Manual programming preventing rapid rollout of robots for over half of US manufacturers
Over two-thirds are spending over a week preparing a robot to complete tasks
Indiana, US - October, 17th 2023 - Over half of manufacturers (52%) in the US say that time-consuming manual programming is required for robots to complete welding, cutting, painting or other tasks on the factory floor, according to new research by Visual Components, the developer of 3D simulation software.
Over two-thirds of manufacturers (73%) state that this process takes between a week and a month, with robots unable to complete automated tasks during this time. This isn't as severe of an issue in the UK with 35% stating the same, however in France almost all companies (98%) agree.
With excessive time needed to get robots up and running, utilization rates are poor among manufacturers, with an average of 34% reported. This is delaying the opportunity to bring products into production quicker, as they are unable to take care of the repetitive actions that humans are currently performing, with over a third of all processes falling under this description (35%).
One in four (26%) manufacturers are also being hindered by having three or more different robot brands on the factory floor, further complicating programming procedures. Over three in ten (32%) French respondents deploy three or more different robot brands.
With only 6% of manufacturers having had cobots (collaborative robots) in place for a prolonged period of time, fears among employees in the time taken to program them effectively may be preventing wider uptake, despite the benefit of cobots to achieve an error-free consistent production rate compared to human handling, removing the laborious tasks from people.
"Robots and cobots are highly valuable technologies in the factory environment, but manual programming is impacting on the ability of manufacturers to fully utilize their capabilities. Offline robot programming (OLP) allows operators to combine the planning and designing of a new robot work cell in a virtual environment. Offline programming avoids any disruption to production and ensures that robots get to work much quicker, leading to increases in productivity and output," said Mikko Urho, CEO, Visual Components.
***
About Visual Components
Founded by a team of simulation experts and amassing over 20 years in business, Visual Components is one of the pioneers of the 3D manufacturing simulation industry. The organization is a trusted technology partner to a number of leading brands, offering machine builders, system integrators and manufacturers a simple, quick and cost-effective solution to design and simulate production processes and offline programming offline robot programming (OLP) technology for fast, accurate and error-free programming of industrial robots. For more information please visit: https://www.visualcomponents.com/
Featured Product
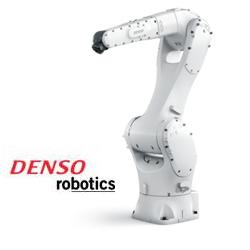
Denso Robotics - Newest 6-axis VMB Series offers longer arm reach and higher load capacity
The new VMB series represent some of the newest members to our 6-axis family of robots. These high-performance, versatile units offer a longer arm reach and a higher load capacity than traditional models which make VMB an excellent solution for palletizing, packaging, and material handling. New features include greater air piping, valve and signal line options, as well as new programming options with state-of-the-art functions using our new WINCAPS Plus software. VMB offers an IP67 protection grade along with meeting ISO Class 5, which makes them suitable for electric parts, food manufacturing processes, and pharmaceutical and medical devices. With the addition of the new VMB large robots, all manufacturing processes can now be automated by DENSO Robotics.