UltraFlex demonstrates induction soldering of 4 different copper tube assemblies within 1 minute
Using the same induction heater for all pipe assemblies, it took a minute to accomplish the soldering process for all 4 joints. The result was strong, reliable and consistent joints, done at a fraction of the time and costs required with traditional, flame-based soldering.
The time-efficient, highly repeatable process of induction soldering for copper tube assemblies has been demonstrated by UltraFlex Power Technologies. The company - a leading manufacturer of digitally-controlled induction heaters - published the showcase in line with its efforts to demonstrate the successful and efficient usage of induction heating to replace traditional, open flame-based heating.
In this test application, performed for a manufacturer of water heaters, UltraFlex demonstrated the induction soldering process for 4 different sizes of copper pipes and fittings - with size ranging from 0.25'' OD to 2.5'' OD (6.35 mm to 63.5 mm).
An UltraFlex induction heater from the UltraHeat SM series had been used to accomplish the soldering. UltraHeat SM are compact 5kW induction heaters. Operating with either a water-cooled or air-cooled remote heat station, they feature adaptive digital phase control providing efficient operation in a wide frequency range.
The induction soldering process was performed using a custom induction soil, which delivered precise heat to the desired area. Preformed solder rings applied to the joints ensured consistent and repeatable soldering results.
Using the same induction heater for all pipe assemblies, it took a minute to accomplish the soldering process for all 4 joints. The result was strong, reliable and consistent joints, done at a fraction of the time and costs required with traditional, flame-based soldering. The soldering process required no specific environment, and guaranteed high-quality result, with no dependency on the operator skills. Finally, the induction soldering was a completely safe process, ensuring compliance with all company safety regulations - it was safe both for the operator and safe for the environment, due to the lack of open flame, noxious emissions and fumes.
Find out more at:
https://ultraflexpower.com/
Contact us at:
+1.631.467.6814
uptnews@ultraflexpower.com
About UltraFlex Power Technologies:
UltraFlex Power Technologies (ultraflexpower.com) offers the most advanced and innovative digitally controlled induction heating equipment in the industry. Its compact modular and flexible systems are used for a wide variety of induction heating, casting and melting applications.
Featured Product
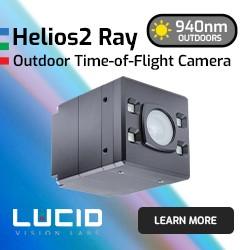