World's Smallest Micro Actuator with Feedback
2022 Trends from Robots.Jobs Shows Dramatic Growth in Robotics and Artificial Intelligence Career Opportunities
IP68 Enclosures Series Ensures Total Protection Against Dust and Continuous Submersion
With the piSOFTGRIP® 100-4, Piab is launching the largest gripper of this series
MHS wins award for robotics designed to address e-commerce demands in parcel logistics warehouses
Robot Sales in North America Have Strongest Year Ever In 2021
Private 5G Connectivity and AI Technologies Accelerate the Transformation From Automation to Autonomy
Epson Signs Heitek Automation as Distributor in the Western Region
Direct Teach, Plug and Play (DTP) Collaborative Robots Enhance Yaskawa's HC-Series Line
The Next Generation of Robots
PTC and Schaeffler announce new strategic alliance to accelerate digital transformation roadmap
Universal Robots Reports Record Annual Revenue of over $300M
Exceptionally high speed and dynamics
MiR Autonomous Mobile Robot Sales Up 42% in 2021
OnLogic Partners with ISMOsys to Expand Reach of Industrial, IoT and Edge Computing Solutions
Records 1411 to 1425 of 11341
First | Previous | Next | Last
Industrial Robotics - Featured Product
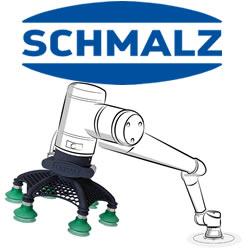