In this guide, we'll explore the benefits of using painting robots and their applications in various industries. Additionally, we'll guide you through the process of sourcing the right paint robot for your needs.
Painting Robots: Benefits, Applications, and Sourcing Tips
Klajd Lika | Bota Systems
A perfect paint job is an excellent indicator of a high-quality manufactured product. But achieving a flawless coating isn't easy — especially in high-volume production. That's where painting robots come in.
Whether you want to enhance the quality of your products, accelerate production times, or create a safer working environment, paint robots offer many benefits that can transform your facility.
In this guide, we'll explore the benefits of using painting robots and their applications in various industries. Additionally, we'll guide you through the process of sourcing the right paint robot for your needs.
What Is a Painting Robot?
Spraying robots are equipped with advanced automation technology and are programmed to follow precise paths and apply paint with remarkable consistency.
Whether you want to paint delicate furniture pieces or large automotive parts, spray painting robots can paint various surfaces.
Benefits of Painting Robots
1. Unmatched Consistency
Regardless of their experience and expertise, human painters can experience slight variations in the painting technique, leading to inconsistencies in the paint finish. Painting robots aren't susceptible to the same issue. They can replicate the same motions with unparalleled precision, ensuring every product is coated evenly.
They can replicate the same motions often with sub-millimeter accuracy because they rely on pre-programmed instructions that guide brush strokes, paint application thickness, and spray patterns.
This consistency eliminates the need for paint reworks due to paint runs, sags, or incomplete coverage, enhancing the finish of manufactured products and customer satisfaction.
2. Enhanced Efficiency
Unlike human painters who work at variable speeds and require breaks, painting robots can operate at constant speeds, tirelessly. Additionally, spray paint robots paint faster than human workers, with some sophisticated models of painting surfaces at top speeds of up to 1000mm/sec. That's exceptionally faster than human painters.
These capabilities translate to increased production output, allowing you to meet tight deadlines and fulfill large orders easily.
3. Minimized Waste
Traditional painting methods often involve overspray, resulting in wasted paint and increased costs. Spraying robots are programmed for precise application, minimizing overspray and ensuring paint only reaches intended areas.
As a result, paint robots reduce paint waste by up to 30% while promoting sustainability by decreasing the environmental impact of manufacturing.
4. Improved Worker Safety
Working with paints can expose workers to hazardous fumes and chemicals. Painting robots eliminate this concern. They can handle harmful materials without risk of exposure, creating a safer workplace for your employees.
Additionally, paint robots can access hard-to-reach areas, reducing the need for workers to maneuver into potentially dangerous positions.
The safety features robots have can improve your teams’ satisfaction, as over nine out of ten employees consider physical safety a top priority within the workplace.
Additionally, enhanced safety can make your organization a more attractive employer, as nearly eight out of ten individuals are more likely to join or stay with a company that prioritizes workplace safety.
5. Improved Flexibility and Scalability
Painting robots aren't one-size-fits-all machines. You can program them to perform various painting tasks. Whether you want to paint small intricate parts or large objects, there's a paint robot suited to your needs. This adaptability allows you to adjust quickly to new product lines without significant downtime when reconfiguring your production line.
Furthermore, scaling up production becomes easier — you can simply add more robots to your production line to match increased demand.
6. Reduced Labor Costs and Training Requirements
While the cost of industrial robots has steadily declined over the past two decades, they still cost thousands of dollars. Nonetheless, although the upfront cost of painting robots might appear steep, the potential for significant long-term savings is considerable.
By automating the painting process, you can reduce reliance on manual labor, potentially lowering your labor costs. For instance, one Chinese company ITOCHU Logistics reduced labor costs by over 50% by implementing robots into its workflow.
Moreover, you can reduce the need for specialized training in painting techniques, as paint robots can handle complex tasks.
Uses of Painting Robots
Automotive Industry
Spray painting robots have been a staple in the automotive industry since the early 1980s. They are ubiquitous on many production lines, and automakers use them to apply paint to car bodies, hoods, doors, and other components.
For example, the Mazda Motor Corporation has used a unique vehicle body painting robot that moves horizontally and vertically to apply paint to vehicle components since the 1980s.
The precision of spray painting robots ensures uniform paint application, resulting in a flawless finish that's tough to achieve manually.
Furthermore, painting robots can easily handle complex shapes and surfaces of automotive parts, ensuring every surface is perfectly coated.
Aerospace Industry
The aerospace industry requires rigorous attention to detail during every stage of the manufacturing process, and painting isn't an exception. Aircraft components require specialized coatings for corrosion resistance, durability, and aerodynamic efficiency.
Painting robots excel at this, applying critical coatings with unmatched precision and consistency. This accuracy is vital to the safety and performance of aircraft.
For instance, to enhance the accuracy and speed of the painting process, Boeing uses robot painters to paint its aircraft. The system is known as the Automated Spray Method (ASM), and the company acknowledges it's a massive improvement over human painters.
Furniture and Home Appliances
Paint robots have transformed the furniture industry, ensuring a consistent, high-quality finish on various furniture components, such as cabinets, beds, tables, chairs, and dressers. Their versatility has enabled manufacturers to switch between different materials, such as wood, metal, and plastic, with ease.
Similarly, in appliance manufacturing, robots ensure a flawless finish on various appliances, such as refrigerators, washing machines, and ovens.
SRG Global Inc., headquartered in Warren, Michigan, employs over 50 painting robots to paint components for the household appliance and automotive industries.
Consumer Electronics
The consumer electronics industry is incredibly fast-paced, with manufacturers releasing new models of laptops, smartphones, and other electronics every so often. Robots can accommodate the rapid changes in production cycles by applying consistent, scratch-resistant coatings that are durable and attractive.
Xiaomi has a smart factory that almost entirely relies on robots to produce its smartphones, with an estimated annual production capacity of about 10 million devices.
Customized Applications
Beyond these industries, painting robots are also making inroads into other sectors like construction and healthcare.
In construction, paint robots are used to paint large structures like bridges, industrial tanks, and wind turbine blades. Their ability to access hard-to-reach areas and handle harsh environments makes them perfect for this application.
In the healthcare industry, robots ensure a sterile and evenly coated finish on delicate instruments.
Sourcing Painting Robots
Define Your Needs
First, determine what you need from a paint robot. Consider the size and complexity of the items you want painted, the types of paint or coatings you'll use, and the production volume. Understanding these requirements will help you narrow down the options and focus on robots suitable for your needs.
Research Robot Manufacturers
Once you determine your needs, scout potential manufacturers. Look for manufacturers with a proven track record producing robotic painting systems and those that offer support and service arrangements.
Comparing different manufacturers will give you insight into the various products they offer, as well as pricing. Don't hesitate to request demonstrations or visit facilities to see the robots firsthand.
Some popular painting robot manufacturers include:
Consider Integration and Compatibility
Bearing that in mind, here are some key factors to consider:
-
Payload capacity: This refers to the weight the robot's arm can handle. Ensure it can handle the weight of your materials and the paint applicator.
-
Reach: The robot's arm should be able to access all the areas you need to paint.
-
Programming ease: Consider how intuitive the robot's programming software is and whether your team might require extensive training to use the software.
Evaluate Training and Support
Consider Costs
If you want to integrate a spraying robot into your operations, weigh the cost of acquiring one against the potential cost savings.
Plan for the Future
Force Torque Sensors for Paint Robots
These sensors provide real-time feedback on the forces and torques experienced by the robot's end-effector, allowing for adjustments to be made dynamically during the painting process.
By incorporating force torque sensors, painting robots can achieve even greater consistency in paint application, ensuring uniform coverage across a variety of surfaces and geometries.
Moreover, these sensors contribute to improved safety by enabling robots to detect unexpected collisions or obstacles, preventing damage to both the equipment and surrounding environment.
As industries continue to embrace automation for enhanced productivity and quality, the integration of force torque sensors with painting robots emerges as a pivotal advancement, offering unprecedented levels of control and performance in automated painting applications.
The content & opinions in this article are the author’s and do not necessarily represent the views of RoboticsTomorrow
Comments (0)
This post does not have any comments. Be the first to leave a comment below.
Featured Product
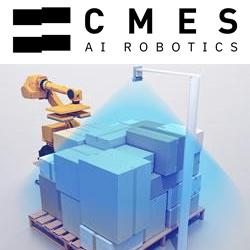