Universal Robots Responds to Demand and Doubles UR20 Cobot Production Ahead of Schedule
The UR20 has quickly become the go-to choice for manufacturers seeking a long-reach, heavy-payload cobot, prompting Universal Robots to double production capacity to meet customer needs.
Novi, Michigan, November 15, 2023: Universal Robots, the global leader in collaborative robotics, announced today that high demand for its new UR20 cobot has led the company to accelerate production timelines. The UR20 has quickly become the go-to choice for manufacturers seeking a long-reach, heavy-payload cobot, prompting Universal Robots to double production capacity to meet customer needs.
"We are thrilled by the tremendous response to the UR20. The rapid adoption by manufacturers speaks volumes about the impact this cobot is having on the industry," says Bryan Bird, President of Americas at Universal Robots. "In response to the demand, we have made the strategic decision to ramp up production faster than initially anticipated."
The UR20 is the first in Universal Robots next generation of industrial cobots designed to take performance to new heights while embracing the UR hallmarks of versatility, usability and small footprints. With a 1750 mm reach and 20 kg payload capacity, UR's next-generation cobot handles more tasks, fits more applications, and assists in more environments than ever.
UR20 order fulfillment in Q4 still possible
As Universal Robots accelerates UR20 production, the company emphasizes that there is still available capacity to fulfill orders in Q4. To encourage manufacturers to take advantage of end-of-year tax incentives, Universal Robots encourages businesses to submit their cobot orders promptly.
"We understand the urgency for businesses to optimize their operations and take advantage of available tax incentives," added Bird. "By doubling UR20 production ahead of schedule, we aim to ensure that our customers can access the benefits of collaborative automation without delay."
Early success at Bob's Red Mill and Ornua
The cobot's success is underscored by the experiences of prominent companies such as Ornua and Bob's Red Mill, who have already integrated the UR20 into their manufacturing processes. Bob's Red Mill, a historic whole grain manufacturer, looked for many years to use collaborative robots for palletizing tasks, but had not found a solution meeting the speed, payload, or reach requirements until the release of the UR20. The new, larger cobot from Universal Robots now successfully meets required cycle times, freeing up four operators while helping propel company growth.
"We had been eyeing UR cobots for a long time; we appreciate the simplicity, their track record and the out-of-the-box features," says Nick Chow, Engineering and Fabrication manager at Bob's Red Mill.
Ornua Ingredients, part of Irish Dairy co-operative Ornua, has now deployed the UR20 cobot in end-of-line palletizing, one of the business' most labor-intensive operations.
"We looked at palletizing as the first area to deploy automation due to the number of human resources we required," comments Jack Cotton, Continuous Improvement Lead, Ornua. "When we learned about what the UR20 could do, we were excited by the capabilities, both in terms of the capacity it could lift and the arm reach, which were perfect for the delicate products we required support for. The benefits of its deployment have been nothing short of brilliant, with increases in consistency and productivity boosts very clear to see."
Manufacturers interested in integrating the UR20 into their operations are encouraged to contact Universal Robots to discuss their specific automation needs and explore the possibilities offered by the UR20 cobot.
Featured Product
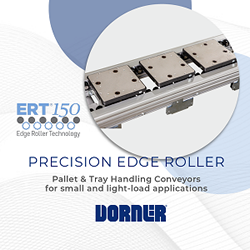