The fourth industrial revolution: more of an evolution?
The Internet of Things has been hailed as the fourth industrial revolution, but can it warrant this title at its current pace of development?
The potential of Industry 4.0 remains an important talking point for members of the international coil winding, transformer and electrical manufacturing communities. And its hardly surprising. Following revolutions in steam power, electricity and digital technology, the Internet of Things (IoT) is tipped to completely transform the way factories operate.
Much of the buzz can be traced back to when Professor Detlef Zühlke, director of Innovative Factory Systems at the German Research Center for Artificial Intelligence in Kaiserslautern, Germany, presented his SmartFactoryKL concept at CWIEME Berlin in 2015.
However, widespread take-up has yet to materialize. At CWIEME Berlin 2017, Alex West, principal analyst for smart manufacturing and industrial communications at IHS Markit Technology, said that Industry 4.0 still offers "no clear return on investment" for manufacturing operations and is seen by some as a "solution looking for a problem."
Nevertheless, investment in Industry 4.0 technology is on the rise. By the first quarter of 2017, the industrial automation equipment market had already increased by 1% on 2016 figures. Wests colleague Andrew Orbinson, a senior analyst in industrial automation at IHS, predicts investments to pick up throughout 2017 and peak in 2018, especially in the US. According to Orbinson, increasing capital spending, reduced tax rates and a strengthening US dollar will help to drive investment, spelling good news for manufacturers of electric motors for industrial automation applications.
Keeping production lines running
IHS believes improvements in uptime and efficiency are some of the main reasons for the increased investment. In his CWIEME Berlin seminar, West highlighted that downtime in an automotive plant can cost 20-30,000 USD per minute. With this in mind, asset health - including condition monitoring and predictive maintenance - is a major focus area for manufacturers. West pointed to a growing market for electric motor sensors that monitor temperature and vibration and could suggest impending failure.
"This intelligence is not feeding into maintenance, however - its still reactive," he said. "Devices are connected and collecting data but the next step is to do something with that data - to have advanced analytics, use of the cloud and open applications, and standards around that."
Meeting new customer demands
IHS also made reference to the fact that customers are increasingly demanding more customization and shorter lead times. CWIEME Berlin exhibitor Voestalpine echoed this trend at the event in June. The Austrian steel producer revealed that half of the pole sheets it sells today are customized. The Voestalpine Group likewise prides itself on its predominantly European and high-tech manufacturing.
"Automation allows companies to bring production closer to the customer because a robot is cheaper than a real person," West said.
Andrew Orbinson also reported that between 2001 and 2013, the US lost 3.2 million jobs to China - especially in computer and electronic parts manufacturing and motor vehicles and motor vehicles parts manufacturing - but increasing automation and smart technologies are supporting a trend for reshoring. "Lower skilled jobs are becoming redundant as robotics can be used, creating higher skilled jobs. Were seeing labour shortages emerging because these jobs didnt exist before. New skillsets are required to work in the factory of the future," he said.
New business models required
A significant issue for manufacturers looking to implement Industry 4.0 principles, however, is that no single supplier has all the expertise. In his CWIEME Berlin seminar, West described a clash between operational technology and information technology with no clear view as to who would own the project. He suggested that widespread implementation would require new vendors with new business models.
"There needs to be a shift from selling hardware and software to services - or rather selling uptime. Customers could pay a service contract for ‘power by the hour," he said.
Misconceptions about cybersecurity
Another major issue slowing the development of Industry 4.0 is concerns about cybersecurity. West spoke of a "misunderstanding of the perceived problems". "You could put your money under your bed or in the bank - experts in providing security and access to assets. The cloud makes sense," he said.
IHS carried out a survey among 915 companies on the reasons for investing in Industry 4.0 and while improving cybersecurity came bottom of the list, Obinson expects it to move up in a few years time.
"Its going to take some time for widespread take-up," he said. "Cybersecurity is a key challenge, but its a speed bump more than a complete roadblock. The technology needs to evolve along with applications, business models, and ways of operating. Industry 4.0 is an evolution, not a revolution."
The discussion continues
Industry 4.0 will once more be an important topic for discussion at the next exhibition in the CWIEME series, CWIEME Istanbul, which takes place 2nd-4th November at the Istanbul Expo Center. Under the theme ‘new pathways to optimisation and efficiency, the CWIEME Istanbul seminar programme will explore the many areas of electrical industries on the brink of disruption at a time when demand for more efficient, intelligent and powerful electric machines is reaching new heights. Among the speakers, Alex West will return to discuss the growing impact of the Industry 4.0 movement on manufacturing.
Featured Product
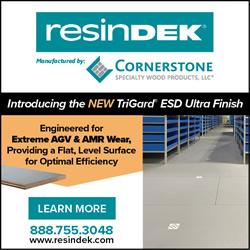
ResinDek® TRIGARD® ESD ULTRA FOR HIGH-TRAFFIC ROBOTIC APPLICATIONS
To maximize the productivity of an autonomous mobile robot (AMR) or automatic guided vehicle (AGV) deployment, it's critical to create the optimal environment that allows the vehicles to perform at their peak. For that reason, Cornerstone Specialty Wood Products, LLC® (www.resindek.com) created the TriGard® ESD Ultra finish for its ResinDek® engineered flooring panels. The TriGard ESD Ultra finish is ideal for high-traffic robotic applications characterized by highly repetitive movement patterns and defined travel paths.