Job loss was on everyones mind. Results showed that the opposite took place. Higher quality led to more orders and an increase in the number of jobs.
Contributed by | The Association for Advancing Automation
Customer demands seemed unrealistic and competitors were making gains. Danish manufacturer Trelleborg Sealing Solutions had to find a way to overcome challenges. Automation held promise but the company had space limitations and a search for a proper solution took more than a decade.
While other manufacturers were enjoying results, answers eluded Trelleborg. Discover the major change that took place and how automation has become the key to recent growth.
Facing Uncertainty
Trelleborg’s customers rely on the o-rings, gaskets, rotary shaft seals and other related products to keep their machines performing critical tasks. Competition was making life uncomfortable for the manufacturer and customers kept seeking lower prices, higher quality, and faster delivery times.
If Trelleborg couldn’t comply then business would be lost. Inefficiencies seemed built in to the supply chain. Trelleborg’s overseas factories provided low wage labor but getting to market quickly was a problem.
“We’re faced with a constant demand for increased efficiency on all fronts,” said Jesper Riis, Trelleborg’s head of production.
Making the Choice
After digging for answers, Riis said in the video segment that Trelleborg settled on robotic arms from Universal Robots. This form of automation fit within space limitations and was programmable to handle small, customized orders and perform efficiently to make several million units.
The benefits to the company were clear, but the move to automation raised concerns among the company’s employees. Job loss was on everyone’s mind. Would they be among the popularized statistics of workers losing their jobs to robots? After all, Trelleborg was discovering that its move allowed them to make more accurate parts and keep costs competitive.
Results showed that the opposite took place. Higher quality led to more orders and an increase in the number of jobs.
Trelleborg’s experience is shared by other manufacturers that have found the solution to meet their needs. The video shows the robotic arms at work, states the improvements in production and highlights the benefits to the workforce. It also reveals the timeframe for the company’s return on investment.
The content & opinions in this article are the author’s and do not necessarily represent the views of RoboticsTomorrow
Comments (0)
This post does not have any comments. Be the first to leave a comment below.
Featured Product
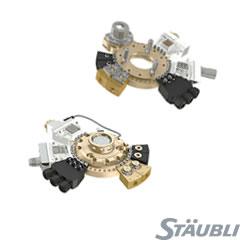