Paperless automation saves space, money, and boosts security. The ease of transferring information while promoting the environmentally sound choices makes this process logical for all manufacturers, particularly food manufacturers.
Automation Means Going Paperless
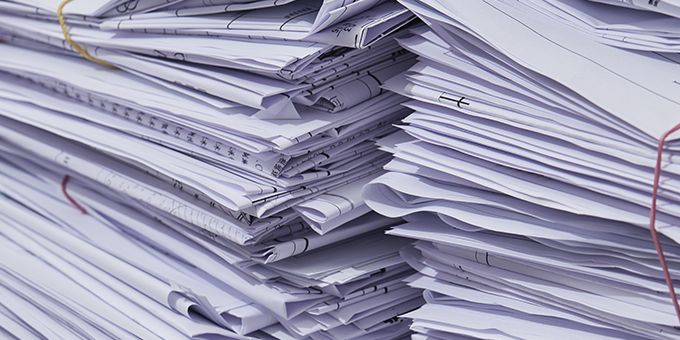
Andrew Schutte, General Manager | COUNTERPART ETO ERP
The benefits of going paperless are often overlooked as the primary advantage of automation. This oversight seems counterintuitive since paperless operations saves time. The time savings no longer required include filing, organizing, and searching for paper documents; time is better spent on more productive tasks.
Paperless automation saves space, money, and boosts security. The ease of transferring information while promoting the environmentally sound choices makes this process logical for all manufacturers, particularly food manufacturers.
Egan Food Technologies, based in Grand Rapids, MI, supplies customized food process machinery for the confectionery, baking, and snack food industries. The company also rebuilds, services, and supplies parts and auxiliary equipment for chocolate molding, depositing, extruding, slab forming, and baking equipment.
Joe Cisler (pictured right), Design Engineer at Egan, shared how the company went paperless and increased access from the shop, purchasing, and engineering. Cisler added, “We are down to one printer basically, and the only reason that is being used is for accounting records. Everything else from manufacturing to drawings is paperless.” The company uses COUNTERPART ERP, an ETO (Engineer-to-Order) solution, giving the entire team real-time access.
“Everybody can see everything digitally without having to print anything. COUNTERPART’s ability to directly integrate with PDM and automatically send the correct CAD files to vendors saves countless hours and eliminates mistakes,” noted Cisler.
SOLIDWORKS integration essential for automating custom food industry equipment
The main feature Cisler was seeking was a direct correlation to SOLIDWORKS. The company was using outdated technology to access database software that had no communication with SOLIDWORKS. Cisler chose COUNTERPART which has two-way communication direct to SOLIDWORKS.
Chocolate molding equipment often requires custom engineering to meet the food engineering specifications; this fact exists for beginning chocolatiers to large food processing factories. The heart of molding plants is the PLC/servo-controlled depositor, which optimizes center-to-shell ratios and overall product weights. Since each chocolatier is unique, Egan builds ETO solutions which utilize robotics and automation.
This allows for flexibility which can be easily adapted for future growth, making mold plants a cost-effective solution. Chocolate molding plants must have the capacity to be customized with indexing or continuous chain circuits. Food customers with existing circuits require that custom-built depositors fit those circuits, regardless of original manufacturer.
Gary Sigler, Plant Manager of Daffin’s Candies commented, "The new molding line has benefited us greatly by eliminating production downtime increasing production output and revenues. Most importantly, the one-shot depositor is producing a higher quality product with a better center to shell ratio. The ability to make fine adjustments to the process is invaluable."
© 2021 COUNTERPART ERP
About Andrew Schutte
Andrew Schutte, General Manager at COUNTERPART ETO ERP, has been mechanically inclined from a young age. Growing up in his father’s machine shop he was provided a valuable hands-on education of machining, fabrication, and mechanical design throughout high school. He moved to designing automation assembly equipment and machine design supporting the automotive, office furniture, medical equipment, and consumer product industries.
The content & opinions in this article are the author’s and do not necessarily represent the views of RoboticsTomorrow
Comments (0)
This post does not have any comments. Be the first to leave a comment below.
Featured Product
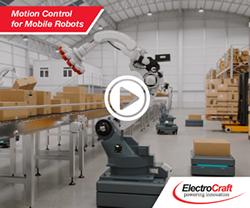