Autonomous Machine Vision (AMV) is a new approach to quality assurance, designed to be more than automatic, but autonomous, from determining the ideal number of samples the system needs to learn the characteristics of an item.
Reliable Quality Inspection of Plastics With Autonomous Machine Vision
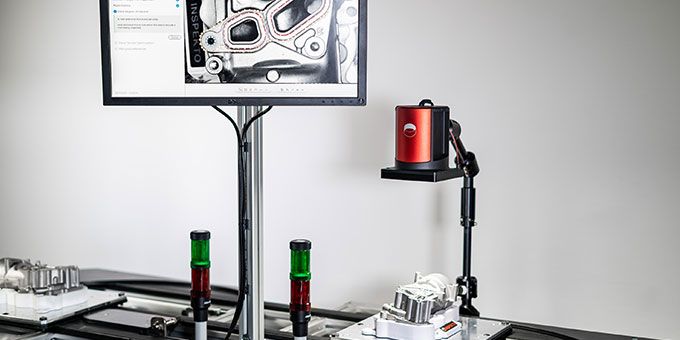
Yonatan Hyatt, CTO | Inspekto
For traditional machine vision solutions, inspecting shiny surfaces can be challenging due to reflections on the surface, which distort images and lead to inaccurate defect detection. Because this issue is common in plastics, it often prevents plastics manufacturers from using automated quality assurance (QA) methods. Here Yonatan Hyatt, CTO at Inspekto, discusses how Autonomous Machine Vision systems can help.
Machine vision systems are the backbone of quality assurance and are commonly used to inspect the results of all plastics processing methods, including injection moulding, rotational moulding, extrusion, compression and more. These systems can identify products with manufacturing defects using cameras that analyse the product from different angles. The data is then processed by integrated software that detects faulty products, which are then removed either manually or automatically from the production line.
However, there are several shortcomings to the use of traditional machine vision systems to inspect plastics. One common issue is the inspection of highly reflective surfaces. Light reflections create a certain visual noise that is seen by the system’s cameras as a physical feature of the inspected part. The system might in turn classify these features as defects, generating false rejects. Similarly, reflections can also cause certain areas of the inspected product to appear hidden, thus preventing inspection. This means that for plastic packaging or other glossy items, the systems’ inability to cope with reflections can be a serious pain point.
On top of this, the fact that the same production line can create items of different colours and shapes is problematic for traditional machine vision solutions, only capable of inspecting one product at a time. This is especially common in plastic injection moulding, where the mould is often replaced to manufacture a variety of products.
To solve this issue, human workers need to perform quality assurance, alone or alongside machine vision systems, to meticulously inspect each product and reject the faulty ones. This process can be exhaustive and too repetitive for humans, leading to errors. Faulty products could be sent to companies and rejected further on, causing a disruption in the logistics chain and amplifying waste.
Autonomous Machine Vision
Autonomous Machine Vision (AMV) is a new approach to quality assurance, designed to be more than automatic, but autonomous, from determining the ideal number of samples the system needs to learn the characteristics of an item, to self-adjusting the camera and lighting settings to obtain the best image possible of the product to be inspected. The system’s algorithm autonomously optimises the camera and illumination settings to take the best possible image of the object to inspect, and then detects and locates the object without any input from the operator.
The only AMV system currently on the market, the INSPEKTO S70, has just been relaunched on the market with new and improved settings that allow it to take clear and informative images of even the shiniest objects, so that they can be reliably inspected. The S70 Gen.2 is equipped with 5000K LEDs that are controlled by pulse-width modulation and arranged in several distinct segments. This allows the system to autonomously control the direction of the illumination and take several images with varying light direction and intensities. The images are then fused to create a single reflection-less HDR image. This patent pending technology makes the system ideal for the inspection of highly reflective plastics. The innovative illumination system is designed to avoid the human eye from seeing any flickering or light variation, so workers nearby will not be disturbed by sudden light changes.
As AMV systems are flexible and applicable to a huge variety of use cases, they can also allow multiple products to be inspected at the same location on the production line, contrary to what traditional systems are capable of. This makes them ideal for applications where the same production line manufactures a variety of items, such as in plastic injection moulding.
Autonomous Machine Vision AI
At the core of Inspekto’s systems are three independent and synergetic AI-based engines driving a proprietary electro-optic system, a technology called Autonomous Machine Vision AI (AMV-AI). The first engine is in charge of adapting the operating parameters of the electro-optical system in real-time to take clear and highly informative images of the object to inspect even in changing environmental conditions. The second is the detection and alignment AI module, which allows the system to recognise the parts it sees in the live video stream from the camera and identify the best moment to acquire an image to perform the last task – inspection. Lastly, the inspection AI engine inspects the part by comparing it with the sample images memorised during set up, without involving any experts or AI-training in the process.
Due to the fact that the system is very cost-effective, manufacturers can choose to implement not just one, but several inspection systems along the production line to ensure a total quality assurance of plastic products and optimise production. This means that defects can be spotted early on, instead of just at the end of the line, so that defective products can be removed before further resources are wasted to complete them. Over time, this approach to quality allows a plant to significantly reduce production scrap as well as save on the amount of energy that would otherwise be spent on producing defective items.
Autonomous Machine Vision also allows production plants to reduce downtime. Installing a traditional machine vision system and its required software can take weeks and even months. AMV systems can be setup in only 45 minutes, needing an average of 20 to 30 OK (good) sample items and no NOK (defective) ones.
There is no need for programming, training, or creating rules and collecting defected parts to train the system on how these may look like. Moreover, AMV systems continue to improve over time by gathering an increasing amount of data on the products they inspect.
The ease of use and cost-effectiveness of using AMV for inspecting plastic products could become a driving force for manufacturers to implement state-of-the-art technologies to avoid wasting material and contribute to increasing sustainability in manufacturing.
The content & opinions in this article are the author’s and do not necessarily represent the views of RoboticsTomorrow
Comments (0)
This post does not have any comments. Be the first to leave a comment below.
Featured Product
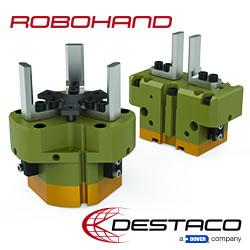