When it comes to efficient and effective material handling, conveyors are an invaluable component of any system. Conveyor systems streamline processes, reduce manual labor costs, and optimize productivity by moving materials from one place to another.
The Essential Role of Conveyors in Your Material Handling System
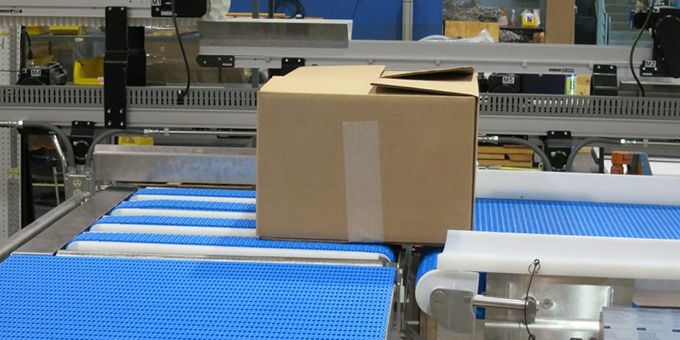
Article from | Dorner Conveyors
Why You Should Prioritize Optimizing Your Material Handling Process with Conveyors
If you have a manufacturing or packaging operation, it is critical that you optimize your material handling process to maximize efficiency. Improving your material handling system with conveyor systems can help reduce costs, improve safety, and increase productivity.
Improve Time and Space Management.
By increasing the speed of material transportation, conveyors help improve time management and reduce downtime. This allows you to meet your deadlines without relying on your employees to perform tedious strenuous labor and instead allowing them to focus on more mentally-demanding tasks.
Reduce Operation Costs
By improving your material handling system with the integration of conveyor systems, you can also reduce your operational costs by decreasing downtime, minimizing handling costs across applications (including packaging and distribution), and prevent costly product damages or loss through precision conveying.
Enhance Product Flow
Updating your system with conveyors can provide a continuous product flow, helping to prevent pile-ups and improve the speed of your production line. This will help you optimize your processes and get products out more quickly without having to slow down or stop to manually move materials from one station to another.
Conveyors can also help to improve overall product quality. By ensuring that products move in a steady and consistent flow, there is less risk of damage due to manual handling or uneven movement.
Increase Productivity and Efficiency
Conveyors not only streamline your material handling process, but they can also help you increase productivity and efficiency in the workplace. With increased speed, you can produce more products per hour with fewer resources. Additionally, fewer people are needed to move materials from station to station, freeing up more time for other tasks.
Key Elements of an Effective Material Handling System
When designing and implementing an effective material handling system, it’s important to take the following elements into consideration.
Material Handling Equipment
The right equipment is essential for ensuring efficient material movement. As the backbone of material handling systems, conveyors are responsible for providing a reliable way to move materials quickly and efficiently. Other essential equipment may include:
- Forklifts
- Pallet jacks
- Hand trucks
- Platform trucks
- Cranes or hoists
- Stackers
- Bucket elevators
- Reclaimers
- Hoppers
These pieces of equipment, along with conveyors, are critical for the precise and efficient movement of products and raw materials throughout the supply chain.
Automated Solutions
Automating your material handling process is key to optimizing productivity. Automation increases efficiency by minimizing the need for manual labor. Automated systems can be programmed to perform specific tasks such as sorting and labeling, taking the strain off of operators.
Common automated solutions for material handling applications include automated guided vehicles, which use computer-controlled navigation to move materials around a facility, and robotic arms, which can pick up items or perform repetitive tasks with precision.
Planning, Standardization, and Simplification
Prior to implementing a new or improved material handling system, it’s important to take the time to plan out each step and standardize your processes. This allows you to anticipate potential issues that may arise, such as bottlenecks or downtime, and develop solutions in advance. It also helps simplify your system by removing unnecessary steps that could slow down operations.
Take a collaborative approach when defining your needs and objectives from the start to guide your system, getting input from all relevant teams (across management, finance, operations, and more). Standardize your equipment and simplify your processes to ensure optimal performance, minimized waste, and increased productivity.
Ergonomics and Safety
Ergonomics is the science of designing products and processes to reduce human physical stress. When designing a material handling system, you should take into account ergonomic principles to ensure employee safety and comfort. This includes providing adequate training on how to use equipment, regular maintenance of equipment, and incorporating safety features such as guardrails or seats to reduce fatigue.
Implementing certain equipment, including conveyor systems, can further reduce ergonomic strain, resulting in decreased risk of injury and improved worker satisfaction.
Environmental Impact
The impact of material handling on the environment can be greatly reduced with certain practices, such as reducing waste and practicing energy conservation. Consider implementing a waste management system to reduce the amount of materials being thrown away.
Additionally, ensure that your equipment is running efficiently and doesn’t cause unnecessary pollution. When handling hazardous materials, implementing and maintaining sufficient safety protocols is critical.
Custom Conveyors for Your Material Handling System Needs
When selecting a conveyor system for your material handling needs, custom solutions can provide a more tailored approach and greater flexibility. Custom conveyors allow you to choose the right components and features that meet your specific requirements, while also reducing downtime and increasing efficiency.
Custom conveyors from Dorner can satisfy your specific material handling needs with features such as:
- Low profile designs for easy integration into existing systems
- Easy-to-clean frames that reduce bacteria growth and contamination
- Heavy duty construction for long-term durability and reliability
- Modular belt systems that can be reconfigured quickly in case of changing product flow
- Automated controls for improved performance and operation
- Sanitary designs to meet the demands of food processing and pharmaceuticals
Streamline Your Material Handling System and Maximize Productivity With Dorner Conveyors
Whether you’re looking to upgrade your current material handling system or start fresh, custom conveyors from Dorner can provide a tailored solution that meets the unique needs of your application. With our custom material handling solutions, you can ensure safe and efficient operations while maximizing productivity and throughput.
The content & opinions in this article are the author’s and do not necessarily represent the views of RoboticsTomorrow
Comments (0)
This post does not have any comments. Be the first to leave a comment below.
Featured Product
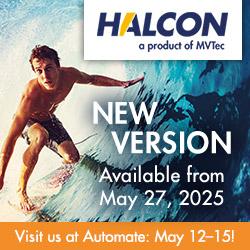