The Smart Factory at Wichita (TSF@W) provides a risk-free environment for companies to explore the art of the possible and gain insight into the latest technologies through an immersive, hands-on experience.
Digital Transformation and the Smart Factory
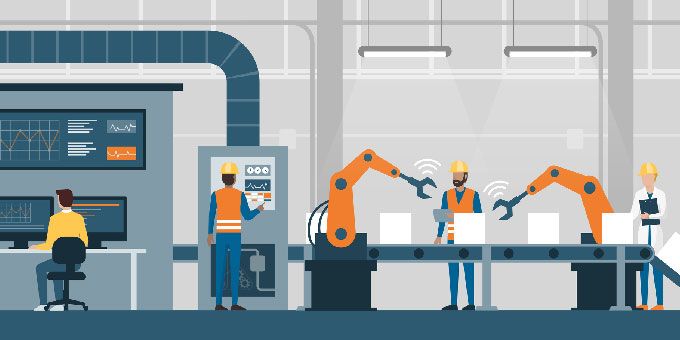
Q&A with Jason Bergstrom | Deloitte
Please explain how Deloitte and Wichita State University (WSU) are helping companies accelerate their digital transformations with their immersive smart factory experiences.
Many manufacturers have struggled to adopt new digital technologies and solutions in recent years. Part of the challenge is that most manufacturers don’t have an appreciation for what’s possible, and as a result default to doing things the same way they have for years. The Smart Factory at Wichita (TSF@W) provides a risk-free environment for companies to explore the art of the possible and gain insight into the latest technologies through an immersive, hands-on experience. Accelerating a company’s digital transformation agenda is much easier once they have a strong working knowledge of what’s possible and our partnership with WSU and our Ecosystem of sponsors bring that experience to life in a fun and controlled environment.
What is your vision for manufacturing over the next 5+ years?
Manufacturing and technology have started to collide at an exponential rate. Five years ago, it was a ‘nice to have’ to have digitized part of your operations and supply chain. Today, accelerated by ever-increasing customer demands and external pressures such as the COVID-19 global pandemic, manufacturers need to rapidly adopt a digital mindset to survive and compete. I expect to see a rapid rise in digital adoption in the next five years as organizations automate and enhance their operations. I anticipate that companies will dramatically increase productivity and efficiency throughout their manufacturing footprint and empower operators to make more informed, real-time decisions.
What are the biggest obstacles a manufacturer faces implementing smart factory technologies?
Many manufacturers have the natural tendency to focus too much attention on the technology associated with a Smart Factory implementation. As it turns out, the much more difficult part of successfully delivering against a Smart Factory ambition is the fundamental shifts that are required to how work gets done and who does the work. Shifting ways of working through streamlined and improved processes and training manufacturing employees on new responsibilities, techniques and solutions are the most difficult hurdles to delivering the value and outcomes that organizations desire. As technology continues to evolve at an alarming rate, manufacturers have access to solutions that were mere impossibilities in the past. Ensuring that you get the most from new technologies requires a keen eye on the broader process and workforce transformation that will make all the difference in delivering sustainable results.
Why is it so important that manufacturers embrace technology and make the digital transformation?
Becoming digital is no longer an option – it’s a requirement. The market today is as complex as any time in history – increasing customer demands, rapidly changing customer preferences and the emergence of new supply channels are all putting enormous pressure on manufacturers. Embracing technology allows manufacturers to sense and react to demand changes faster, increases flexibility to meet broader and more complex customer needs and improves operational performance to compete with lower cost manufacturers. Those that choose to avoid digital transformation of their operations will be quickly leapfrogged by their competitors and will struggle to compete.
What are the technologies that will be most impactful over the next year?
Many manufacturers will transform their supply chains by optimizing for resilience and risk. This will come through newer interaction models such as:
- Digital experience/reality assisting the workforce in tasks such as design or remote support
- Data analytics and artificial intelligence to predict and augment decisions from assembly operations to material movement
- Distributed platforms to run the ML/AI in the location that best optimizes the cost and computation needed for the data connectivity in support of those systems
- Automation opportunities through the deployment of traditional robots, collaborative robots, and drones will make teams more productive and safer
How are companies of all sizes implementing smart factory technologies today?
By combining the strengths of the human workforce with machines and platforms, manufacturers can achieve exponential improvements in customer service, output, and productivity. While the scale may be different based upon company size, it’s critical to focus on what will bring the most value to your particular business. Our Smart Factory Team helps frame smart factory technology advancement areas in context of the “Great 8” use cases (ranging from Factory Asset Intelligence to Energy Management) to help identify the most impactful areas for that specific company’s size and maturity. (More on the Great 8 use cases can be found here).
What are ways smart factories are enabling the digital transformation of the future?
The core manufacturing process itself improves with smart factory transformation by leveraging machine and process data. This establishes optimal setpoints for a specific operation, improving cycle time and ensuring that products are produced with the highest quality. Additionally, there are several decisions made during normal factory operations, which were historically incumbered with lack of timely supporting data. Today, Smart Factories supply operators and machines with timely insights to further improve operations, enabling digital transformation of business models.
About Jason Bergstrom
Jason, principal with Deloitte Consulting LLP, is Deloitte’s Go-To-Market Smart Factory leader responsible for sales, marketing and ecosystem activation. Mr. Bergstrom has helped numerous organizations deliver complex, global manufacturing transformations with a focus in the oil, gas, and chemical industry. As a certified Lean Six Sigma Master Black Belt, Jason specializes in delivering process and operations excellence projects and leading efforts to develop internal continuous improvement capabilities for clients. He holds an undergraduate degree in chemical engineering from the University of Colorado Boulder and an MBA from MIT’s Sloan School of Management.
The content & opinions in this article are the author’s and do not necessarily represent the views of RoboticsTomorrow
Comments (0)
This post does not have any comments. Be the first to leave a comment below.
Featured Product
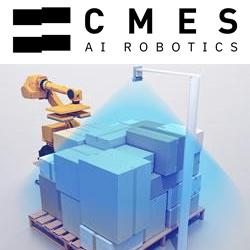