Redefining CNC robot programming - Tezmaksan’s RoboCAM transforms the landscape of industrial automation
Developed by Tezmaksan's software team, RoboCAM is a program used to control and monitor robotic operations, significantly reducing the time spent instructing the robot. The platform is designed to eliminate the complexities of robotics programming, making it accessible to operators of all skill levels.
Tezmaksan Robot Technologies, a leading European manufacturer of robotics and automation, has introduced a new CNC robot programming software platform, RoboCAM. The software is designed to modernise and simplify the role of robot operators, making automation engineering more accessible to individuals with varying levels of programming expertise.
Developed by Tezmaksan's software team, RoboCAM is a program used to control and monitor robotic operations, significantly reducing the time spent instructing the robot. The platform is designed to eliminate the complexities of robotics programming, making it accessible to operators of all skill levels.
"RoboCAM's interface is designed to be user friendly, both for seasoned professionals and those who are new to automation," said Hakan Aydogdu, general manager at Tezmaksan. "Many sectors already benefit from the use of RoboCAM — such as automotive, casting, aviation and metalware manufacturing."
RoboCAM was initially developed to control Tezmaksan's own robot automation system, the CubeBOX, a modular solution designed to automate production without human operators. However, RoboCAM has since emerged as a versatile software solution compatible with all robotic CNC machines.
A key breakthrough achieved with RoboCAM is that the software can create 3D models of workpieces. By converting 2D CAD drawings into 3D CAM instructions, RoboCAM streamlines the design manufacturing process. This function removes the need for programming and extensive CAM knowledge, as well as the need for specialised training.
In addition, RoboCAM's easy to use interface makes its possible to easily create transportation scenarios — where the robot moves objects or materials from one location to another — while taking into account part sizes and floor layout. It is also possible to record and reuse robot movement positions.
More recently, Tezmaksan has launched RoboCAM+, the latest version of the intelligent software. The new platform is designed for an easy set up, and with the capability to read and work seamlessly with Drawing Exchange Format (DXF) files. The latter function means operators can effortlessly upload and monitor designs for enhanced customisation and flexibility.
Tezmaksan's robotic CNC automation solutions are designed to elevate production in machine shops," added Aydogdu. "The RoboCAM software streamlines robotic programming and operation, catering to users of all skill levels, making automation engineering more accessible and efficient across various industries."
To learn more about how RoboCAM can improve manufacturing processes, visit the Tezmaksan Robot Technologies website.
Featured Product
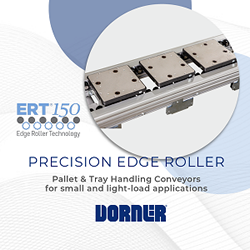