To better understand the benefits of cobot automation and how it works on the shop floor, we spoke to two leading providers of automated tools to small shops targeting two of the most time consuming and difficult to staff processes, quality control and welding.
Machine Shop Robots Get Real
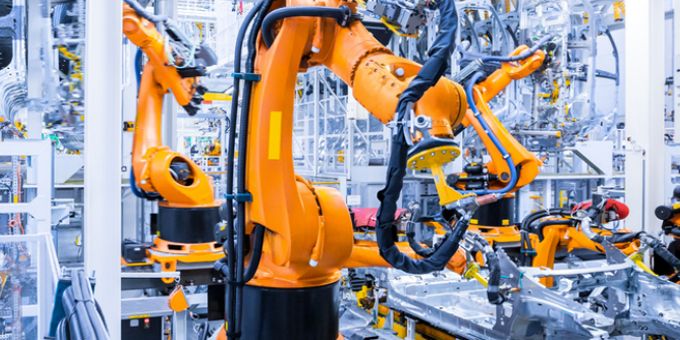
John Slater & Jorge Maceyras | FOCUS Investment Banking LLC
When we posed that somewhat naïve question to the CEO of an extreme high precision machine shop in 2014, we got the response we deserved. “Look up on the landing.” There we saw a hulking industrial robot our client had acquired years before to satisfy his auto industry customer that had a factory full of such behemoths. The unwieldy, difficult to program, creature had no role in the high mix low volume shop and had long been consigned to serve as the firm’s robot museum.
We quickly realized that a high precision shop such as our client’s was actually filled with robots, they just didn’t look like the industrial robotic arms we expected to see. A five axis mill with automated tool changers and pallet systems is an ever more sophisticated robot, but it can’t do everything. Parts must still be loaded, machines programmed and tweaked and materials and parts moved around the plant floor. In 2014 these tasks could be done by easily hirable shop floor employees. Those halcyon days are long gone. Today every owner is challenged daily with the increasingly frustrating task of recruiting qualified team members for the floor.
Fortunately, the world of robotics has made great strides, particularly with the advent of affordable cobots which can realistically support your machinists by taking on the dull dangerous and dirty jobs formerly the domain of entry level employees. As we noted previously, at IMTS 2022 automation was no longer an afterthought shoved to the back of the building, it was front and center and ubiquitous. Robotic automation is no longer the exclusive domain of giant manufacturers making thousands of identical parts—requiring “heavy” integration to install and configure new equipment. Now, with the “light” integration of cobots—short for collaborative robots—even small metalworking shops can (and increasingly must if they are to survive) automate at least part of the production of low-volume, high-mix orders.
At a relatively small cost in capital and quicker time-to-production —perhaps $100,000 and often producing within days or weeks of receipt —robotic automation creates huge dividends and a quick return on investment. With the shortage of skilled labor showing no signs of easing, automation can free up machinists to do more challenging and more profitable work—the kind of work they want to do—while the robots quietly load the parts. For the growing number of private equity acquirers focused on consolidating the machining and metalworking industry, shops which demonstrate smart use of automation attract more attention and higher valuations. A heavily automated, highly efficient shop is not only more likely to be more profitable, but also able to take on more new business, adding even more value to the enterprise. Not to mention the increase in quality, which also enhances margins.
To better understand the benefits of cobot automation and how it works on the shop floor, we spoke to two leading providers of automated tools to small shops targeting two of the most time consuming and difficult to staff processes, quality control and welding. Josh Pawley is founding partner and vice president of business development at Vectis Automation, a Loveland, Colorado-based company that provides cobots that automate the “dull, dirty and dangerous” aspects of the welding shop. Dave Henderson is CEO of New Scale Robotics in Victor, New York. Its Q-Span workstations automate the sorting and measurement of high-mix, small-batch manufactured parts, helping eliminate QC bottlenecks and improving utilization rates. Both companies use robots from Universal Robots, the number one cobot manufacturer in the world. Founded in 2005, the Danish company pioneered an automation revolution that has made robot technology accessible to small- and medium sized businesses.
Automated Quality Control
New Scale Robotics has pioneered a class of ultra-high precision micro robotic grippers to automate one of the most labor-intensive aspects of machining. “Many shops can't get the parts out because their quality control has gone from four days to six weeks. They just don't have the staff and it becomes a major bottleneck in the company,” Dave Henderson explains. “When that happens, the need to automate QC really becomes front and center. And for an industry like medical devices or aerospace components, quality control is absolutely critical.”
New Scale’s Q-Span workstation is a robotic arm that has grippers on the end that can pick up parts and then measure them using an automated dimensional gauging system. “Measurement is our main differentiator,” Henderson says. “We are twice as accurate as a digital caliper without the human variation. That's our starting point. We also do drop gauges, bore gauges, thread gauges, and other kinds of measurements. We can do other configurable tools with Q-Span.”
For example, one of New Scale’s customers makes drill bits for orthopedic procedures, such as installing artificial joints. Each one has very specific diameters. The client wanted a system that can measure 30 different parts that are similar but have unique differences.
“We developed a system that mimics what their human operators are doing,” Henderson explains. “The human operator puts the parts in a vertical tray that has the parts sticking up in a very precise array. The robot then sequences through the array in a very specific manner. The part is picked up out of the tray, brought to a measuring system and the part is evaluated for pass or fail criteria.” The information is then fed back into the machine tool to make any necessary adjustments.
Even more impressive, New Scale is working with another client to create a program that can sort through and measure 15 different parts, each with unknown dimensions.
“You put the parts in a bin, which are then picked out by a robot using machine vision,” he explains. “Then the parts are measured and sorted according to a range of values. There are different bins for different sizes and use standard commercial trays to hold these parts. The operator can then take the parts, put them in a rack, and they are ready for the manufacturing process.”
New Scale is targeting machine shops that are struggling with staffing to get people to run their machines. “We are addressing the labor shortage by helping them to retain and motivate a younger workforce,” Henderson says. “Now one machine operator can run five machines instead of two.”
Henderson also notes that cobots are “inherently safe. They don't require safety protection like shields or lasers or other kinds of sensors. That really simplifies the challenges of bringing in a new tool in an existing facility. You don't have to completely reorganize your facility to use our tool. Industrial robots are usually in cages because they could injure someone, but a cobot sits right next to the machine operator.”
Automated Welding
Vectis addresses the same core problem, lack of a trained workforce throughout the metalworking industry. “We saw a need for lower cost, easier to use, less risky, and more flexible automation to allow small- and medium-size enterprises to leverage automation just as the big guys have for decades,” according to Josh Pawley. “That allows for lower volumes to be automated, and for people of all types and backgrounds to program and teach the robot what to do.”
That’s particularly important at a time when there is such an acute shortage of trained machinists, welders and other workers skilled to run the machines that make the parts that American manufacturers need. “The shortage of welders and skilled fabricators is the biggest driver of our business,” says Pawley. “It's largely the nature of welding—it's dull, dirty and dangerous in many cases. There are not a lot of folks going into the space, and the average age of a welder is in the late 50s. But the most dull and dirty jobs can be supplemented with automation.”
Indeed, job shops are some of the biggest winners from flexible and cobot automation, he says. “The ability to changeover quickly from job to job and project to project is going to be more and more important. Everybody needs to get better at rapidly responding and pivoting. The ability to changeover quickly and retool and reprogram is going to be necessary for manufacturers moving forward. This spurs the need for more automation.”
While years ago there may have been some resistance, if not hostility, from welders concerned that robots were going to take away their jobs, that’s generally not the case anymore, Pawley told us. “Welders like to do stuff that's challenging. They don't want mind-numbing, boring work,” he says. “That is the best work for automation. Cobot automation is a tool to offload all that boring stuff, and welders usually connect with that very well.”
It's also a talent attraction and retention tool, he adds. “It makes welding more interesting. Someone who is young, eager, and not put off by technology, who has been in front of computer screens their whole life, they will be your ‘cobot champion.’”
While automation can’t do all the tasks in a machine shop—at least not yet—it can reduce the amount of work that must be done by a human. For example, grinding “has to be one of the worst jobs in the fabrication shop,” Pawley says. While Vectis has yet to automate the grinding process, which Pawley describes as a “visual and cosmetic thing” that in most cases requires a human to do it, automated welding often eliminates, or at least lessens, the need for grinding later on in the process.
“By making better welds in the weld shop, you reduce the need for grinding in the grind shop,” he says. “You take out the grinding, which is mostly dirty and expensive, that's a huge win. Most of our customers are seeing two to four times productivity increases in the weld shop from per-part labor savings – not to mention those additional wins of higher quality, less grinding, talent attraction, and more control over cycle times.”
“Crawl, walk, run”
Both Pawley and Henderson agree that small machine shops interested in automating their processes should start small, automating only those parts of their processes that most lend themselves to being done by a robot, which usually are those tasks that human workers don’t want to do and can be done more cost effectively by a robot.
“Don't focus on automating the biggest and most complex welding jobs in the shop,” Pawley advises. “Start with the simple stuff. Crawl, walk, run. That's the key to psychological success as well. If you try to run first, you may fall on your face. You start to not feel comfortable with leveraging the technology. Instead, get the quick win and go from there. I see a lot of folks trying to run, walk, crawl. They think, ‘If I’m going to spend the money on automation, why not go big?’ Our automation allows manufacturers to take that crawl step. We can run and walk with them, too, but let's take that crawl step first.”
Automating aspects of the manufacturing process can also be economical.
“Incremental automation is very important, the ability to break it down into step-by-step pieces,” Henderson says. “We consistently get requests from people who were thinking of heavy integration, but they haven't had any automation before, and they wanted a turnkey system which cost $1 million and take a year to implement. But traditional automation for some fabricators is too much to jump into to begin with. We can get them up and running in three months for $100,000. By doing that you empower your staff to operate machines, as opposed to having turnkey systems that are dependent on the system integrator. So you get the best out of both automation and your people.”
At the very least, “if you are not automated yet, it's time to start looking,” Pawley says. “Start the conversation soon. The labor shortage isn't getting any better.”
The content & opinions in this article are the author’s and do not necessarily represent the views of RoboticsTomorrow
Comments (0)
This post does not have any comments. Be the first to leave a comment below.
Featured Product
