The new algorithm and technology have the potential to drastically reduce complex fiber alignment and photonics alignment procedure times by several orders of magnitude, surpassing any other existing technique used for automated fiber optic alignment in the market.
Fiber Alignment and Photonic Chip Test & Assembly Just Got Easier
Article from | PI
Video: PILightning first-light detection technology explained
We went to first principles and thought about search in the macroscopic world. Which when viewed in certain lights is wildly different than the existing photonics signal search paradigm in concept. We conceived of a new search method based on an in-depth understanding of active piezo ceramics – effectively building a bridge from the macro world and into microscopic search.
Lightning-fast first light capture is now available with this new technology.
We ran this new technology through real photonics signal data simulation to quantitatively characterize alignment times referenced against current state-of-the-art methods. And the results were dramatic: the simulations under one scenario of typical alignment conditions resulted in multiple orders of magnitude improvement in first signal finding. We also carried out multiple tests, first with high-speed piezo mechanisms in free space laser coupling and close fiber to photonic element coupling with outstanding results.
Later, we adapted the lessons learned in the piezo world to larger, multi-axis air-bearing motion systems in single- and dual-sided alignment applications.
The outcomes exceeded our expectations and have the potential to revolutionize the industry.
In some cases, we captured data that would perform the signal finding at such high speed it was surpassing human reaction times. The alignments were done lightning-fast, and that’s why we call this new technology PILightning.
The PILightning model is a quantum leap forward. It promises to improve alignment time by orders of magnitude – orders of magnitude faster alignment! It's outpacing any other technique currently used for automated photonics alignment in the market. We look forward to its implementation in Silicon Photonics Test & Assembly solutions.
The content & opinions in this article are the author’s and do not necessarily represent the views of RoboticsTomorrow
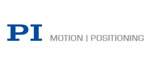
PI USA (Physik Instrumente)
PI is a privately held company that designs and manufactures world-class precision motion and automation systems including air bearings, hexapods and piezo drives at locations in North America, Europe, and Asia. The company was founded 5 decades ago and today employs more than 1300 people worldwide. PI's customers are leaders in high-tech industries and research institutes in fields such as photonics, life-sciences, semiconductors and aerospace.
Other Articles
Nanopositioning and Motion Control Solutions for the Semiconductor Industry
Elevating Precision Motion and Control with Magnetic Levitation to New Heights
Comparing XY-Theta Motion / Positioning Stage Options for Precision Automation Applications
More about PI USA (Physik Instrumente)
Comments (0)
This post does not have any comments. Be the first to leave a comment below.
Featured Product
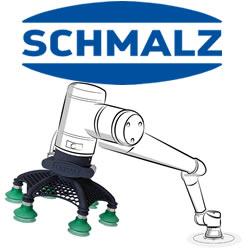