A comprehensive Del Monte quality initiative sought to ensure product code legibility, and improve labeling accuracy and overall traceability of its canned fruits and vegetables.
Contributed by | Microscan
Customer Profile
With its products found in the cupboards and pantries of 8 out of every 10 homes in the U.S., Del Monte Foods is a household name in the U.S. and throughout the world. Known as a producer and distributor of high quality fruits and vegetables, it comes as no surprise that Del Monte is a company that takes quality seriously – from the freshness of its produce to the accuracy of its packaging.
Requirements:
- Ensure legibility of printed product codes
- Improve labeling accuracy
- Increase overall traceability
Project
- Implement vision inspection system to read OCR text and barcodes on canned fruits and vegetables
Solution
- GigE camera system and Visionscape® Machine Vision Software with custom user interface by Tensor ID
Result
- Improved accuracy, peace of mind, and cost savings for Del Monte; better quality for the consumer
The Challenge
As a testament to this commitment, the company recently undertook an initiative to improve the quality and traceability of its canned products. Del Monte wanted to ensure that the product code printed on the top of the can matched both the contents inside the can and the label that is applied to the can. They also wanted to verify that the product code was readable to be sure that products could be easily traced back to key points in the canning and packaging process. Without an error-proofing system in place, incorrect codes resulting from human error, and missing or unreadable codes caused by printer faults, posed several risks including mislabeled products reaching customers, accidental product mix-ups on the line, mixed products shipped to customers, and ultimately consumer safety risks and costly product recalls. The company needed greater peace of mind that its packaging process was being done properly and its products were leaving the facility in the correct condition.
After researching numerous companies to find the technology that would best fit its needs, Del Monte chose to work with Tensor ID, Inc., a provider of factory automation solutions based in Oceanside, CA. With expertise in auto ID and machine vision, Tensor ID designed and installed a custom machine vision inspection system that incorporates Microscan’s Visionscape® Machine Vision Software with multiple cameras positioned along key points of the packaging line. The solution accomplishes three primary objectives:
1. Improved quality and accuracy of the printed product code on every can
2. Assurance that every can receives the correct label
3. Improved overall traceability of canned fruits and vegetables
Del Monte recognized the benefit that automated vision inspection provides both to the consumer from a quality standpoint, and to the company in terms of reduced waste and cost savings. Accurate labeling assures the reseller and end-user of the product that there will be no surprises when opening the can. Inspection is critical for compliance with allergen labeling and prevents product recalls due to mislabeling. Expanded traceability enables the company to limit the extent of a recall should one become necessary, and speeds troubleshooting by helping to identify precisely where an error has occurred.
As an Elite Distributor for Microscan, Tensor ID partnered with Microscan on this project for three main reasons: trust, technical support, and superior machine vision software technology. “For this project, we specifically partnered with Microscan due to the support and expertise of the entire Microscan organization. Everyone from the president to the local sales representative was involved in making the Del Monte project a success,” said Tensor ID President Stacey Swall. She added that Microscan’s engineering team consists of some of the best engineers in the industry. “Their entire team has gone above and beyond to support us in this project.”
The Solution
The PC-based vision system includes Gigabit Ethernet (GigE) cameras positioned at multiple key points throughout the packaging process, all of which are supported by Microscan’s Visionscape software. Visionscape supports up to eight camera inspection points per system and includes a comprehensive toolset for a wide range of inspection applications.
An enclosed camera positioned on a can seamer reads the variety code on the top of the cans.
The system inspects and verifies printed product codes, UPC/2D codes on product labels, and finished cases at varying operating speeds up to 1,200 cans per minute. Any code that is missing or unreadable is rejected from the line. If the system detects the wrong code, the line will shut down and alert the operator.
Custom user screens, created by Tensor ID, link Microscan’s Visionscape with the PLC and SQL database.
All of the data collected by each individual inspection point goes to the PC and is stored in a SQL database. A PLC provides the controls for the system. Tensor ID created a custom user interface that links the PLC, the PC, the database, and Microscan’s Visionscape software, to provide the analysis and control needed for this application and future applications.
The system inspects both UPC and Data Matrix codes on the product labels.
Because there were not any off-the-shelf systems on the market to satisfy all of Del Monte’s requirements, Tensor ID designed, built, and implemented a completely custom system, including intuitive user screens that enable employees to run the system and initiate line changeovers with minimal training. Operators can view pass and fail counts, view current and last failed images, adjust inspection tolerances along with camera settings, and request remote support from Tensor ID.
A camera reads the UPC code during the labeling process.
One of the biggest challenges in the project was attaining repeatable results reading the cans’ variety codes due to inconsistencies in print size, character spacing, and ink color. To solve this issue, Microscan’s Solutions Engineering Team developed a way of synthetically training characters using Visionscape’s Intellifind® and OCR vision tools. In addition, Del Monte has moved to standardize the printing of their codes in the OCR-A font to ensure longterm readability. “We also faced challenges of varying production line speeds, reading the printed code regardless of its radial orientation, different size cans, bright and dull finish of the cans, and an aggressive installation schedule,” added Swall. “We worked directly with the Del Monte engineering team to overcome these challenges.”
Microscan’s Visionscape software supports up to eight camera inspection points per system.
The Benefits
Within the past two years, Tensor ID has installed over 70 inspection points at six Del Monte locations within the United States. Proactive in its quality policies, Del Monte plans to incorporate even more error-proofing steps and additional inspection points into its process moving forward.
With the new system implemented, Del Monte can be sure that its canned fruits and vegetables are meeting the high standard of quality that has become synonymous with the Del Monte name. Gary Short, Distribution Supervisor at Del Monte, commented on the improved accuracy in their processes, which has ensured peace of mind for the company: “This system has met all of Del Monte’s demands for an automated inspection system that assures the correct label and packaging is being applied onto the correct brite cans. Since Del Monte Foods has installed this system on our high-speed label/packaging line, we have not received any customer complaints for mislabeled product. How great is that to know your customers are always getting exactly what they expect!”
The content & opinions in this article are the author’s and do not necessarily represent the views of RoboticsTomorrow
Comments (0)
This post does not have any comments. Be the first to leave a comment below.
Featured Product
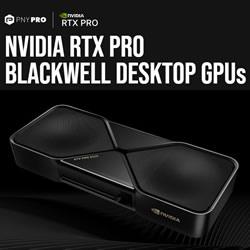