Application story: UltraFlex induction brazing magnetic steel ice skates, ensuring minimum oxidation
The demo application proved that by using an advanced, digitally controlled UltraFlex induction heater and optimizing the brazing process, the customer could automate the process, ensure repeatability, and achieve high-quality results, independent of operator skills.
UltraFlex Power Technologies, a leading manufacturer of innovative, digitally controlled induction heating solutions, recently demonstrated their low-oxidation induction brazing process for magnetic steel ice skates. The demo was conducted for a customer who already used induction for their brazing processes and was looking to achieve lower oxidation for the brazing process on three positions of the magnetic steel skate surface.
UltraFlex engineers recommended the UltraFlex SOLO Induction Heating System as the most appropriate solution for this application. The UltraFlex SOLO Systems feature a unique Direct Digital Step™ control algorithm, are air-cooled and compact, and have configurable output power from 12kW to 32kW. These systems leverage the latest SiC MOSFET transistor technology and patented digital control algorithms to deliver optimal performance and maximum efficiency in a wide frequency range.
During the demo, silver brazing alloy provided by the customer was used, and brazing flux was applied to minimize oxidation. Several heating tests were conducted to identify the best heating parameters for the customer's scenario. Applying 5 kW power, it took up to 30 seconds to complete the brazing process for each joint. However, the tests revealed that the coil position was impacting an area beyond the joint, which required a custom induction coil design to minimize oxidation.
To further reduce oxidation, UltraFlex recommended using argon blown above the joint to remove oxidizing air and cool down the skate. The demo application proved that by using an advanced, digitally controlled UltraFlex induction heater and optimizing the brazing process, the customer could automate the process, ensure repeatability, and achieve high-quality results, independent of operator skills. The induction brazing process was energy-efficient and safe for the operator and the environment, with no flames or noxious emissions.
Find out more at:
https://ultraflexpower.com/
Contact us at:
+1.631.467.6814
uptnews@ultraflexpower.com
About UltraFlex Power Technologies:
UltraFlex Power Technologies (ultraflexpower.com) offers the most advanced and innovative digitally controlled induction heating equipment in the industry. Its compact modular and flexible systems are used for a wide variety of induction heating, casting and melting applications.
Featured Product
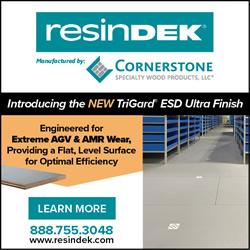