FANUC Introduces New DR-3iB/6 STAINLESS Delta Robot for Primary Food Handling at Automate 2022
FANUC Will Demonstrate Its Latest Robots, Cobots and Factory Automation
FANUC America, the world leader in CNCs, robotics, and ROBOMACHINEs, will introduce the new DR-3iB/6 STAINLESS delta robot for primary food handling at
Automate 2022, June 6-9 in Detroit, in booth #3323. FANUC will also demonstrate its latest products including the new CRX cobot series and CR-35iB collaborative robot, the new M-1000iA heavy-payload robot, the new LR-10iA/10 material handling robot for machine tending and warehousing applications, and much more.
NEW FANUC DR-3iB/6 STAINLESS Delta Robot
The new DR-3iB/6 STAINLESS is FANUC's first stainless steel food-grade delta robot for picking and packing primary food products. Rated IP69K, the robot meets USDA and FDA food safety standards, and sets a new benchmark for robotic food handling in terms of payload, speed, reach and sanitation.
The DR-3iB/6 STAINLESS features a fully enclosed stainless steel body that is resistant to the chemicals and high pressure/temperatures required in strict wash down environments. The robot's mirror-like surface finish ensures that any microbial contaminants can be washed away cleanly. With additional features such as NSF H1 food grade lubricant, secondary oil catch basins (with viewing windows to monitor potential leaks), self-draining surfaces, and many other small details driven by USDA/FDA standards, the DR-3iB/6 STAINLESS is ideally suited for primary food handling applications.
"The new DR-3iB/6 STAINLESS robot combines FANUC's industry-leading performance and reliability with a food-safe stainless steel construction," said Jessica Juhasz, staff engineer, FANUC America. "We're happy to offer a food processing robot that will help companies maximize production efficiencies without compromising food safety."
The DR-3iB/6 STAINLESS has a 1200mm reach (400mm height) and a powerful four-axis design allowing it to handle 6kg payloads at high speeds. The new robot operates with FANUC's latest R-30iB Plus controller with integrated intelligent functions such as iRVision®, Force Sensing, Robot Link, Collision Guard and Zero Down Time (ZDT).
At the show, the new DR-3iB/6 STAINLESS delta robot using a Soft Robotics gripper will pick bakery, dairy and meat products from the middle section of the demonstration's work area and place them in specified zones.
COBOT ZONE: CRX and CR Cobot Demonstrations
FANUC recently expanded its popular series of CRX collaborative robots with the new CRX-5iA, CRX-20iA/L and CRX-25iA. The new CRX cobots complement FANUC's existing line of CR and CRX cobots that now total 11 model variations able to handle products from 4 to 35kg. Designed for companies looking to increase their capabilities and overcome labor issues, FANUC's CRX cobots are extremely robust and can run for up to eight years without maintenance.
FANUC will demonstrate a wide range of CRX cobots to address a variety of industrial applications.
The new CRX-5iA cobot, featuring a 5kg payload and 994mm reach will make its first appearance in North America at Automate. The CRX-5iA will pick and assemble small gears using integrated force control. First, the CRX-5iA with integrated force control will pick different height gears (short and tall) from a stack. Using the "touch skip" feature, the cobot will determine the height of each gear. Next, the CRX-5iA will assemble the selected gear using integrated force control's "Phase search" function.
A CRX-10iA welding cobot will allow attendees to teach weld joints using hand guidance or a tablet interface with drag and drop icons. The CRX welding cobot supports FANUC's advanced features including iRVision, Torch Angle Control, Touch Sensing and Thru Arc Seam Tracking (TAST). The CRX will use Lincoln Electric's Power Wave® R450 robotic power source, and the new Lincoln Electric Smart Torch. Built for the industrial space, the CRX-10iA welding cobot is compatible with Lincoln Electric's weld programs to help customers maximize productivity.
A new CRX-25iA robot, offering a 25kg payload and 1,889mm reach will demonstrate case palletizing. Guided by a 3DV/200 vision sensor mounted to the arm, the CRX-25iA will palletize boxes to nearly 7' high.
A CRX-20iA/L with FANUC QSSR (Quick & Simple Start-up of Robotization) will demonstrate the easy connection of a FANUC CRX cobot and a machine tool. QSSR simplifies the automation of machine tool load/unload applications using the CNC controller's easy guidance functionality for quick connectivity, start-up and operation.
NEW FANUC CR-35iB - Bicycle Assembly
FANUC's new CR-35iB collaborative robot with a 35kg payload can work in a variety of applications that typically require lift assist devices or custom equipment. In addition to being the industry's strongest cobot, the CR-35iB has a large work envelope, and small installation footprint, making it ideal for tight spaces. A more streamlined and lighter mechanical unit includes FANUC's latest sensor technology for safety.
At Automate, the CR-35iB will help an operator assemble a bicycle. The operator will program various assembly positions with the easy-to-use tablet TP featuring a "drag and drop" user interface. The demonstration underscores the cobot's ability to make the assembly process quicker while eliminating ergonomic stress.
NEW FANUC M-1000iA Robot - Battery Assembly
The new M-1000iA robot is capable of handling very heavy products including automotive components, construction materials and battery packs for electric vehicles. At Automate, the M-1000iA equipped with iRVision will highlight the EV battery assembly process.
The M-1000iA's serial-link construction allows a wider range of motion in every direction. It can extend its arm upright or rotate it backwards, which is not possible for typical heavy-payload robots with a parallel-link mechanism. With a 1000 kg payload, a 3,253mm horizontal reach, and a 4,297mm vertical reach the M-1000iA is a good choice to help manufacturers increase output and maximize efficiency.
NEW FANUC LR-10iA/10 Robot: Vision-Guided Piece Picking
FANUC's new LR-10iA/10 robot is designed for machine tending and many picking applications found in the warehousing and logistics markets. Weighing just 46 kg, the LR-10iA/10 robot mounts to the floor, upside down, or on an angle. It's also very easy to mount the robot to an AGV or other mobile platform.
The LR-10iA/10 has a 10 kg payload and a large work envelope with a long reach of 1,101 mm. Its compact size accommodates tight floor spaces, and a slim arm fits easily into machine tools for part load/unload. In addition, an enclosed structure makes it easy to integrate, and an IP67 rating allows it to operate in environments with dust, water and oil mist.
A new FANUC LR-10iA/10 robot guided by four 3DV/400 vision sensors mounted over the workcell will pick various combinations of products from four separate totes to demonstrate order fulfillment. When the order tote is completed, it moves to the opposite side of the cell, where an LR Mate 200iD robot picks and places each item back onto the conveyor, sorting them by color to refill the pick totes.
More Robotic Demonstrations at Automate
M-2000iA/1700L: Handles a Chevrolet Corvette
FANUC's M-2000iA robot series is ideal for automotive and other large component manufacturers with super heavy-payload applications looking to reduce costs associated with conventional conveyors and lifting devices.
At Automate, the FANUC M-2000iA/1700L will handle a 2020 Chevrolet Corvette to demonstrate how assembled automotive bodies are commonly handled in automotive OEM facilities.
The demonstration will also feature Dual Check Safety (DCS) Speed and Position Check software, which limits the robot's envelope within a compact workspace.
Paint Mate 200iA Robot: Visual Tracking
The FANUC Paint Mate 200iA is a flexible and compact six-axis paint robot with a 5kg payload and 892mm reach. Ideal for small paint booths, the Paint Mate's versatile mounting options include floor, wall, inverted or at an angle. The Paint Mate is part of a series of painting robots designed and built by FANUC in Rochester Hills, Michigan since 1982.
At Automate, the Paint Mate 200iA robot will use iRVision 3DV and line tracking to paint ACT test panels placed randomly on a conveyor. First, the integrated robot vision system identifies the part type and orientation. Next the robot's HVLP spray gun simulates painting the part. The demonstration highlights the robot's ability to quickly adapt to randomly-oriented or shifting parts.
R-2000iD/210FH Robot: Automotive Spot Welding
The FANUC R-2000iD/210FH is part of an extensive family of industrial robots offering a variety of payloads and reaches. The robot offers a compact design with a hollow arm for better cable management, which minimizes interference with system equipment and allows the robot to operate in tight workspaces. Featuring a 210kg payload and 2,605mm reach, the R-2000iD/210FH is ideal for spot welding and material handling applications.
At the show, the R-2000iD/210FH robot equipped with integrated FANUC Servo Gun Control and a hollow arm for spot welding dress out will perform simulated spot welding in and around a truck cab.
SR-12iA SCARA Robot: Packing and Unpacking
FANUC's family of 4-axis SCARA robots includes the SR-3iA, SR-6iA, SR-12iA, and SR-20iA models with 3kg, 6kg, 12kg and 20kg payload capacities, and a 400mm - 1,100mm reach, respectively. FANUC's SCARA robots are designed to help customers increase productivity in a number of industries including consumer goods, batteries and other auto components, plastics, lab automation, appliances and medical devices.
The small SR-3iA and SR-6iA SCARAs have a compact footprint and space-saving design for maximum efficiency. The higher-payload SR-12iA and SR-20iA robots provide flexibility with a large vertical stroke, and an Environmental Option for withstanding moisture and dusty conditions.
At the show, FANUC's SR-12iA SCARA robot will pack and unpack four-packs of two liter pop bottles. The demonstration shows the SR-12iA's ability to handle heavy products in a wide operating area at high speeds.
Factory Automation Demonstrations at Automate
Linear Motor Demo
See our new Linear Motor demo arranged in an X/Y table application. FANUC's LiS-B series linear motors have set new standards for acceleration, precision and speed, delivering high gain and rigidity with excellent path accuracy. Unlike conventional drives, these motors work without any force transmission mechanisms, making machine design and maintenance easier (no ball screws, no backlash). The linear design enables rigid long-stroke axes, increased thrust force and multi-head configurations by arranging multiple coil sliders on a single magnet track.
Panel i Industrial PC Wall
See all the industrial PC options FANUC provides for its CNCs at the Panel i Industrial PC demo. Designed with the latest technology, these industrial PCs provide a powerful platform for custom developments and are available in a variety of display options. Plus, if you have legacy PCs, check out our Panel i Upgrade program to keep your operations safe from cyberattacks.
FANUC experts will participate in a variety of conferences, panel discussions and advanced courses at Automate. For more information visit.
About FANUC America Corporation
FANUC America Corporation is a subsidiary of FANUC CORPORATION in Japan, and provides industry-leading CNC systems, robotics and factory automation. FANUC's innovative technologies and proven expertise help manufacturers meet their goals to improve productivity, maximize profits and remain competitive.
Our culture of "Service First" means customer service is our highest priority. We are committed to supplying customers with parts and support for the life of their FANUC products.
FANUC America is headquartered at 3900 W. Hamlin Road, Rochester Hills, MI 48309, with facilities throughout the Americas. For more information, please call: 888-326-8287 or visit www.fanucamerica.com . Also, connect with us on YouTube, Twitter, Facebook, LinkedIn and Instagram.
Featured Product
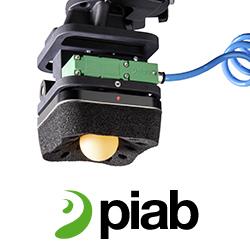
The piCOBOT Electric vacuum generator
Fully electric, slim design and absence of air-tubing and cabling. The new piCOBOT® Electric heads towards another success for Piab's piCOBOT® program. A secondary effect of these achievements is the absence of entangling air tubing and cabling. It simplifies the installation, and as the new piCOBOT® Electric only needs a single connection on the cobot arm, the clean set-up allows a completely unrestricted movement. The new piCOBOT® Electric package will contain plug & play software to fit UR e-series cobots, but many other useful adaptations will be introduced in the coming year