New Multi-Axis Alignment System for Silicon Photonics Automation Applications, from PI
Achieve first light search and alignment up to 100X times faster.
Auburn, MA - PI's family of photonics alignment automation systems has expanded with a new air-bearing-based multi-axis assembly and an EtherCat-based high-performance motion controller with embedded alignment algorithms. The unique combination of direct-drive maintenance-free air bearing alignment stages with sophisticated first light search and alignment routines result in extraordinary time savings - a critical factor in silicon photonics alignment automation.
How the Alignment System Works
The F-143 alignment system is based on three A-143 air bearing stages in an XYZ configuration. Each axis provides a travel range of 25mm, with a maximum velocity of 250mm/sec, and acceleration up to 10m/s2. Preloaded air bearings guarantee exceptional flatness and straightness of 0.25µm and 0.05µm, respectively. The vertical axis stage is equipped with an adjustable counterbalance and brake mechanism to offset the force of gravity on the motor and prevent potential collisions with a SiPh wafer in the event of a power failure.
A special, EhterCat-based motion controller with embedded photonics alignment algorithms and user-friendly software allows the system to perform alignments up to 100 times faster than conventional optical alignment engines.
Wear-Free and Clean-Room Compatible
The use of friction-free, wear-free, and maintenance-free components along with the absence of lubricants makes the air bearing automated alignment system ideally suited for silicon photonics waver probing and other clean-room applications.
Absolute Encoder Option
A key feature of these stages is the choice of encoders, including absolute and incremental options. Absolute encoders provide explicit position information, facilitating precise determination of each angular position without the need for incremental counting. This feature ensures immediate availability of position information upon power-up, enhancing operational efficiency and safety.
Industries
Served industries include optics, photonics, silicon photonics.
Featured Product
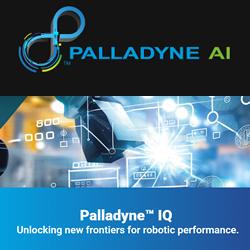
Palladyne™ IQ - Unlocking new frontiers for robotic performance.
Palladyne™ IQ is a closed-loop autonomy software that uses artificial intelligence (AI) and machine learning (ML) technologies to provide human-like reasoning capabilities for industrial robots and collaborative robots (cobots). By enabling robots to perceive variations or changes in the real-world environment and adapt to them dynamically, Palladyne IQ helps make robots smarter today and ready to handle jobs that have historically been too complex to automate.