UltraFlex demonstrates automated robotic induction brazing for copper to brass assemblies
This demonstration proved that the customer could successfully replace torch brazing with induction brazing. He could also take advantage of automation to increase his productivity rates and achieve consistent and high-quality brazing results every time, regardless of an operator's skills.
A demo showcasing the usage of a robotic arm to accomplish automated induction brazing for copper and brass parts has recently been set up by UltraFlex per request of a customer. The customer - a manufacturer from the HVAC industry - was looking to replace his current torch-based brazing process for various sized copper and brass HVAC parts and increase productivity by reducing the heat cycle times.
UltraFlex has a practice of setting up demonstrations proving the time-, energy- and cost-efficiency of induction heating compared to traditional, torch-based brazing. This demo setup aimed at defining the specific heating parameters for the induction heating process and the results the customer could achieve.
The demo was set up for 2 copper to brass joints that had to be brazed one after the other, using UltraFlex Dragon 15/20 brazing robot. Dragon 15/20 integrates the Ultraflex W15 (15 kW) induction heating system with a Universal Robots cobot (UR 5) to achieve a fully automated brazing process. The integrated induction coil mounted directly onto the robotic arm is capable of reliably brazing multiple joints by applying controllable heat precisely positioned by the robotic arm.
In this heating process, the robot held the induction coil at the first specified brazing position. Heating was then applied until the first braze was completed. The robotic arm then moved onto the second brazing position, holding the coil there and applying heat until the second braze was completed. At 8 kW of power used, the target brazing temperature of ~800° F (~427° C) was achieved within mere a few seconds for each joint. The entire automated heat cycle, for both joints, took about 20 seconds.
This demonstration proved that the customer could successfully replace torch brazing with induction brazing. He could also take advantage of automation to increase his productivity rates and achieve consistent and high-quality brazing results every time, regardless of an operator's skills.
The automated induction-based brazing process would be energy- and cost-efficient, as well as completely safe for the environment, due to the lack of open flame, smoke and noxious emissions.
Find out more at:
https://ultraflexpower.com/
Contact us at:
+1.631.467.6814
uptnews@ultraflexpower.com
About UltraFlex Power Technologies:
UltraFlex Power Technologies (ultraflexpower.com) offers the most advanced and innovative digitally controlled induction heating equipment in the industry. Its compact modular and flexible systems are used for a wide variety of induction heating, casting and melting applications.
Featured Product
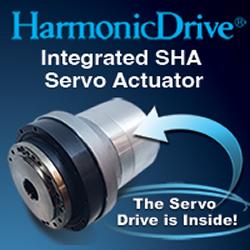