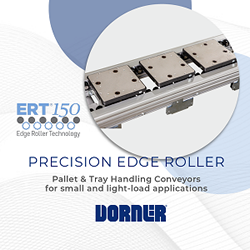