Robotic testing using a forming gas or helium is proving to be the easiest, most efficient way to ensure fuel-injection system safety and reliability without the need for additional manpower.
Automakers and Their Suppliers Turning More and More to Robotic Testing
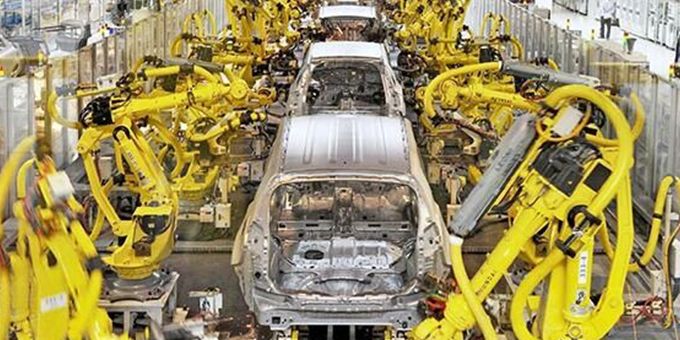
Thomas Parker, North American Automotive Market Sales Manager | INFICON
Carmakers and their suppliers today are relying more and more on robotic leak-detection systems to reduce costs, improve quality and increase assembly-line speeds.
INFICON, a major global supplier of leak-detection equipment, expects to see a significant increase in robotic leak testing in the regulation-sensitive arena of auto manufacturing in years to come.
Thomas Parker, the company’s North American automotive sales manager, says, “Barely five percent of all U.S. automotive plants currently have robotic leak-detection systems.
“We expect that number to climb to 20 percent or more within the next four to five years. The process will accelerate even further as new products are added and existing production lines are improved.”
Static robotic leak-detection today is used on automotive assembly lines to test a variety of components, including fuel systems, air-conditioning parts and transmissions. The move from low-pressure fuel injection (40-60 psi) to much higher pressure direct-injection systems (2000-3000 psi), for example, has dramatically increased the need for fuel-system quality checks.
Robotic testing using a forming gas or helium is proving to be the easiest, most efficient way to ensure fuel-injection system safety and reliability without the need for additional manpower.
“We also see a big push towards robotic testing in the refrigeration and air-conditioning industries which are faced with stiff foreign competition,” Thomas points out.
“Headcount reductions, line-speed increases and other efficiency improvements are essential stepping stones in the never-ending battle to remain competitive.”
Parker notes that the joints and connection points on many refrigerators and home air conditioners are similar from unit to unit and easy to check robotically. To maintain or reduce operator head count along with a need to improve quality and efficiency, a number of companies have chosen to put a sniffer probe into the hands of a robot.
Sniffer probe mounted on robotic arm at known problem area.
He adds that robotic testing is a critically important first step in eliminating costly human error that invariably takes place when tests are conducted manually. And in the age of the coronavirus crisis, robotics also support the need for social distancing.
“How you leak test is just as important as the equipment you use”, Parker says. “A properly installed robotic station can make the difference between stellar product quality and an expensive exercise in futility. Just like a great chef carefully sets up his or her kitchen with the right equipment, great product leak testing requires attention to detail.”
INFICON recently published a white-paper guide for original equipment manufacturers and their suppliers that provides important pointers for successfully installing robotic leak-detection systems. Available online, the paper also discusses differences between static and dynamic “sniffer” testing; why a leak detector’s gas-flow capacity is important, and which test configurations are most suitable for specific applications. The paper is available at the following hyperlink: Robotic Leak Testing White Paper or through the provided QR code.
INFICON’s white paper includes five important tips to help manufacturing engineers and quality control managers avoid costly mistakes when installing robotic leak-detection systems:
Tip #1: Meet Equipment Requirements – Be sure to have the proper equipment. Whether the process will be static or dynamic will determine exact equipment needs. Static testing can be used if potential leaks occur at specific locations.
A dynamic test is required to validate larger surface areas. With dynamic testing, a “sniffer” sensor moves over a test piece at a speed that will allow for the most reliable test results.
Static point-to-point leak testing that requires a robot to move from one connection to another is a popular application in a variety of industries. High test-gas flow is important in static testing because the sniffer tip often cannot get close enough to the part. High gas flow gives reliable results even at some distance from the leak location.
Dynamic testing in the auto industry is used primarily for checking the seams of lithium-ion battery packs. Test gas is introduced into the battery pack and a robotic arm equipped with a sniffer probe moves along the seam to test for leaks. Robots also are employed to dynamically test continuous weld lines on welded steel fuel tanks. Fast test-gas flow rates are important in dynamic test situations since they allow the robot to move more quickly along areas of the part to be tested.
In the HVAC industry, static testing currently is used to check critical joints within a system. Quality control engineers also are considering the use of robots to dynamically test refrigerant coils.
Static vs. Dynamic Leak Testing
Tip #2: Avoid Crosswinds! – A draft of air during a sniffer test will affect reliability. For best results, the test area should be enclosed whenever possible. Typically, test stations are enclosed in cages to ensure worker safety.
Substituting acrylic glass for caging material will not only protect employees, but also will shield the test area from gusts of air caused by HVAC systems, passing forklifts and other equipment.
Tip #3: Calibrate Carefully – and Regularly – Test equipment always should be properly calibrated and checked frequently – at least once every hour when possible. Extremely important to assure reliable results, calibration tests can be performed quickly and easily.
Calibration protocols depend on part volume, part specifications and a company’s internal recall process if a failure occurs between process validations.
Tip #4: Watch Test Background – The most common causes of false test readings are high background concentrations of test gas. Ways to avoid “false positive” results caused by background sources include:
-
Evacuating parts both before and after each test;
-
Monitoring tracer-gas fill processes to assure the part is connected correctly;
-
Locating gas-supply cylinders a good distance away from test stations, and
-
Inspecting gas supply lines for leaks.
Tip #5: Avoid Forming-Gas Cross Contamination – Forming gas (95 percent nitrogen / 5 percent hydrogen) often is used as a test gas. Industrial environments often contain other sources of hydrogen not always obvious to testers. Be on the lookout, for example, for forklift-truck exhaust gases or for lead-acid battery charging stations where hydrogen is a process byproduct.
“Companies that have relied more heavily on the automation of their manufacturing processes have been less likely to shut down during the current pandemic crisis, Parker notes finally. “Because of social-distancing requirements, plants with more labor-intensive production lines tended to be the first to shut down and the last to restart.”
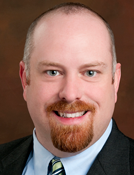
Thomas Parker is responsible for INFICON’s automotive sales in North America, supporting the company’s growing focus and investment in the automotive market. He is considered an industry expert on leak testing of automotive parts, systems and final assembly processes.
The content & opinions in this article are the author’s and do not necessarily represent the views of RoboticsTomorrow
Comments (0)
This post does not have any comments. Be the first to leave a comment below.
Featured Product
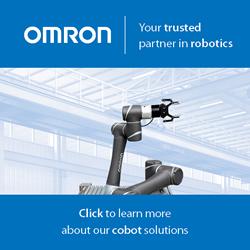