Smarter tech for safer food
Food safety has been one of the top priorities for food manufacturers and consumers for many years. In fact, the 2016 food manufacturing outlook report by US magazine Food Processing found that a quarter of manufacturers considered it their top priority. Here, Shan Zhan, Global Business Manager for Food & Beverage within the ABB Control Technologies business unit, explains how smart technologies are helping manufacturers exceed food safety standards.
There has been an alarming number of food recalls in recent years. In the US alone, the past ten years have seen recalls increase by 250 per cent according to a global food safety report from Swiss Re. This rate shows no signs of slowing down, as the US food and drug administration (FDA) also issued a total of 764 recalls in 2016 — an increase of 22 per cent from the previous year.
This issue is by no means exclusive to the US. Across Europe, a total of 847 alerts were transmitted using the European Unions rapid alert system for food and feed (RASFF) in 2016. An alert in this instance indicates that food presenting a serious risk has made it to market and urgent action, such as a recall, is required.
These statistics make it clear that, while food safety is a top priority, there is still a considerable amount of tainted produce that makes it to market. In particular, the majority of these tainted products are contaminated with pathogens — usually Listeria, E. Coli and Salmonella.
Food production managers must then identify the source of this contamination and act accordingly. This is becoming an easier task to manage with the rise of smart technologies in food plants, particularly smart manufacturing execution systems (MES), that allow for easier tracing of ingredients through the supply chain by connecting to food measurement and analyzer products and providing real-time data transfer.
For example, pathogens such as E Coli contaminate raw food ingredients through exposure to the feces of animals carrying the bacteria. With an effective MES that provides accurate, real-time genealogy tracking and analysis of ingredients, production managers receive an alert and can quickly identify which batch was carrying the bacteria and then work backwards through the chain. This information is then transferred to external systems to quickly notify plant personnel.
Production managers can also cross-reference this to determine whether the cause of the contamination is due to the source of ingredients or contaminated equipment. While an increasing number of production facilities are using sanitized food processing robots to maximize hygiene and reduce contamination, some plants still use equipment prone to bacterial contamination. Identifying this is a critical step in properly addressing the issue.
Smart technology is enabling plant and production managers to do this quicker and with a higher degree of accuracy, preventing the risk and cost of a product recall while ensuring regulatory compliance with industry standards and best practices.
Food safety will likely always remain the top priority for food production managers across the globe. With the rise of smart technologies and intelligent systems in food manufacturing plants, businesses can manage safety standards and compliance in an easier and more streamlined fashion.
Featured Product
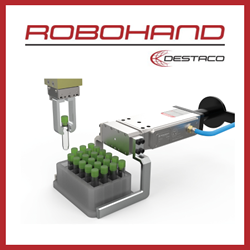