Robotics In Manufacturing: Threat or Opportunity?
The use of robotics in manufacturing has grown consistently over the past decade. A recent report from the Association for Advancing Automation revealed that North America saw a record in robot sales in 2022, with the number of robots ordered up 11% from the previous year.
Robots can perform repetitive or dangerous tasks such as material handling or assembly faster than humans and with optimal accuracy, thereby increasing safety and productivity on the manufacturing floor.
For this reason, many fear that robots could displace human workers and disrupt the labor market. However, the impact of robotics on human employment hasn’t always been clear. In fact, some studies have concluded that robots aren’t actually replacing human workers, but rather complementing their labor.
Here’s the truth about robots in the manufacturing industry.
Robots increase productivity
Robots can work around the clock at a consistent pace. They’re generally faster and more precise than humans in repetitive tasks, and they produce higher-quality products in less time.
Given that robots rarely make mistakes, they greatly reduce the need for rework and minimize scrap on a manufacturing floor.
In 2021, Nestlé reported a 53% increase in productivity after incorporating pallet-loading robots in its chocolate manufacturing plants in Brazil.
Additionally, Forbes states that Amazon has increased its productivity by up to 300% thanks to its warehouse robots.
But productivity isn’t always about carrying out a task more promptly and efficiently. It can also encompass performing multiple tasks — something that modern robots are excellent at doing.
For example, the UR16 collaborative robot from Universal Robots can take care of machine tending, material handling and removal, screw and nut driving, and packaging, and it’s programmed to switch between tasks in one continuous operation. This model was acquired by the Ford Motor Company, specifically for one of its Romanian plants, where it’s used to optimize the plant’s assembly lines.
Robots increase plant safety
Productivity is closely related to safety. In the U.S. alone, workdays lost due to occupational injuries totaled 65,000,000 in 2020. But given that robots can take over dangerous tasks on the manufacturing floor, they can also improve productivity by keeping human workers safe and active.
A 2022 study by the University of Pittsburgh, the University of Toronto, and the Free University of Berlin revealed that industrial robots were able to reduce work-related injuries by 1.2 cases per 100 workers in a one-year period.
Robots can be used for welding operations, which can cause electric shocks, burns, eye damage, and manganese poisoning. American construction equipment manufacturer Caterpillar, which relies on collaborative welding robots to do this activity, has claimed that welding robots have made their overall manufacturing process more efficient and safe.
The second leading nonfatal occupational injury is overexertion, according to a 2020 report by the U.S National Safety Council. Overexertion occurs when workers push their bodies beyond their physical limits. In manufacturing, repetitive work and heavy lifting are often the cause of overexertion. Robots can do this type of work 24/7 without consequences.
Many robots are used for heavy lifting purposes, especially in the automotive industry. There are also item-moving robots, such as Amazon’s Sparrow. The use of robots in general has cut down total walking distances by 75% to 80% at Amazon’s warehouses, reducing their workers’ muscle fatigue.
Additionally, robots can work in contaminated environments and handle harmful substances, something that can seriously affect a human worker’s health — but is an essential part of work in certain industries.
If equipped with adequate sensors, robots can also monitor their environment to identify potential hazards and send alerts to human workers. For example, if a robot working on a machine detects a dangerous temperature increase, it may send an alert to maintenance teams or shut the machine down to avoid an accident.
Robotic technology increases efficiency
Efficiency is about making the most out of the same resources, and robots can increase efficiency in the manufacturing plant in several ways:
-
They can accelerate and optimize manufacturing processes in ways that help manufacturers save on energy costs. If integrated with IoT devices and sensors, they can monitor and improve real-time energy consumption. They can also work in poor lighting conditions and extreme temperatures, reducing the need for climate control systems in manufacturing plants.
-
They can make maintenance more efficient. When integrated with CMMS software, robots can receive repair orders and automate scheduled maintenance tasks, which minimizes machine downtime. They can perform a variety of maintenance tasks, such as cleaning, lubricating, or replacing a machine’s components. They can also be equipped with sensors that detect equipment malfunctions or failures before they happen.
-
They can help reduce waste in the manufacturing plant — having fewer defective products discarded in each production run means that robots enable a more efficient production process. At the end of the day, manufacturers can produce higher-quality products with minimal rework, scrap, and recalls thanks to the robots’ precision.
Conclusion
Robots are becoming increasingly popular in the manufacturing industry because their benefits outweigh the threats.
As mentioned above, robots aren’t likely to replace as many human workers as people think they will. Instead, they provide the opportunity to get rid of repetitive or dangerous tasks, allowing workers to focus on more creative and fulfilling tasks — tasks that require critical thinking, decision-making, and problem-solving skills.
Human workers can always be reallocated or have their tasks reassigned, as human intervention is still required in several areas of manufacturing.
Robots can work alongside humans, as is the case of collaborative robots.
At the same time, robots can create new job opportunities, such as high-paying specialized roles in robot design, programming, maintenance, and supervision.
ERIC WHITLEY
For over 30 years, Eric Whitley has been a noteworthy leader in the Manufacturing space. In addition to the many publications and articles Eric has written on various manufacturing topics, you may know him from his efforts leading the Total Productive Maintenance effort at Autoliv ASP or from his involvement in the Management Certification programs at The Ohio State University, where he served as an adjunct faculty member.
After an extensive career as a reliability and business improvement consultant, Eric joined L2L, where he currently serves as the Director of Smart Manufacturing. His role in this position is to help clients learn and implement L2L’s pragmatic and simple approach to corporate digital transformation.
Eric lives with his wife of 35 years in Northern Utah. When Eric is not working, he can usually be found on the water with a fishing rod in his hands.Comments (0)
This post does not have any comments. Be the first to leave a comment below.
Featured Product
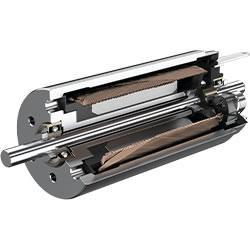