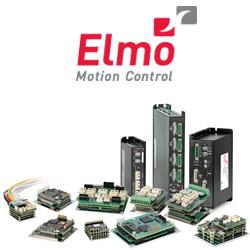
Elmo Motion Control - The Platinum Line, a new era in servo control
Significantly enhanced servo performance, higher EtherCAT networking precision, richer servo operation capabilities, more feedback options, and certified smart Functional Safety. Elmo's industry-leading Platinum line of servo drives provides faster and more enhanced servo performance with wider bandwidth, higher resolutions, and advanced control for better results. Platinum drives offer precise EtherCAT networking, faster cycling, high synchronization, negligible jitters, and near-zero latency. They are fully synchronized to the servo loops and feature-rich feedback support, up to three feedbacks simultaneously (with two absolute encoders working simultaneously). The Platinum Line includes one of the world's smallest Functional Safety, and FSoE-certified servo drives with unique SIL capabilities.
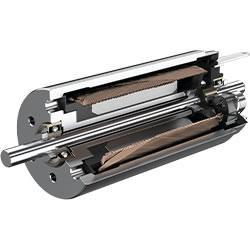
New incremental encoder IERF3 L from FAULHABER
FAULHABER is expanding its product range with the ultra-precise incremental encoder IERF3 L. Thanks to the optical measuring principle and state-of-the-art chip technology, the device offers the highest resolution, excellent repeatability, and outstanding signal quality. In typical applications, the positioning accuracy is 0.1° and the repeatability 0.007°. This makes the encoder the perfect solution for high-precision positioning applications in confined spaces.
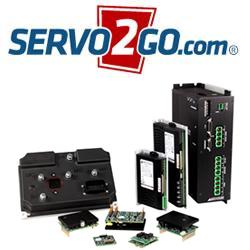
High Performance Servo Drives for localized and distributed control applications from Servo2Go.com
Engineered to drive brushless and brush servomotors in torque, velocity or position mode, Servo2Go.com offers a broad selection of servo drives in a wide range of input voltages and output power levels.
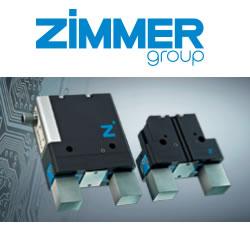
Zimmer Group - THE PREMIUM GRIPPER NOW WITH IO-LINK
IO-Link is the first standardized IO technology worldwide for communication from the control system to the lowest level of automation.
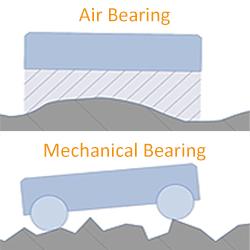
PI USA - Gantry Stages for Laser Machining and Additive Manufacturing
High performance gantry systems, from PI, are used in precision assembly, laser machining, and additive manufacturing. Complete with software and state-of-the-art EtherCat® motion controllers. Easy to program, easy synchronization with lasers and dispensers. Standard and custom, compact systems and large, granite-based units.
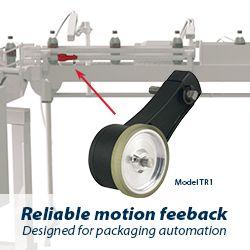
Model TR1 Tru-Trac
The Model TR1 Tru-Trac® linear measurement solution is a versatile option for tracking velocity, position, or distance over a wide variety of surfaces. An integrated encoder, measuring wheel, and spring-loaded torsion arm in one, compact unit, the Model TR1 is easy to install. The spring-loaded torsion arm offers adjustable torsion load, allowing the Model TR1 to be mounted in almost any orientation - even upside-down. The threaded shaft on the pivot axis is field reversible, providing mounting access from either side. With operating speeds up to 3000 feet per minute, a wide variety of configuration options - including multiple wheel material options - and a housing made from a durable, conductive composite material that minimizes static buildup, the Model TR1 Tru-Trac® is the ideal solution for countless applications.
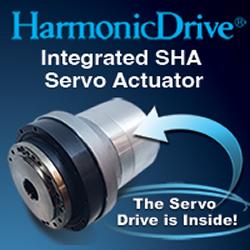
Harmonic Drive - Coming Soon! Integrated Actuators with EtherCAT®!
The IDT Series is a family of compact actuators with an integrated servo drive with CANopen® and, coming soon, EtherCAT® . With high torque, exceptional accuracy and repeatability, these actuators eliminate the need for an external drive and greatly simplify cabling.
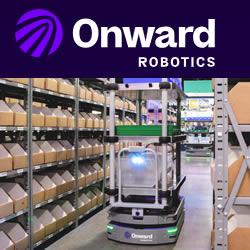
Onward Robotics - Meet Me® Fulfillment Automation
Meet Me uniquely brings talent and technology together: providing end-to-end process efficiency and enabling accurate and continuous fulfillment workflows. Proprietary Pyxis technology uniquely orchestrates picker and Lumabot AMR workflows independently, delivering fast, accurate, and efficient fulfillment from induction to pack out. Learn more about Meet Me Automation: Download Overview Brochure
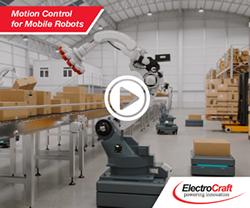
ElectroCraft's Motion Control for Mobile Robots
ElectroCraft is showcasing its award-winning mobile robot technology including their powerful and compact wheel drives, high-torque-density brushless DC motors, precision linear actuators as well as servo motor drive technology at a variety of conferences and tradeshows including the Boston Robotics Summit. Robotics Summit is the premier symposium for the sharing of ideas, technology, and market developments for robotic technologies across industries. Beyond a showcase and pitch of product, ElectroCraft is eager to participate in the collaborative discussion of challenges and opportunities that will shape the near and long-term robotic marketplace.
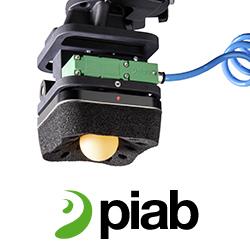
The piCOBOT Electric vacuum generator
Fully electric, slim design and absence of air-tubing and cabling. The new piCOBOT® Electric heads towards another success for Piab's piCOBOT® program. A secondary effect of these achievements is the absence of entangling air tubing and cabling. It simplifies the installation, and as the new piCOBOT® Electric only needs a single connection on the cobot arm, the clean set-up allows a completely unrestricted movement. The new piCOBOT® Electric package will contain plug & play software to fit UR e-series cobots, but many other useful adaptations will be introduced in the coming year
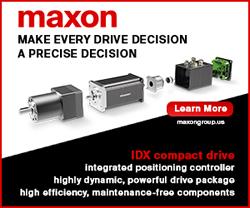
Strain Wave Gearheads by maxon - Highly precise, compact, and efficient.
Strain wave gearheads are ideal for use in applications requiring precision motion control and high torque transmission in a compact design. maxon strain wave gearheads are a specialized type of gearhead where precision and compact design are crucial. This type of gearhead is often used in applications in a confined space. With their advanced gear tooth design, maxon's strain wave gearheads provide high efficiency and good back drivability. Typical applications include: Robotics, Aerospace, Medical technology and Optical systems .
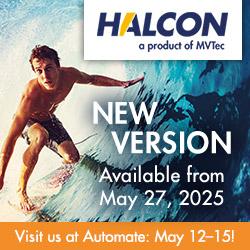
Next-Level Vision with HALCON 25.05
HALCON 25.05 sets new standards for machine vision, introducing Deep 3D Matching for robust bin picking, enhanced OCR accuracy, improved QR code reading on curved surfaces, and smarter camera integration. Meet MVTec at Automate Detroit and experience how the latest deep learning technologies and development tools empower you to create faster, more reliable, and flexible industrial solutions.
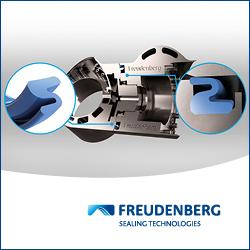
IP Seals for Robots
Freudenberg Sealing Technologies' IPRS (Ingress Protection Seals for Robots) provides reliable protection for robotic systems operating in harsh environments. Designed to prevent dust, moisture, chemicals, and wear from compromising performance, IPRS extends service life and reduces maintenance. The adaptive Z-shaped geometry ensures sealing integrity under continuous motion, making it ideal for high-speed automation and outdoor applications. Manufactured with high-performance elastomers such as Fluoroprene XP and EPDM, IPRS offers exceptional resistance to lubricants, cleaning agents, and extreme temperatures. This makes it the perfect solution for six-axis robots, SCARA robots, AMRs, AGVs, and cobots. With its low-friction design and durable materials, IPRS enhances energy efficiency and operational reliability in industrial and autonomous robotics. Learn more about our IPRS Seals
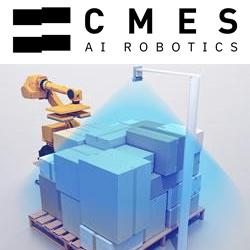
CMES - AI-Powered 3D Robot Vision
Powered by AI, CMES Robotics enables 3D vision for factory robots. CMES AI vision software enables robots to recognize unstructured, flexible, or deformed objects, pick them up, and loading and unloading. CMES Vision software has been deployed worldwide for random palletization and depalletization along with void filling applications. CMES Robotics automates your warehouse, logistics, and supply chain. For more information, please visit: cmesrobotics.com or email info@cmesrobotics.com.
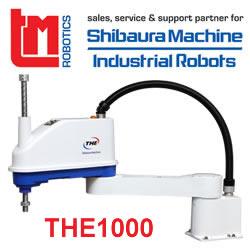
TM Robotics - Shibaura Machine THE SCARA range
The THE range from Shibaura Machine is an extensive line up of SCARA robots. Available in four arm lengths THE400 (400mm), THE600 (600mm) and the most recent THE800 (800mm) and THE1000 (1000mm), this range is suitable for assembly, handling, inspection and pick and place processes in varied industrial applications. The THE1000 boasts a 20kg payload capacity and an impressive 0.44 second cycle time, providing high speeds for processes with large components. In fact, the range has been recognised for as the price-to-performance leader compared to other SCARA models in its price range due to its impressive speed versus payload capacity.
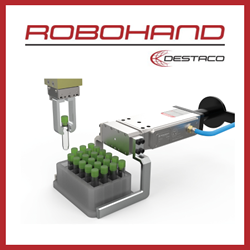
DESTACO - Revolutionizing Industrial Automation
Looking for a reliable solution to enhance your automation process? Look no further than the DESTACO Robohand Grippers. These grippers are designed for the modern world of robotics, offering unparalleled performance and precision. Whether you need to grip fragile items, irregularly shaped objects, or heavy-duty components, the DESTACO Robohand Grippers have got you covered. Their modular design allows for quick and easy customization, ensuring a perfect fit for your application.

Oriental Motor USA - Ideal for AGV/AMR Applications
The BLV Series R Type brushless DC motor (BLDC motor) speed control system offers the design of motor and driver significantly reduced in size and weight, yet high-power, and contributes to the battery driven automation. The BLV Series R Type is compatible with the two interfaces of Modbus (RTU) and CANopen communication.
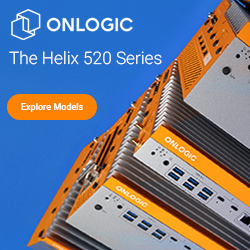
OnLogic's Helix 520 Series of Scalable Fanless Computers
The Helix 520 series utilizes the latest Intel Core Ultra processors with integrated edge AI capabilities to deliver exceptional performance and industrial-grade reliability for demanding applications in automation, robotics, machine vision, and more. Its unique modular design allows for flexible scaling of CPU and GPU performance, while robust connectivity and expansion options ensure seamless integration.
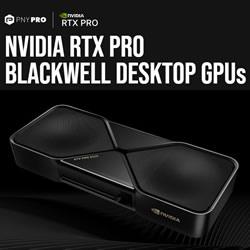
NVIDIA RTX PRO™ BLACKWELL DESKTOP GPUs
NVIDIA RTX PRO™ - Built for Professionals - NVIDIA RTX PRO Blackwell Desktop GPUs feature the latest breakthroughs in AI, ray tracing, and neural rendering technology to power the most innovative workflows in design, engineering, and beyond.
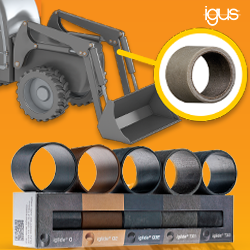
igus® - triflex® R robot dresspacks
Properly managed cables on a multi-axis robot are the difference between successful, failure-free operation and frequent unplanned downtime and lost profits. Discover how triflex® robot dresspacks are designed to protect cables in multi-axis motion - extending cable life, minimizing costs, and reducing unplanned downtime.