In the long term, job roles will shift away from their traditional remits and evolve to meet the needs of the modern, automated workplace.
Rita Brunk | Genfour
Since the industrial evolution there have been concern around machines infiltrating the workplace. Recent discussion around the rapid developments in automation has revived this concern and opened up new debates about the impact of automation on the future workforce. So, how will widespread adoption of robotics affect employees? We address the key questions below:
How to successfully implement management of change
The introduction of automation should be treated in the same way you would treat any other transformational change program: Prepare extensively and recognize the challenges that the change will present to your company and its employees.
It helps to break the transformation down into three levels of change: Individual change, organizational change and transformational management.
Individual change management is change at the most basic level that impacts your employees first. Individuals react differently when a new change project is introduced, such as automation. Some people are quick to adapt, while others may react with fear, anger or resistance. This can be a difficult area to navigate, so it’s important that your employees are as informed as possible throughout the process. These situations require crystal clear communication, professional training and guidance, so we’d recommend bringing in a change management specialist to work alongside the project team and stakeholders from the beginning.
It is natural for all humans to have fear of the unknown. With this in mind, find a way to allow your employees to interact with robots so that they will become more comfortable with them. One organization bought a dozen Lego Robot kits, put the employees in teams of two and gave them a challenge. They were given 3 hours to build the robots, and program them to maneuver a simple obstacle course laid out on the floor with tape. What started as fear at 9:00 A.M. ended with fun by noon.
The individuals are the hardest sell because the threat of a job loss is personal. They are also the most important because they are in the best position to identify automation opportunities. Another approach taken was to bring the employees that did the work in without leadership. Pose three questions:
-
What do you hate about your job?
-
What about your job can you do in your sleep?
-
What part of your job would you choose to give up?
The answers are redundant. They are also the repeatable tasks that are perfect for a robot. Employees then come to the conclusion that by automating the low level tasks the value of the remaining job content increases. The result should be a healthy list of opportunities.
Organizational change management is where specific teams or departments are impacted by changes. Moving teams towards improvements and new processes can help them to adapt more easily, as they can actively educate and support one another throughout the journey.
Transformational management requires the recognition of the impact on overall strategic planning, communication and leadership of the business. All automation initiatives and their impact should be factored in from an overall, company-wide vantage point. A perfect example of how to encourage the organization to make these improvements is to benchmark the metrics of the processes against other companies. The more work moved for the robot to handle, the better the metric to compare to peers in the industry whom may still operate with a full human staff.
Will the implementation directly result in attrition?
Implementing robotic process automation within your company does not negate the need for your human employees. In many cases, companies use part process automation to streamline repetitive, rules based elements of a task, allowing human employees to focus on more complex, value-add tasks.
Informing your employees about the impact of automation from the offset will mitigate any feeling of attrition and help them to adjust to the change.
Will the employees sabotage the operation?
Negative feelings toward automation is often caused by a lack of understanding of the reasons why a company has chosen to implement automation, and the benefits that it will bring to the organization.
As in any business transformation project, communication is key. Be transparent with your employees and let them know that robotic process automation will not replace their jobs – but it may alter them.
Computers and robots have made remarkable advances into the workforce in recent years, from the factory floor to banks and mobile phones. However these advances have altered, not replaced, professions, and have raised our living standards overall.
Long term impact on employees
While robotic process automation is a highly efficient solution to numeric, routine tasks, employees’ humane skillsets are still very much in demand. The ability to be flexible, interact effectively with other humans and draw on common sense to solve unexpected problems are skills that are invaluable, and robots cannot fully replicate these skills.
The initial transition towards an automated workplace may take some time for your employees to adapt to, but they will do just that, because they are human. In the long term, job roles will shift away from their traditional remits and evolve to meet the needs of the modern, automated workplace.
Look out for part eight in our ABC of RPA series, where we will be discussing whether it is possible for robots and humans to work side by side, in harmony.
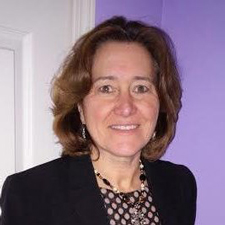
Rita Brunk is the Robotics and Automation Transformation Lead for the US at Genfour, the robotic process automation (RPA) and AI delivery specialist. Rita has seven years of automation experience within a shared services environment, which developed to incorporate robotics tools.
Prior to joining Genfour, Rita led a global shared services effort at Hewlett Packard for robotics. She opened and closed various captive shared services sites outside of the US, and several sites under her responsibility won SSON Excellence Awards for value creation in a mature shared series centre.
For the past 15 years, Rita has held a number of executive positions in a captive shared services environment focused on process optimisation and the development of analytics within the finance, HR, logistics, procurement and marketing functions. During this time, Rita oversaw large teams located in Michigan, India, Costa Rica, Argentina and Mexico. For the last two years, she led global efforts to reduce headcounts across all locations, implementing RPA to drive this progress.
The content & opinions in this article are the author’s and do not necessarily represent the views of RoboticsTomorrow
Comments (0)
This post does not have any comments. Be the first to leave a comment below.
Featured Product
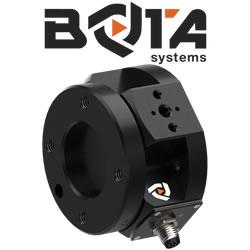