UltraFlex induction soldering a 4-part brass assembly within 12 seconds
This demo scenario set up by UltraFlex proved the significant efficiency of induction soldering - time- and cost-wise. In addition to being efficient, this soldering process had also been perfectly precise and also clean.
The energy-, time- and cost-efficient induction soldering process for a 4-part brass assembly has recently been demonstrated by UltraFlex Power Technologies. UltraFlex is a leading manufacturer of advanced, digitally controlled induction heaters and frequently demonstrates the efficiency of induction heating for a variety of industrial applications.
In a requested demo, a potential customer from the Oil & Gas industry was looking to evaluate the results and induction heating parameters for a brass assembly soldering application. The soldered workpiece would be used as a capillary type of thermometer filled with silicon oil. Hence, to avoid oil leakage, the soldering would have to be perfectly accomplished while still pursuing the customer's goal to minimize the soldering time and costs.
UltraFlex induction soldering engineers considered an UltraFlex induction heater from the UltraHeat SM-5 series as the most efficient and cost-effective choice for this application. UltraHeat SM is a compact 5 kW induction heater operating with either a water-cooled or air-cooled remote heat station. It features adaptive digital phase control providing efficient operation in a wide frequency range.
The induction soldering process had been completed in 2 steps. In the first step the brass pin base had been soldered to the brass ribs and the entire assembly then inserted into the brass case. In the step that followed, the cap was inserted into the brass case, flux had been applied between the parts to be joined and simultaneous soldering of the cap to the brass case and the brass ribs assembly had been done.
The two soldering steps had been completed within a total of 10 to 12 seconds. The result had been strong and reliable joints, the quality of which was tested with compressed air.
This demo scenario set up by UltraFlex proved the significant efficiency of induction soldering - time- and cost-wise. In addition to being efficient, this soldering process had also been perfectly precise and also clean. Moreover, when implemented on the line, it would ensure consistent, repeatable results, with no dependency on the operator skills. Finally, induction soldering is safe - safe for the operator, safe for the environment, due to the lack of open flame, smoke and noxious emissions.
Find out more at:
https://ultraflexpower.com/
Contact us at:
+1.631.467.6814
uptnews@ultraflexpower.com
About UltraFlex Power Technologies:
UltraFlex Power Technologies (ultraflexpower.com) offers the most advanced and innovative digitally controlled induction heating equipment in the industry. Its compact modular and flexible systems are used for a wide variety of induction heating, casting and melting applications.
Featured Product
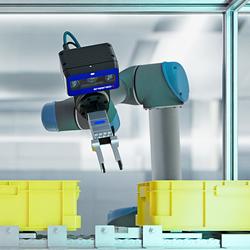