As Everest Labs was developing their system to be sold to recycling centers worldwide, they found that their robot needed speed feedback in order to track the recyclables on the conveyor, and therefore needed a simple way to install conveyor speed feedback on a gear motor.
SCARA Robot Sorts Recyclables Using a Simple Conveyor Speed Feedback System
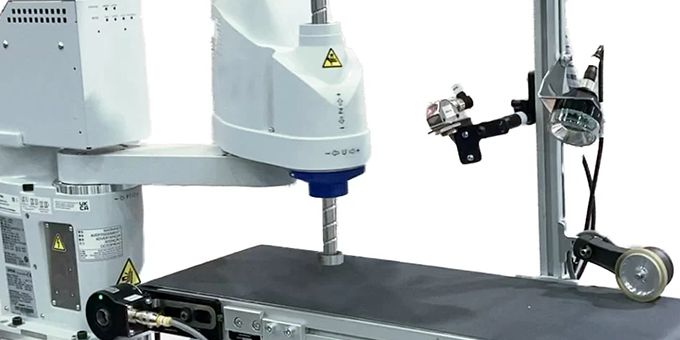
Case Study from | Encoder
Everest Labs in Fremont, California, is an innovative company building AI-enabled operating systems. Using a SCARA robot with pick-and-place operation, their system sorts materials passing by it on a conveyor, using an AI to distinguish materials and identify recyclables.
As Everest Labs was developing their system to be sold to recycling centers worldwide, they found that their robot needed speed feedback in order to track the recyclables on the conveyor, and therefore needed a simple way to install conveyor speed feedback on a gear motor.
SUMMARY OF ENCODER REQUIREMENTS FOR THIS APPLICATION:
- 58 mm hollow-bore encoder
- 3/8 inch shaft
- Tether arm
- Resolution of 1024 CPR
- Line Driver Output
- 8-pin M12 connector
- IP67 sealing
The Problem
Everest Labs are developing their system to be sold to recycling centers worldwide, which will make recovering recyclables from refuse more efficient.
In their system, the robot requires speed feedback from the conveyor. But the construction required an innovative mount. Everlast Labs had seen an EPC encoder on a gear motor, and wanted suggestions on how to affix the encoder but keep it protected from other equipment.
With varying motors used from one customer to the next, they were looking for a solution that could be flexible and allow quick and easy installation. The gear motors typically have a back shaft opposite the drive end that is exposed, but somewhat flush to the gearbox case. There is not enough shaft to install an encoder. Drilling and tapping the shaft and installing a stub shaft was an option, but time consuming and could void warranty of the gear motor.
Samir Kamat, an engineer with Everest Labs, called EPC and reviewed possible solutions. Ryan Money, an engineer with Kaman Automation (a distributor of EPC products) was available and in the area, so Ryan visited Everest Labs to review the installation challenge and see how it could be solved.
The Solution
After some consideration, a solution was found: EPC's Model 58HF could be mounted with a magnetic coupling and an EPC Uni-cover, along with a customer-supplied adaptor plate for securing the encoder.
Everest Labs chose the Model 58HF because of its compact size, metal housing, and IP67 seal – which protects the encoder in applications where water is present. The magnetic coupling was selected because it allows fast, easy installation on almost any motor shaft likely to be encountered on-site. The Uni-cover was selected for safety for operators working around the equipment, and to protect the encoder from debris and impact hazard from fork lifts or other equipment.
After the Model 58HF was installed with the magnetic coupling, Uni-cover, and customer-supplied adaptor plate, and testing was completed, Samir and Ryan reported that the machinery was working consistently and reliably.
MODEL 58HF WITH TETHER ARM
The Model 58HF Accu-Coder® hollow-bore encoder is specifically designed for the challenges of an industrial environment. The versatile Model 58HF offers 6 output types, 32 different waveforms, and any resolution from 1 to 65,536 CPR (that’s 262,144 counts in full quadrature). This encoder is also highly mechanically configurable.
MODEL 58HF KEY FEATURES:
- 58 mm package available in thru-bore or blind hollow bore
- Resolutions from 1 to 65,536 CPR
- 6 different output types to choose from
- 32 different waveforms available
- Standard and metric bore sizes up to 5/8” and 15 mm
- Several flexible mounting options available
- IP67 sealing available
The content & opinions in this article are the author’s and do not necessarily represent the views of RoboticsTomorrow
Comments (0)
This post does not have any comments. Be the first to leave a comment below.
Featured Product
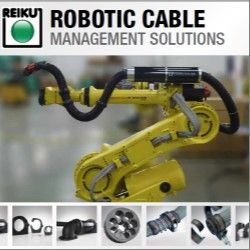