For the competition we will launch a horde of miniature robotic submarines called Marine Bees. They take their design from real bees, not just for the way they look, but also because they mimic the behavior of real bees and the operation of a hive to explore and image the ocean floor.
Interview with Shell Ocean Discovery XPRIZE Team Eauligo
Contributed by | Eauligo
How did you/your team decide to enter and pursue the Shell Ocean Discovery XPRIZE?
We were attracted to the Shell Ocean Discovery XPRIZE for a few reasons. As a company of engineers the first reason is the technical challenge. To succeed in the competition we need to find solutions that cross a range of domains, from materials and mechanical engineering to ensure our robotic submarines can survive the depths, artificial intelligence to control them in an unknown environment, data storage, communications, etc. From a technical viewpoint, after space exploration, remotely exploring the bottom of the ocean is the next biggest engineering challenge. The second reason for us to enter is for the exploration. The ocean is still largely unexplored so it is the one place on earth where there are still new discoveries to be made. It is really inspiring to discover and explore even a small area, knowing that no one in the world has ever seen it before.
Describe your approach to underwater mapping and how it relates to mimicking bird/fish/insect behavior. Does it involve flying, diving and swarming?
For the competition we will launch a horde of miniature robotic submarines called Marine Bees. They take their design from real bees, not just for the way they look, but also because they mimic the behavior of real bees and the operation of a hive to explore and image the ocean floor.
Just as the real bees leave their hive and fly into the fields and woods looking for flowers, returning to tell the other bees what they have found, our Marine Bee submarines do exactly the same. They dive down to the bottom of the ocean floor, spreading out to explore and map an area. They bring back their nectar, which for us is the data and images. Returning to the surface they share the data with the other Marine Bees so they can autonomously decide where to explore next.
The design of each Marine Bee is also unique, using components and manufacturing techniques from mass produced consumer products to drive down costs and produce a low cost, mass produced unit. They have many features of full sized Autonomous Underwater Vehicles but are smaller and cheaper. The real advantage comes from putting hundreds of these small and simple robotic submarines together. Multiple Marine Bees provide scalable and low cost exploration.
How does AI and robotics factor into your Shell Ocean Discovery XPRIZE solution?
Once our robotic Marine Bees dive under the water we have no control over them. At the depths they need to operate there are no practical data links so our Marine Bees have to be totally autonomous. The strength of our solution is that the AI rules that control our Bees are relatively simple and the complexity comes from combining the data from a large number of them, but each Marine Bee still needs to be able to navigate independently using its AI and sensors.
What kind of differences (pressure, light, temperature) do you expect to see in mapping the sea floor at 2,000 and 4,000 meters, as compared to current high resolution imaging at that has been done in much shallower sea floor areas, for example?
The pressure is the main factor at these depths. The design of any solution has to start with how to manage the strengths and the materials needed. It is one of the reasons we decided on lots of small robots instead of a fewer large ones. With a smaller robot size, the thickness and weight of material to survive at depth is reduced.
Light is also a factor because we cannot rely on any ambient light unlike imaging in shallow waters. This means we need to provide enough lighting which generally takes a lot of power and reduces the time that can be spent on imaging. Finally imaging in shallower waters does not involve significant travel to get to the depth you want to image. However for us, if we want to image something at 4000 meters that means our Marine Bees will be making an 8km round-trip just to get to and from the ocean floor. This adds constraints to ensure accurate navigation to get to the correct area and additional power requirements.
What challenges exist for the robotic components in your solution? What challenges do you see for the autonomous/hands-off functionality of your approach (AI focus)?
In most robotic developments we are designing a robot to complete some task in a known environment. We can see and understand, as programmers, what the robot needs to do, we just need to be able to give the robot enough AI to do it for itself. The main challenge for ocean exploration is that we as designers do not know what to expect. The deep ocean is largely unexplored, unmapped, and untouched. We simply do not know what type of situations our robotic Marine Bees will need to handle. How will they cope with the huge variety of terrain underwater, how will they navigate around obstacles, how will they manage an encounter with marine life? This is the real challenge for an autonomous solution. We cannot program it to manage every eventually so we need to make a decision about what situations we let the AI handle, and in which situations it may have to give up and return to the surface.
How is your XPRIZE team stretching the boundaries in regards to technology, integration, robotic skills and/or AI complexity? (Any or all)
Each area is challenging as we have to master them all to have a working solution. However the main challenges we face are actually the same as most mass produced products. We need our Marine Bees to the be small, relatively low cost and easy to manufacture in large numbers. We are not producing a complex, one-off design, we are trying to create hundreds of robots. So our design has to take into account not just the features and functions, but also how can the robots be produced in large quantities at a reasonable price. So the components and manufacturing techniques we use are closer to consumer products than industrial robot design.
What have you found to be the most demanding part of your solution development so far? What might you see as the most difficult part of mapping at such deep depths?
The most demanding part of the development is actually the testing. Due to our location we are lucky enough to have 2000m deep waters not far from shore, so we have an ideal test environment. However when we send a robot underwater, if there is a bug, we have a good chance of losing the robot and worse, not being able to tell which bug caused the problem. As soon as we get beyond a certain depth there is no way to have a telemetry or a data link back to the surface so if something goes wrong we have to hope our robot submarine can resurface so we can debug and find out what has happened. So it is actually this process of testing and debugging in the real environment that is one of the hardest parts of the development.
What provided the initial idea for your approach? Was there an “a-ha” moment?
Nature is always a good place to look to solve engineering problems. Nature has been designing things a lot longer than we have. Seeing a bee in the garden going from flower to flower gave the team leader the original idea. Each bee is exploring on its own, but there are lots of bees all doing that simultaneously to cover a large area. This inspired the team to build a solution that copied the bees.
What do you see in the future of robotic mapping of the ocean? Can your approach be applied to off-world, planetary exploration (fluid oceans of the Jupiter or Saturn moons, for example)?
Our basic solution is to use lots of low cost robots in a horde to map the ocean. One advantage is that it is scalable. If we want to map a large area of the ocean in a manageable amount of time and cost then using hundreds of small robots is a way to achieve this. We could get to the point where the robots could be dropped from planes or drones to reach parts of the ocean that would never be cost effective to map by ship.
This technique of horde robots certainly has applications in space exploration. Instead of developing large planetary missions that are expensive to launch and lost if there is a failure, we could imagine an interstellar version of our Marine Bees being launched in small groups as secondary payloads over multiple launches to save costs. We don't need them all to reach the oceans of Enceladus to return useful data.
What would you/your team do if you win the Shell Ocean Discovery XPRIZE and what are your future plans for your innovations?
The Shell Ocean Discovery XPRIZE is a great catalyst and driver of innovation and has given us targets and motivation to develop new technology. However we know that whether we win or lose the XPRIZE it is not the end of the story. This technology is just one part of developing a new business area for our company and as usual we will need to find target markets and commercial opportunities to grow it into a sustainable business. On a personal note, as team leader, I have an interest in Marine Archeology so definitely I will be using our Marine Bees in that area as well.
The content & opinions in this article are the author’s and do not necessarily represent the views of RoboticsTomorrow
Comments (0)
This post does not have any comments. Be the first to leave a comment below.
Featured Product
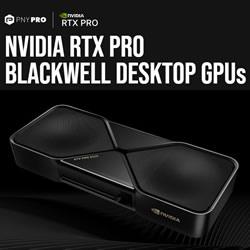