How Robotics Has Helped The Tank Cleaning Industry
Before robotics, cleaning hazardous and non-hazardous waste from industrial tanks fell to the responsibility of field workers who put themselves at great risk. Crawling into tight spaces became a job no one particularly wanted, and for obvious reasons.
Falls, burns, oxygen deprivation, loss of consciousness, and even fatalities are a common risk of industrial tank cleaning. We’re on a mission to turn that around. Here’s how we’re doing it.
New Industry Standard
The need for human employees to enter confined and hazardous spaces can and should be eliminated. Industrial workers already put themselves at risk during their regular jobs. Entering tanks can increase their risk of injury or even death while on the job.
Rather than continue to place employees in harm’s way for a job that robots can do, the robotics industry is coming in and saving lives.
Robot tank cleaners are creating a new wave of employee safety. They are utilized to complete dangerous tank cleanout while an employee controls every movement of the robot in the safety of their workspace outside the tank.
Robots can enter any tank that a human can fit into and clean the entire thing without requiring the presence of a human in the tank itself.
Increased Safety
Tank cleaning injuries and deaths are, unfortunately, a very present reality. They occur so frequently that industry initiatives are calling for a complete end to confined space entry by 2025. We’re taking that seriously.
Safety is perhaps the greatest contribution robotics has produced in the world of industrial tank cleaning. If an employee isn’t required inside the tank, there is no risk of injury from the process.
For hazardous and non-hazardous materials alike, Robots can complete the job from start to finish, assisted by an employee operator within the safe confines of their workspace. Robots are so thorough that there is no reason for your employees to enter at any time during the cleaning process.
Increased Cost Savings
Your employees are the most valuable part of your company. There is no reason for them to face needless risk when they can operate a robot to do the job of the cleanout, instead.
Robot cleanout will not only save your employees time during the cleanout job itself but will cut down the time it takes them away from the rest of their job. Using robotics for tank cleanout will increase employee productivity across your company.
While:
Some companies will find they are best served by purchasing tank cleaning robotics systems outright, there is also the option of renting.
If your company only infrequently requires tank cleanout, then utilizing a leasing program may be the ideal way to keep your employees safe and save your company time and money.
A Better Workplace
Robotics is changing the tank cleaning industry for the better. No longer are employees needed to put themselves at risk of injury or death when robots can be used instead.
Not only is the tank cleaning job completed efficiently and safely, but employees can spend more time at the rest of their job, increasing company-wide efficiency and cost-savings. Are you ready to give robot tank cleaners a try?
Comments (0)
This post does not have any comments. Be the first to leave a comment below.
Featured Product
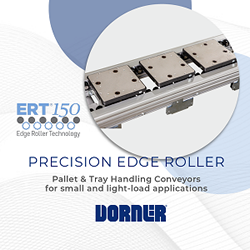