This disruptive technology enables Baxter to switch between tasks without retraining by using environmental markers, called Landmarks™, in conjunction with its existing, embedded vision system.
Contributed by | Rethink Robotics
Rethink Robotics today announced the availability of its new Robot Positioning System, a groundbreaking technology that will allow the Baxter collaborative robot to manage and adapt to ever-changing, real-world environments. As part of Intera 3.1, Rethink Robotics’ latest software upgrade, the Robot Positioning System helps users to more quickly and easily re-deploy the robot after common plant-floor variations occur, such as tables being bumped, fixtures being moved, and more.
This disruptive technology enables Baxter to switch between tasks without retraining by using environmental markers, called Landmarks™, in conjunction with its existing, embedded vision system. The robot is now able to recognize the original locations of the markers, and, when those locations change slightly, can mark the new locations and adjust its movements accordingly. By accounting for and adapting to common variability on the plant floor, Rethink Robotics is making it easier for manufacturers to deploy Baxter across multiple applications.
“Manufacturing robots have always been caged, not only to protect the workers around them from harm, but also to protect their precisely configured environments from being disrupted by those same workers,” said Scott Eckert, CEO at Rethink Robotics. “With Baxter, we brought the manufacturing robot out of its cage by making it safe enough to work next to people; and now, we’ve made it safe for the robot to work effectively in real-world conditions as well, by allowing it to adapt to everyday variations that people naturally produce.”
Users can now define Baxter’s environment with up to 20 Landmarks, saving time, manpower and resources when it comes to switching the applications Baxter is working on. The Robot Positioning System enables Baxter to adapt quickly to workstation changes of up to +/-50mm horizontally and within +/-10 degrees of rotation, by marking the new Landmark locations and accounting for any accidental movement or shifts in the workspace. The result is an automation solution that can readily adapt to common variations in its environment – saving considerable time and helping to keep production lines up and running.
One of the first customers to utilize the new technology, Praxis Packaging Solutions meets the diverse packaging demands for a wide variety of customers on a 24×7 basis. One of the defining characteristics of the Praxis production lines is rapid reconfiguration. Baxter provides flexible automated labor to meet those demands.
“We need our people and our automation to effectively work in a semi-structured, and sometimes variable, manufacturing environment. Rethink’s Baxter robot, particularly with the new Robot Positioning System, provides a solution that can finally adjust to the changing conditions of our work cells,” said Chris Hager, Information Technology Manager at the Michigan-headquartered Praxis Packaging Solutions. “No other robot built for manufacturers can come close to providing the flexibility and adaptability of Baxter.”
Rethink Robotics’ latest software release, Intera 3.1 strategically leverages multiple advantages of the Baxter robot, including smart software, multiple sensors and embedded vision. Through software upgrades, the company can deliver continuous innovation quickly and frequently, adding ever-increasing value to the inexpensive robot and further representing a game-changing approach to automation in manufacturing. The more a robot can do on its own, the less users have to do when redeploying it on a new task. And as the software advances, Baxter’s capabilities will continue to expand, again applying the power of software to enhance performance and ability.
Intera 3.1 will be available directly from Rethink Robotics and its nationwide network of partners. For more information, please visit www.rethinkrobotics.com.
Rethink Robotics, Inc. helps manufacturers meet the challenges of an agile economy with an integrated workforce, combining trainable, safe and cost-effective robots with skilled labor. Its Baxter robot, driven by Intera, an advanced software platform, gives world-class manufacturers and distributors in automotive, plastics, consumer goods, electronics and more, a workforce multiplier that optimizes labor. With Rethink Robotics, manufacturers increase flexibility, lower costs and can invest in skilled labor—all advantages in fueling continuous innovation and sustainable competitive advantage.
Committed to accelerating robotics innovation in manufacturing and beyond, Rethink Robotics’ Baxter Research Robot gives academic and corporate research environments a humanoid robot platform with integrated sensors and an open software development kit for creating custom applications.
Based in Boston, Massachusetts, the company is funded by Bezos Expeditions, Charles River Ventures, Highland Capital Partners, Sigma Partners, Draper Fisher Jurvetson, and Two Sigma Ventures. For more information about Rethink Robotics, please visit www.rethinkrobotics.com.
The content & opinions in this article are the author’s and do not necessarily represent the views of RoboticsTomorrow
Comments (0)
This post does not have any comments. Be the first to leave a comment below.
Featured Product
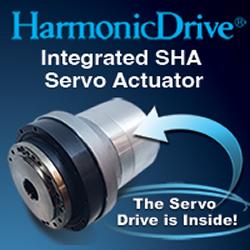