The advantages of all-electric injection moulding machines demonstrate how automation and robots can help manufacturers bring their operations back home to the UK. Reshoring can be achieved with cost- and energy-efficiency as well as productivity benefits.
Reshoring with robots - UK manufacturers can use automation to bring production back home
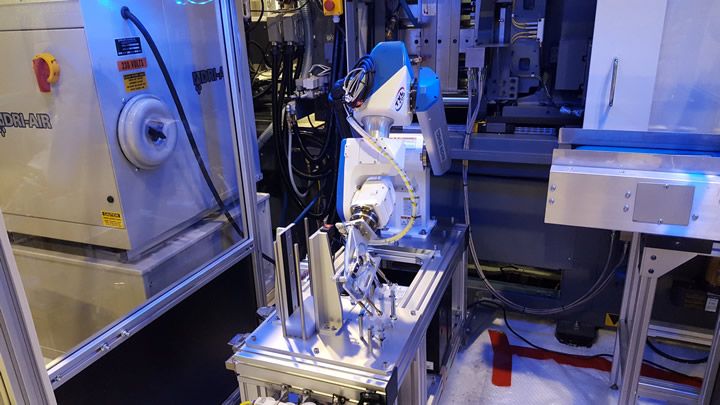
Nigel Smith, CEO | TM Robotics
Manufacturers hope that, by reshoring, they can bring supply closer to demand in order to achieve shorter lead times and better service against the current global supply chain issues and increasing-import costs. Here, Nigel Smith, CEO of industrial robot specialist TM Robotics, the official distributor of Shibaura Machine, explains the vital role of advanced robotics in these trends, such as the use of Shibaura Machine’s robotics-led injection moulding technologies to support the booming growth in injection moulded medical devices.
“Mama, I’m coming home,” Ozzy Osbourne once sang, “here I come, but I ain't the same.” This could apply to manufacturers that are trying to quickly reshore production back to their own countries, under slogans such as “buy British” in the UK. In doing so, companies hope to mitigate supply chain issues caused by the after-effects of the COVID-19 pandemic, Brexit, the Ukraine conflict and material shortages.
But, to paraphrase Ozzy, manufacturing is no longer the same. Gone are the pre-Covid days when managers and suppliers could take supply chains for granted, and manufacturing was outsourced to countries like China at a significant profit. Instead, businesses are under pressure to reshore their production while keeping it economically viable, reducing lead times and improving quality of service, despite the supply chain disruptions.
However, according to the London School of Economics, robotisation might play a vital role in helping manufacturers bring their operations back home to the UK.
Injection moulding, used to manufacture plastic products for a range of sectors, is expected to see significant growth over the coming decade.
High production
Take injection moulding for instance, a manufacturing process that Digital Journal predicts will see booming growth between 2023 and 2030. Injection moulding is used to manufacture a huge variety of plastic parts — everything from medical devices to takeaway food containers — with good repeatability, consistently high production with low waste, and a low-cost-per-part. However, the injection moulding process can be expensive, overall. Estimates range from £3,000 to £100,000, relative to the size of the product, the volume of manufacture and the speed of production.
How can automation and robotics lower these costs? First, let’s consider that 90 per cent of the costs of injection moulding are attributable to the electricity used to power the injection moulding machine itself. Machines powered by a hydraulic motor are often favoured because they produce higher energy levels and higher injection pressures, and the initial cost of the machine is lower.
But, there are disadvantages. The machine’s hydraulic power is connected to an electric power unit, so works at maximum capacity during the entire moulding process and even consumes energy when idle. These factors significantly impede the energy efficiency, and are why manufacturers should instead consider all-electric machines.
The SXIII can integrate easily with robots like the TVL700 for additional performance benefits.
Energy efficiency savings
Let’s examine the case of Lotan, a TM Robotics customer and manufacturer of plastic containers. The UK-based company relies on Shibaura Machine’s all-electric injection moulding machines (IMM) supplied by TM Robotics. Performance benefits of the IMM include a range of clamping force from 50 to 2,500 tons, which can be calibrated by a digital direct screw transfer (DST) control for added production flexibility. While all-electric machines are initially more expensive with lower injection pressures, they greatly outperform hydraulic versions in a variety of other ways.
Advantages of all-electric IMMS include higher rates and speeds of injection, because they rely on toggle clamping rather than direct pressure clamping, which is better for high-speed injection moulding. Other benefits are improved dry cycle times and the overall stability of the mould itself.
But what about the energy savings? Performance tests by Shibaura Machine measured its EC650SX-61B IMM, with a clamping force of 650 tons, against a hydraulic servo machine. It delivered a 51 per cent energy reduction. Another EC-SX model, the 1,800 ton EC1800SX-155B, was tested against a competing all-electric IMM. Although both machines had the same energy consumption, the Shibaura Machine IMM delivered a faster cycle time, for overall energy efficiency savings of 30 per cent.
Bringing it all back home
Meanwhile, Lotan has experienced 20 to 40 per cent lower running costs and 35 per cent faster cycle times with the all-electric IMMs, plus a lower cost-per-mould.
Thanks to these benefits, Lotan has ordered several more Shibaura Machine IMMs from TM Robotics, specifically its newest SXIII range of injection moulding machines. An additional benefit is that the SXIII can be easily integrated with Shibaura Machine robots like the TVL industrial robot range that are compact, lightweight and space saving. Each robot has varying reach and payload specifications, and a longer arm length compared with previous robot ranges.
The advantages of all-electric injection moulding machines, like the EC-SX and SXIII, demonstrate how automation and robots can help manufacturers bring their operations back home to the UK. Reshoring can be achieved with cost- and energy-efficiency as well as productivity benefits — even if, as Ozzy sang, things “ain't the same.”
To learn more about Shibaura Machine’s robots for injection moulding, visit its website.
The content & opinions in this article are the author’s and do not necessarily represent the views of RoboticsTomorrow
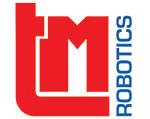
TM Robotics (Americas) Inc
TM Robotics, in partnership with Shibaura Machine, formerly known as Toshiba Machine until 1st April 2020, offers a comprehensive range of industrial robots ideally suited for high-precision assembly, machine loading/unloading and material-handling applications that can be dust proof, clean room, or IP65/67. The company's extensive product line starts with a Cartesian solution available in thousands of combinations from single actuators to four-axis solutions; six-axis solutions that can include precise vision-control; and a complete range of SCARAs from low cost to the industry-leading SCARA with 1200-mm reach that can carry up to 20 kgs. TM Robotics sells and services robots throughout Europe, the Middle East, India, Russia, and Africa, as well as North, Central, and South America, from headquarters in Hertfordshire, England and Elk Grove Village, IL, USA. For more information, visit www.tmrobotics.com or follow us on Twitter, LinkedIn and YouTube.
Other Articles
Giving lens cleaning cloths a robotic hand - Robotic automation for textile processing
Investing in the UK’s injection moulding sector - The case for all-electric machines and robotic integration
Robotic solutions for pharmaceutical packaging - Automated system addresses key limitations of manual processes
More about TM Robotics (Americas) Inc
Comments (0)
This post does not have any comments. Be the first to leave a comment below.
Featured Product
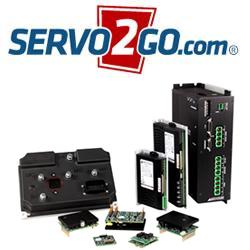