Study: AI Can Speed Up Car Seat Quality Inspection By More Than 27 Times
AI can significantly increase accuracy and reduce time for car seat quality inspection. EasyODM - a dedicated AI and Computer Vision software - was deployed at a production facility of a leading global car seat manufacturer. Over the course of two years, the software was able to reduce car seat inspection time to 2.2 seconds performing at overall accuracy of 99%.
AI can significantly increase accuracy and reduce time for car seat quality inspection. EasyODM - a dedicated AI and Computer Vision software - was deployed at a production facility of a leading global car seat manufacturer. Over the course of two years, the software was able to reduce car seat inspection time to 2.2 seconds performing at overall accuracy of 99%.
With area scan cameras installed on the production line, the system was able to identify such manufacturing defects as wrinkles, scratches, staining and creases. Defects could be attributed to a certain seat area and - depending on the manufacturing workflow - defected seats can be forwarded for automated robotic or manual defect removal.
"Manual seat inspection usually takes around 60 seconds. By utilizing AI, this process can be reduced to only 2.2 seconds on average. While manual accurate for simple defects or low volume production, human-performed visual inspections remain monotonous, time-consuming, and susceptible to fatigue-caused errors. AI introduces uniformity in quality control, operating at and even exceeding human levels of accuracy" - says CEO of EasyFlow Simas Jokubauskas.
EasyODM can easily adapt to support different seat models, layouts, trims and finishes. A premium car brand can offer more than 40 versions of seats across different product lines. Legacy car seat quality inspection software was developed to only work with a particular seat model, meaning that it needed to be calibrated to support new products. It was also not tolerant of manufacturing realities - for instance, that a seat for inspection could arrive slightly bent or a few centimeters off from the ideal inspection point.
EasyODM was developed to accommodate a diverse product portfolio and often imperfect manufacturing environment. At first the software identifies the seat in the image and isolates it from the background noise. Then - pixel by pixel - the software scans segments of the seat for defects, highlighting the affected regions in the image. The highlighted defects can then be forwarded for automated removal. After the elimination of defects, the software performs an additional quality check.
EasyODM was extensively tested at the facilities of one of the largest car seat manufacturers. With more than 250 manufacturing and assembly plants globally, the company provides services to leading automotive brands.
EasyODM was created by EasyFlow, an AI and Computer Vision software development house. EasyFlow develops AI applications for retail, construction and manufacturing industries.
Featured Product
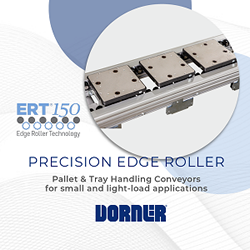