MHS wins SDCE 100 recognition for UPS hub expansion
Award recognizes advanced automated solution for parcel super hub
(Mt. Washington, Ky.) July 8, 2020 - MHS (www.mhsglobal.com), a single-source provider of material handling automation and software solutions, announces its recognition on Supply and Demand Chain Executive's list of innovative supply chain projects. The company earned its place on the 2020 SDCE 100 for the design and implementation of high-performance automated systems in the expanded UPS ground operations hub at its Louisville Centennial campus.
MHS completed the project six months ahead of schedule and more than doubled the now one-million-square-foot facility's throughput to 85,000 packages per hour. The solution includes two separate systems to accommodate significant package variety, one for small parcels and another for large, irregularly shaped packages. Several miles of conveyor and multiple scan tunnels support the sorters and provide data for control software to direct package routing.
"Winning recognition on the SDCE 100 is an incredible honor, as is having such an exceptional customer," says Pat Cowgill, senior vice president, MHS. "Our relationship with them allowed us to deliver a system that met all business requirements and got them up and running ahead of schedule."
With the hub operating on a 24/7 schedule and the project including retrofits, new equipment installation and integration, MHS used a phased approach to minimize disruption. This allowed UPS to reap the benefits of an interim boost in capacity before the project was completely finished, expanding from 39,000 to 60,000 parcels per hour during the 2018 peak season. And when UPS expressed interest in expediting the project timeline, an experienced field service team worked overtime to get the project completely finished and online in April 2019 - six months ahead of the original schedule. Today, UPS considers the facility a super hub, one of their 10 largest ground-sorting facilities in the world.
About MHS
Founded in 1999, MHS Global is a full-service provider of innovative material handling systems that solve the challenges of distribution and fulfillment operations. We take a comprehensive, customer-centric approach that includes custom engineering, design, manufacturing and turnkey integration services. Our quality solutions leverage a broad range of controls and automated equipment, including but not limited to sorters, conveyors, extendable loading and unloading systems. We provide complete, responsive support to maintain systems for peak performance, with predictive analytics and local technicians to maximize long-term value and return on investment.
MHS has a global installed base of over $5 billion for small to large distribution and fulfillment projects in a variety of industries, including e-commerce, parcel, third party logistics and outside integrators.
# # #
Media contact:
Dan Gauss, Koroberi
336.409.5391
Dan@koroberi.com
Company contact:
Lauren Pedley, MHS
502.645.6199
Lauren.Pedley@mhsglobal.com
Featured Product
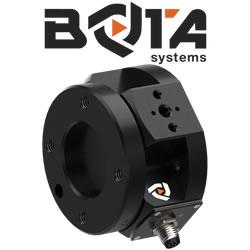
Bota Systems - The SensONE 6-axis force torque sensor for robots
Our Bota Systems force torque sensors, like the SensONE, are designed for collaborative and industrial robots. It enables human machine interaction, provides force, vision and inertia data and offers "plug and work" foll all platforms. The compact design is dustproof and water-resistant. The ISO 9409-1-50-4-M6 mounting flange makes integrating the SensONE sensor with robots extremely easy.
No adapter is needed, only fasteners! The SensONE sensor is a one of its kind product and the best solution for force feedback applications and collaborative robots at its price. The SensONE is available in two communication options and includes software integration with TwinCAT, ROS, LabVIEW and MATLAB®.