Acura Provides All Access Look into the Performance Manufacturing Center (PMC)
In a new video released today, Acura offers a comprehensive, behind-the-scenes look into its Performance Manufacturing Center (PMC) in Marysville, Ohio, the home of the NSX.
"Inside PMC" is the latest in a series of videos on the innovations and performance capabilities of the NSX, which began with the release of "NSX, 30 Years of Performance" at this year's Chicago Auto Show, where Acura marked 30 years since the debut of the iconic supercar, followed most recently by "Face-off: Acura NSX vs NSX GT3 Evo," highlighting the similarities between the production NSX and race-bred NSX GT3 Evo.
From its inception, the PMC was designed to innovate both the means and the methods of producing low-volume specialty vehicles by marrying the precision of advanced technology with the artistry of human craftsmanship1. "Inside PMC" presents some of the Performance Manufacturing Center's most advanced and ingenious approaches to making a supercar, including its unique body construction method, world-class painting system, meticulous vehicle assembly process and total quality validation process, as well as the exclusive NSX Insider Experience for owners.
Precision Crafted Performance the PMC Way
Numerous qualities distinguish the PMC:
- Ultimate Body Accuracy: PMC is the first plant in the world to utilize 100-percent robotic MIG welding for body construction, using eight robots to apply 860 MIG welds to the aluminum-intensive space frame with ultimate precision, to produce a highly accurate body with tolerances measurable down to the width of a human hair.
- Inventive Technologies: PMC associates are responsible for the development of seven patented and four patent-pending technologies, a number of which were inspired by racing, including a novel 45-minutes process for exacting wheel alignment, a 4-corner weight and ride height check, and a dynamic 4-wheel braking performance measure.
- In-house Validation: To ensure the pristine condition of NSX, each vehicle is performance-validated through a sophisticated series of measures within the walls of PMC, and its engine is bench tested to the equivalent of 150 break-in miles at the company's Anna, Ohio, engine facility, such that every NSX is track-ready without ever having been driven on the street.
- Ultimate Configurability: just like a race shop where items are moved around by hand, PMC has no conveyor belts or other automated parts delivery systems. This allows for maximum flexibility within the plant to accommodate different types of vehicles and new approaches to achieving ultimate quality for the customer.
- Incredible Paint Quality: Andaro Paint is Acura's most lustrous paint and among the highest quality finishes on any vehicle anywhere. Painting an NSX takes five days and creates a finish up to 17 millimeters thick, 3-times more than an average production car.
- Quality You Can Track: Nearly every one of the NSX's bolts is fastened initially by hand to avoid cross threading, and then torqued to exacting tolerances using wirelessly connected wrenches that validate and record every fastener's setting in perpetuity, as a part of the specific vehicle's build data.
- Handmade Performance: Each NSX engine is hand assembled by a single master builder, within a bespoke production facility at the company's nearby Anna, Ohio, engine plant. The Anna plant also manufactures the NSX's six aluminum frame nodes, which utilize the world's first ablation casting method to deliver both rigidity for performance and ductility for crash energy absorption.
- Race Car Repair: The PMC produces the space frame for the NSX GT3 Evo race car. While nobody likes a crash, in racing, it's bound to happen. In such cases the PMC repairs and rebuilds customer GT3 race cars, sometimes in as little as 2-3 days, to ensure Acura Motorsports customers are ready to go when the green flag drops.
- Sharing the Dream: It was always Acura's dream to share the passion and craftsmanship of the PMC team with more Acura customers. That dream came true with the July 2019 launch of the 2020 TLX PMC Edition, painstakingly finished, hand assembled and quality checked by the same master technicians that build the Acura NSX supercar. Only 360 lucky customers will get their hands on one.
About Acura
Acura delivers Precision Crafted Performance – a commitment to evocative styling, high performance and innovative engineering, all built on a foundation of exceptional quality and reliability. The Acura lineup features six distinctive models – the RLX premium luxury sedan, the TLX performance luxury sedan, the ILX sport sedan, the five-passenger RDX luxury crossover SUV, the seven-passenger Acura MDX, America's all-time best-selling three-row luxury SUV, and the next-generation, electrified NSX supercar.
Five of the six Acura models sold in North America are made in central Ohio, using domestic and globally-sourced parts, including the ILX and TLX luxury sports sedans (Marysville Auto Plant), the RDX and MDX luxury SUVs (East Liberty Auto Plant) and the Acura NSX supercar, which is built to order at the Performance Manufacturing Center in Marysville, Ohio.
Additional media information including pricing, features & specifications and high-resolution photography is available at AcuraNews.com. Consumer information is available at Acura.com. Follow Acura on social media at Acura.us/SocialChannels.
1 Acura vehicles built in the PMC use domestic and globally sourced parts
Comments (0)
This post does not have any comments. Be the first to leave a comment below.
Featured Product
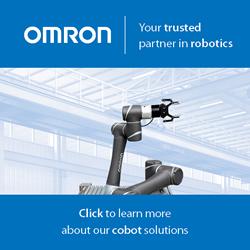